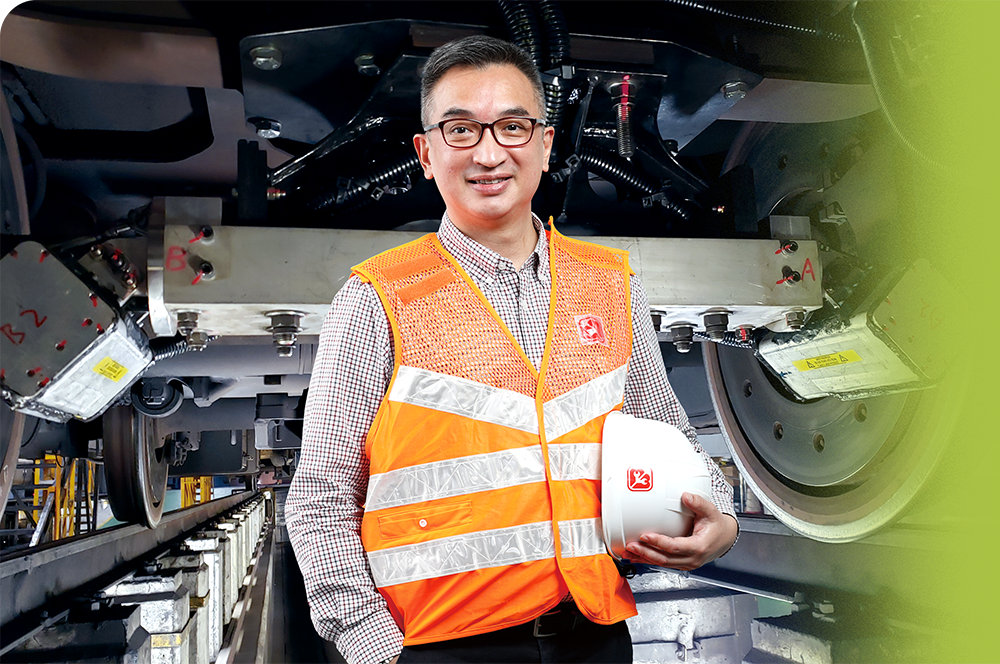
Staying Calm to Co-ordinate Major Railway Incident Investigation
Major incident investigations are never easy, as onsite situations are unpredictable and the evidences must be gathered promptly. Railways Branch Senior Engineer Mr Li Yick-fai, Ernest, recalls how he co-ordinates the investigation into the MTR Hung Hom Station derailment incident.
On 17 September 2019, at the time when Mr Li Yick-fai, Ernest, Senior Engineer of the Railways Branch (RB), returned to the EMSD Headquarters for work, he received a call about a serious incident, in which an East Rail Line (EAL) train had derailed while entering Hung Hom Station. He ran into the office to gather colleagues and rushed to the scene with about ten people. Ernest is a veteran in handling electrical and gas incidents as he has served in various posts in the EMSD. Although he was nervous, Ernest could still remain calm in the face of this serious incident, the firstever derailment of an EAL train carrying passengers.
The site of the incident was extensive, making the investigation and evidence collection even more complicated and difficult. “First, we had to gauge the situation of the scene to ascertain how serious the incident was, and whether there were casualties. Then we had to determine how services were affected and what might have caused the incident. We did a quick tabulation of parts and equipment on site, and the degree of damage to the tracks, and then checked if any CCTV systems near the Station had captured footage of the incident. Additionally, we had to gather relevant information for the Secretary for Transport and Housing and our Director to make responses to media enquiries, as well as co-ordinating with the MTR Corporation Limited (MTRCL) on their repair plans and work flow,” Ernest recalled.
While the RB team was conducting on-site evidence collection, the MTRCL carried out repairs. Train services at Hung Hom Station partially resumed by 6 a.m. the next morning. Repairs continued for several nights after EAL services had finished for the day. Throughout this period, Ernest and his colleagues took turns to monitor the repairs and testing of key components including track gauge, welded joints, sleepers, and point machines at turnouts. A test run with an empty train was also carried out to confirm the safe and smooth operation of the service. The team approved a full resumption of services by the MTRCL through the affected rail section only after all the test data was satisfactory.
After the incident, the RB sought assistance from overseas experts experienced in investigating major railway incidents. Subsequently, the “Technical Investigation Report on Train Derailment Incident at Hung Hom Station on MTR East Rail Line” was released in March 2020, which recommended a number of improvement measures for the MTRCL to implement, so as to ensure that similar incidents would not happen again.
Ernest said, “As a regulator, the EMSD focuses on using our expertise to protect public safety. Upon completion of the report, we kept monitoring the MTRCL’s implementation of the recommended remedial measures. Since this serious incident, the RB has stepped up its regulatory work to ensure railway safety and to regain public confidence in our railway systems.”
The site of the incident was extensive, making the investigation and evidence collection even more complicated and difficult. “First, we had to gauge the situation of the scene to ascertain how serious the incident was, and whether there were casualties. Then we had to determine how services were affected and what might have caused the incident. We did a quick tabulation of parts and equipment on site, and the degree of damage to the tracks, and then checked if any CCTV systems near the Station had captured footage of the incident. Additionally, we had to gather relevant information for the Secretary for Transport and Housing and our Director to make responses to media enquiries, as well as co-ordinating with the MTR Corporation Limited (MTRCL) on their repair plans and work flow,” Ernest recalled.
While the RB team was conducting on-site evidence collection, the MTRCL carried out repairs. Train services at Hung Hom Station partially resumed by 6 a.m. the next morning. Repairs continued for several nights after EAL services had finished for the day. Throughout this period, Ernest and his colleagues took turns to monitor the repairs and testing of key components including track gauge, welded joints, sleepers, and point machines at turnouts. A test run with an empty train was also carried out to confirm the safe and smooth operation of the service. The team approved a full resumption of services by the MTRCL through the affected rail section only after all the test data was satisfactory.
After the incident, the RB sought assistance from overseas experts experienced in investigating major railway incidents. Subsequently, the “Technical Investigation Report on Train Derailment Incident at Hung Hom Station on MTR East Rail Line” was released in March 2020, which recommended a number of improvement measures for the MTRCL to implement, so as to ensure that similar incidents would not happen again.
Ernest said, “As a regulator, the EMSD focuses on using our expertise to protect public safety. Upon completion of the report, we kept monitoring the MTRCL’s implementation of the recommended remedial measures. Since this serious incident, the RB has stepped up its regulatory work to ensure railway safety and to regain public confidence in our railway systems.”
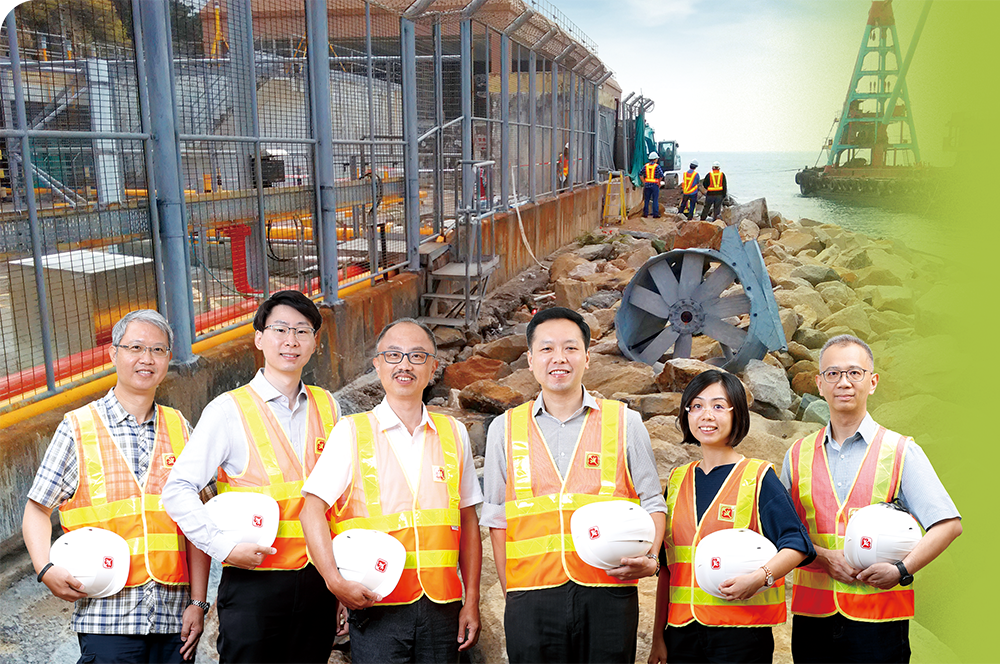
Learn from the Experience and be Well-prepared to Enhance the Safety of Near-shore Gas Storage Facilities
This team from our Gas Standards Office co-ordinated an inter-departmental group to expedite the recovery of a seawall near an LPG storage facility in Ap Lei Chau, severely damaged by super typhoon Manghkut. The works also improved safety for the community. Ms Laura Ngai and Mr Anthony Leung share the story.
During the passage of super typhoon Mangkhut on 16 September 2018, the seawall at Lee Nam Road, Ap Lei Chau, was battered by huge waves and high winds, resulting in unprecedented damage to an LPG storage facility nearby. Settlement occurred at part of the facility and a peripheral structure had to be demolished due to serious structural damage. While assessment results suggested that the damage did not pose gas safety hazards nor affect gas supply, the facility owner should repair and reinforce the facility before the next typhoon season arrives. In view of this, the Gas Standards Office (GasSO) of the EMSD took the lead to form an interdepartmental working group with the Buildings Department, the Civil Engineering and Development Department, the Drainage Services Department and the Lands Department to render assistance to the facility owner. Members of the working group met on a bi-weekly basis to co-ordinate relevant tasks and expedite the monitoring and approval of repair works. GasSO engineers Ms Ngai Nga-man, Laura, and Mr Leung Kwan-kit, Anthony, spearheaded the tasks.
“As Hong Kong’s Gas Authority, the EMSD attaches great importance to maintaining gas safety. Thus, we took the initiative to co-ordinate the inter-departmental working group and communicate closely with other departments. Thanks to their unfailing support, the assistance of our experienced colleagues and supervisors, the on-site supervision of our inspectors as well as the efforts of the facility owner, the complicated approval processes and repair works were completed swiftly within just six months,” Laura said.
During the works period, Laura, Anthony and the GasSO team closely liaised with the facility owner to explore the most practicable reinforcement solutions, such as introducing settlement measuring devices to monitor the settlement risk of the LPG pipes and storage tanks near the collapsed grounds, reinforcing and moving inland a gas supply main of 200 mm diameter, installing wire meshes with high durability and aluminium panels to a sea-facing water boiler room to shield it from strong winds and debris, etc. The team also reminded the facility owner to maintain sufficient spare parts for timely replacement in the future.
“Thanks to the collaborative efforts of our team, the LPG supply to about 8000 households in the neighbourhood was unaffected throughout the works period. The facility is now sturdier to withstand future typhoons. Learning from this experience, we immediately conducted a comprehensive risk assessment of all LPG storage facilities in Hong Kong and urged owners of near-shore gas storage facilities to make reference to the reinforcement works of the facility at Ap Lei Chau, including the provision of similar protective measures to their sea-facing installations, trimming of tree branches before the typhoon season to prevent damage of facilities due to fallen trees, etc.,” Anthony said.
Collaboration between the GasSO team and the Ap Lei Chau facility owner kept the LPG storage facility safe and ensured that all repair and reinforcement works were completed before the typhoon season in July 2019. At the same time, owners of other near-shore facilities drew reference from the works of the Ap Lei Chau facility and adopted precautions against heavy wind. Together, we will ride out the storms ahead.
“As Hong Kong’s Gas Authority, the EMSD attaches great importance to maintaining gas safety. Thus, we took the initiative to co-ordinate the inter-departmental working group and communicate closely with other departments. Thanks to their unfailing support, the assistance of our experienced colleagues and supervisors, the on-site supervision of our inspectors as well as the efforts of the facility owner, the complicated approval processes and repair works were completed swiftly within just six months,” Laura said.
During the works period, Laura, Anthony and the GasSO team closely liaised with the facility owner to explore the most practicable reinforcement solutions, such as introducing settlement measuring devices to monitor the settlement risk of the LPG pipes and storage tanks near the collapsed grounds, reinforcing and moving inland a gas supply main of 200 mm diameter, installing wire meshes with high durability and aluminium panels to a sea-facing water boiler room to shield it from strong winds and debris, etc. The team also reminded the facility owner to maintain sufficient spare parts for timely replacement in the future.
“Thanks to the collaborative efforts of our team, the LPG supply to about 8000 households in the neighbourhood was unaffected throughout the works period. The facility is now sturdier to withstand future typhoons. Learning from this experience, we immediately conducted a comprehensive risk assessment of all LPG storage facilities in Hong Kong and urged owners of near-shore gas storage facilities to make reference to the reinforcement works of the facility at Ap Lei Chau, including the provision of similar protective measures to their sea-facing installations, trimming of tree branches before the typhoon season to prevent damage of facilities due to fallen trees, etc.,” Anthony said.
Collaboration between the GasSO team and the Ap Lei Chau facility owner kept the LPG storage facility safe and ensured that all repair and reinforcement works were completed before the typhoon season in July 2019. At the same time, owners of other near-shore facilities drew reference from the works of the Ap Lei Chau facility and adopted precautions against heavy wind. Together, we will ride out the storms ahead.
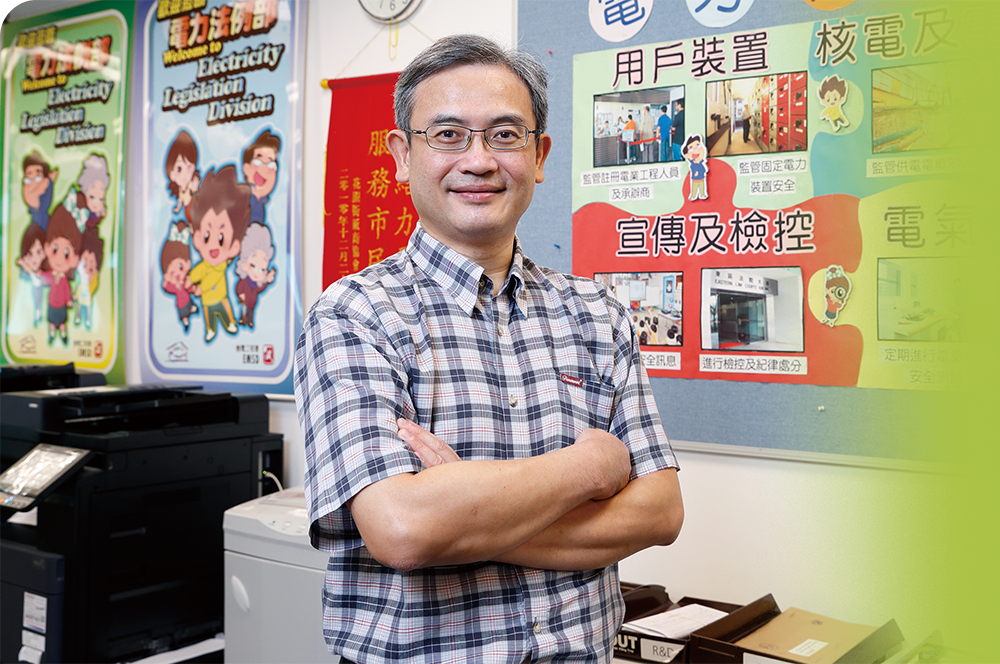
Promoting Electrical Safety with the EMSD for Four Decades
Mr Pang Nai-tai has served more than 22 years at the Electricity Legislation Division and worked in all of its sub-divisions. He shares his experiences from his almost 40-year long career at the EMSD, most of which was devoted to promoting electrical safety.
Mr Pang Nai-tai began his career with the EMSD as an apprentice and rose through the ranks to become a Senior Electrical Inspector before his retirement in July 2020. Throughout his service of nearly 40 years with the EMSD, he served more than 22 years at the Electricity Legislation Division (ELD) and worked in each of its four subdivisions, undertaking nearly all of its functions, including inspection, monitoring, investigation, evidence gathering, publicity, prosecution, etc., thereby contributing to the electrical safety of Hong Kong.
From 1997 to 2006, Mr Pang was posted to the Electrical Products Sub-division, where he participated in shop inspections, with the aim of monitoring and promoting electrical product safety, so as to ensure compliance with the Electrical Products (Safety) Regulation. He also took part in investigation and evidence gathering for electrical incidents. Among the handled cases, one was a fatal electrocution incident involving an air-conditioning technician who was dismantling an air-conditioner. During investigation, he discovered that the cable of the appliance was compressed during installation and subsequently damaged during removal. As the cable was still energised during the process, the metal frame of the air-conditioner was live, resulting in the fatal accident. Mr Pang also found that the building’s responsible persons failed to correctly label the switches. He promptly reminded the responsible contractor to carry out regular inspections in strict accordance with the relevant ordinance to prevent similar incidents in future.
His next stint was with the Publicity and Prosecution Sub-division from 2006 to 2010. Apart from handling prosecution cases based on the evidence collected by other sub-divisions, he was also involved in a range of promotional activities, with a view to enhancing public awareness of electrical safety by means of non-law enforcement work.
After posting outside of the ELD between 2010 and 2012, Mr Pang, having been promoted, returned to the Nuclear and Utility Safety Sub-division of the ELD in 2012. One of the key responsibilities of Mr Pang was to inspect construction sites to prevent workers from damaging underground cables during their works. He was also responsible for reminding the trade and workers through various channels such as seminars to adopt safety measures to protect both the cables and the workers. Besides, this Sub-division was also responsible for ensuring that the electromagnetic field of the power companies’ pylons were in compliance with the World Health Organization’s regulations. As a member of the inter-departmental emergency response team for the Daya Bay Nuclear Power Station, this Sub-division participated in the regular meetings and drills to maintain effective teamwork and agility to deal with incidents. Mr Pang was thankful that the emergency response team did not need to be activated during this time.
In mid-2019, Mr Pang was transferred to the Consumer Installations Sub-division, where he took up the duties of monitoring annual inspections of fixed electrical installations and the registration of generating facilities to tie in with the implementation of the Feed-in Tariff Scheme, which motivated members of the public to install renewable energy generating facilities. Mr Pang was also involved in facilitating the understanding of and compliance with the relevant electrical safety requirements by generating facility owners and the trade while contributing to sustainability.
Devoted most of his career to promoting electrical safety, Mr Pang was delighted to observe a continuing reduction in electrical incidents in the territory before his retirement.
From 1997 to 2006, Mr Pang was posted to the Electrical Products Sub-division, where he participated in shop inspections, with the aim of monitoring and promoting electrical product safety, so as to ensure compliance with the Electrical Products (Safety) Regulation. He also took part in investigation and evidence gathering for electrical incidents. Among the handled cases, one was a fatal electrocution incident involving an air-conditioning technician who was dismantling an air-conditioner. During investigation, he discovered that the cable of the appliance was compressed during installation and subsequently damaged during removal. As the cable was still energised during the process, the metal frame of the air-conditioner was live, resulting in the fatal accident. Mr Pang also found that the building’s responsible persons failed to correctly label the switches. He promptly reminded the responsible contractor to carry out regular inspections in strict accordance with the relevant ordinance to prevent similar incidents in future.
His next stint was with the Publicity and Prosecution Sub-division from 2006 to 2010. Apart from handling prosecution cases based on the evidence collected by other sub-divisions, he was also involved in a range of promotional activities, with a view to enhancing public awareness of electrical safety by means of non-law enforcement work.
After posting outside of the ELD between 2010 and 2012, Mr Pang, having been promoted, returned to the Nuclear and Utility Safety Sub-division of the ELD in 2012. One of the key responsibilities of Mr Pang was to inspect construction sites to prevent workers from damaging underground cables during their works. He was also responsible for reminding the trade and workers through various channels such as seminars to adopt safety measures to protect both the cables and the workers. Besides, this Sub-division was also responsible for ensuring that the electromagnetic field of the power companies’ pylons were in compliance with the World Health Organization’s regulations. As a member of the inter-departmental emergency response team for the Daya Bay Nuclear Power Station, this Sub-division participated in the regular meetings and drills to maintain effective teamwork and agility to deal with incidents. Mr Pang was thankful that the emergency response team did not need to be activated during this time.
In mid-2019, Mr Pang was transferred to the Consumer Installations Sub-division, where he took up the duties of monitoring annual inspections of fixed electrical installations and the registration of generating facilities to tie in with the implementation of the Feed-in Tariff Scheme, which motivated members of the public to install renewable energy generating facilities. Mr Pang was also involved in facilitating the understanding of and compliance with the relevant electrical safety requirements by generating facility owners and the trade while contributing to sustainability.
Devoted most of his career to promoting electrical safety, Mr Pang was delighted to observe a continuing reduction in electrical incidents in the territory before his retirement.

Regional Digital Control Centre: Vision Comes to Life
Mr So Pok-man, Patrick, and his team are responsible for the design and implementation of the EMSD’s first Regional Digital Control Centre with an aim to achieve E&M digitisation and lay the foundation for building a smart city.
Standing in front of the huge light-emitting diode dashboard in the EMSD’s first Regional Digital Control Centre (RDCC) is like being in a sci-fi movie. Graphical visualisations of operational data, tracking everything from the energy efficiency performance of air-conditioning systems to the status of lifts and escalators, can be called up and analysed to enable rapid troubleshooting, more effective predictive maintenance and even real-time facility management.
Overseeing the implementation of this pilot RDCC is Mr So Pok-man, Patrick, an engineer of the General Engineering Services Division (GESD). This RDCC will eventually be connected to 400 major government buildings maintained by the GESD, each with annual electricity consumption of over 500000 kWh, to monitor and optimise their E&M systems’ energy efficiency and operational performance.
“RDCC is one of the initiatives under the second EMSTF Five-year Strategic Plan,” Mr So noted. In 2018, he and his team were tasked with turning the RDCC vision into reality. As the concept was new and no off-the-shelf solution was available, the team partnered with a start-up to work on design and implementation. The RDCC began operations in February 2020.
“In the long run, RDCC is the way forward for the management of smart buildings,” Mr So said. The EMSTF also has the unique advantage of having access to a rich database of government building E&M facilities, especially from newer buildings that have deployed integrated Building Management Systems in the past five to seven years. Once integrated with machine learning and artificial intelligence, the database will generate useful digital tools to help make buildings smarter and greener. Both the hardware and software have been designed to run on an open platform so that all future EMSD RDCCs can communicate with each other.
Overseeing the implementation of this pilot RDCC is Mr So Pok-man, Patrick, an engineer of the General Engineering Services Division (GESD). This RDCC will eventually be connected to 400 major government buildings maintained by the GESD, each with annual electricity consumption of over 500000 kWh, to monitor and optimise their E&M systems’ energy efficiency and operational performance.
“RDCC is one of the initiatives under the second EMSTF Five-year Strategic Plan,” Mr So noted. In 2018, he and his team were tasked with turning the RDCC vision into reality. As the concept was new and no off-the-shelf solution was available, the team partnered with a start-up to work on design and implementation. The RDCC began operations in February 2020.
“In the long run, RDCC is the way forward for the management of smart buildings,” Mr So said. The EMSTF also has the unique advantage of having access to a rich database of government building E&M facilities, especially from newer buildings that have deployed integrated Building Management Systems in the past five to seven years. Once integrated with machine learning and artificial intelligence, the database will generate useful digital tools to help make buildings smarter and greener. Both the hardware and software have been designed to run on an open platform so that all future EMSD RDCCs can communicate with each other.

Racing Against Time to Convert Chun Yeung Estate
Mr Tang Choi-chin participated in the on-site preparation works, such as Towngas water heater installation, at the Chun Yeung Estate quarantine centre. With the experience of fighting against SARS in 2003, he is proficient in taking part in the anti-epidemic preparation works this time.
On Chinese New Year’s Eve in January 2020, Mr Tang Choi-chin, a chief technical officer of our Health Sector Division, received a call from his senior asking him to quickly assemble a team to get ready to convert a new but unoccupied housing estate into a COVID-19 quarantine centre as requested by the DH. Mr Tang, with experience in building negative pressure wards during the SARS outbreak in 2003, mobilised a team overnight and took immediate action. Unfortunately, a number of facilities in the housing estate were promptly vandalised. Hence, the newly converted quarantine units could not be put into operation.
Chun Yeung Estate in Fo Tan, another new housing estate, was soon identified for conversion. Mr Tang needed to mobilise an inter-divisional team to commence the work there at full steam on 9 February 2020. “The EMSTF’s role was to install more than 16000 light bulbs in around 3200 units, and to install and test around 3200 gas water heaters, one in each unit by phases,” he said.
Time was tight, and first-phase installation had to be completed by 19 February 2020 when the first batch of Hong Kong residents on board the Diamond Princess cruise ship, was expected to return to Hong Kong on a Government-chartered flight for their 14-day quarantine at the Estate. “It turned out that testing the gas water heaters was the biggest challenge,” Mr Tang recalled. “Though Towngas had provided manpower to help install the water heaters, it was necessary for the EMSTF team to conduct the testing, which was time consuming.”
According to Mr Tang, the Government’s inter-departmental drill exercise code-named Jadeite in 2012 to test contingency actions in the event of a virus outbreak, proved highly valuable in 2020. “Thanks to the drill I participated eight years ago, I was able to equip team members this time with the necessary knowledge and resolve infection control concerns that some had,” he said.
The conversion at Chun Yeung Estate was completed on time. “Our colleagues’ team spirit of mutual trust and seamless collaboration in this cross-divisional mission was most impressive. Exercise Jadeite also proves the value of training and the importance of passing on experience,” Mr Tang concluded.
Chun Yeung Estate in Fo Tan, another new housing estate, was soon identified for conversion. Mr Tang needed to mobilise an inter-divisional team to commence the work there at full steam on 9 February 2020. “The EMSTF’s role was to install more than 16000 light bulbs in around 3200 units, and to install and test around 3200 gas water heaters, one in each unit by phases,” he said.
Time was tight, and first-phase installation had to be completed by 19 February 2020 when the first batch of Hong Kong residents on board the Diamond Princess cruise ship, was expected to return to Hong Kong on a Government-chartered flight for their 14-day quarantine at the Estate. “It turned out that testing the gas water heaters was the biggest challenge,” Mr Tang recalled. “Though Towngas had provided manpower to help install the water heaters, it was necessary for the EMSTF team to conduct the testing, which was time consuming.”
According to Mr Tang, the Government’s inter-departmental drill exercise code-named Jadeite in 2012 to test contingency actions in the event of a virus outbreak, proved highly valuable in 2020. “Thanks to the drill I participated eight years ago, I was able to equip team members this time with the necessary knowledge and resolve infection control concerns that some had,” he said.
The conversion at Chun Yeung Estate was completed on time. “Our colleagues’ team spirit of mutual trust and seamless collaboration in this cross-divisional mission was most impressive. Exercise Jadeite also proves the value of training and the importance of passing on experience,” Mr Tang concluded.
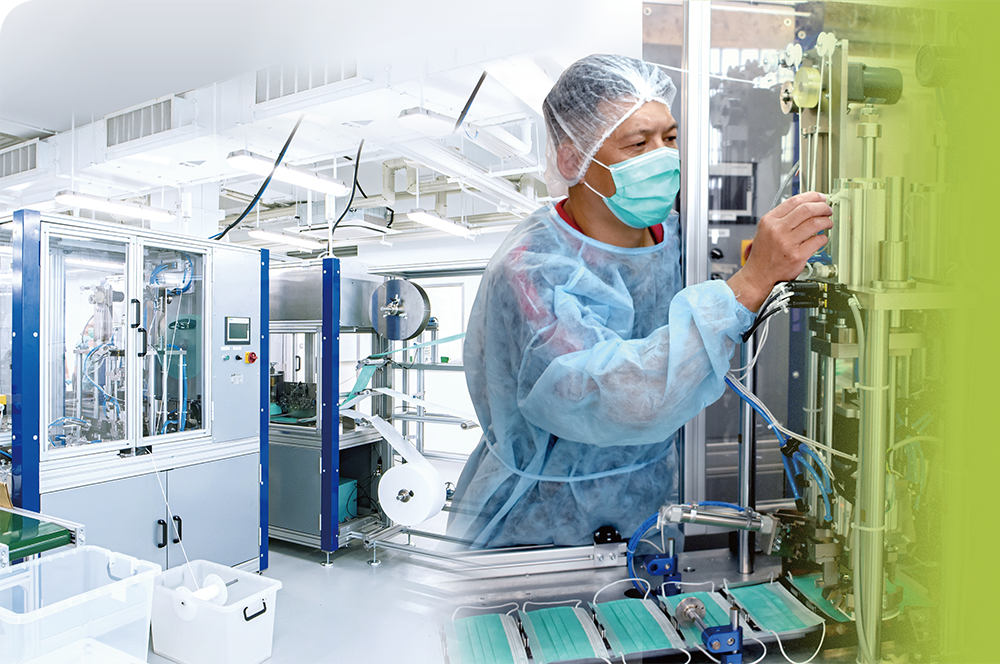
Close Encounters with Face Mask Machines
Mr Wu Tai-suen and his team support the maintenance work of mechanical facilities at Lo Wu Correctional Institution. They have overcome all technical obstacles and equipped themselves with skills of assembly, testing and commissioning of mask-making machines in a short time to ensure reliability and high productivity of the machines.
Demand for surgical masks suddenly shot up after the COVID-19 outbreak in January 2020. In early February 2020, Mr Wu Tai-suen, a works supervisor II at the Security and Vehicle Services Division, who heads up the resident team responsible for mechanical systems maintenance at Lo Wu Correctional Institution, was tasked with installing and calibrating several new mask-making machines from the Mainland to cope with increasing demand.
“Installing and calibrating mask-making machines was new to us” said Mr Wu. “The machines were of different types and origins, with no operating manuals. What’s more, the technical person who was supposed to come to Hong Kong to set the machines up had his trip postponed due to the Mainland lockdown.” What followed was a few months of challenging work and a steep learning curve, drawing on the team’s mechanical experience, online research and advice from local trade partners and manufacturers familiar with mask machines.
“The biggest challenge was calibrating the earloop machines,” he explained. Each mask-making machine comes with two earloop machines, each churning out 40 earloops per minute. The earloops must be of the right tensile strength so the mask can cover the face snugly, and calibration of the machine is important to make sure the earloops are not too tight or too loose. As the mask and earloop machines must operate 24x7 at high speed to satisfy demand, this heavy use meant they had to be calibrated often and their parts replaced frequently. “We soon realised that though the machines are not involved with high tech, the mask-making steps are complex and the specification requirements are actually very high,” he recalled. “Luckily, we got the hang of it after a while and managed to find locally all the spare parts we need.”
Mr Wu’s team had to work round the clock in shifts in those months to keep the machines running, which was on top of normal maintenance duties for the CSD. Any insight from the experience? “What looks simple, may not be simple at all. There is always something new to learn,” Mr Wu concluded.
“Installing and calibrating mask-making machines was new to us” said Mr Wu. “The machines were of different types and origins, with no operating manuals. What’s more, the technical person who was supposed to come to Hong Kong to set the machines up had his trip postponed due to the Mainland lockdown.” What followed was a few months of challenging work and a steep learning curve, drawing on the team’s mechanical experience, online research and advice from local trade partners and manufacturers familiar with mask machines.
“The biggest challenge was calibrating the earloop machines,” he explained. Each mask-making machine comes with two earloop machines, each churning out 40 earloops per minute. The earloops must be of the right tensile strength so the mask can cover the face snugly, and calibration of the machine is important to make sure the earloops are not too tight or too loose. As the mask and earloop machines must operate 24x7 at high speed to satisfy demand, this heavy use meant they had to be calibrated often and their parts replaced frequently. “We soon realised that though the machines are not involved with high tech, the mask-making steps are complex and the specification requirements are actually very high,” he recalled. “Luckily, we got the hang of it after a while and managed to find locally all the spare parts we need.”
Mr Wu’s team had to work round the clock in shifts in those months to keep the machines running, which was on top of normal maintenance duties for the CSD. Any insight from the experience? “What looks simple, may not be simple at all. There is always something new to learn,” Mr Wu concluded.
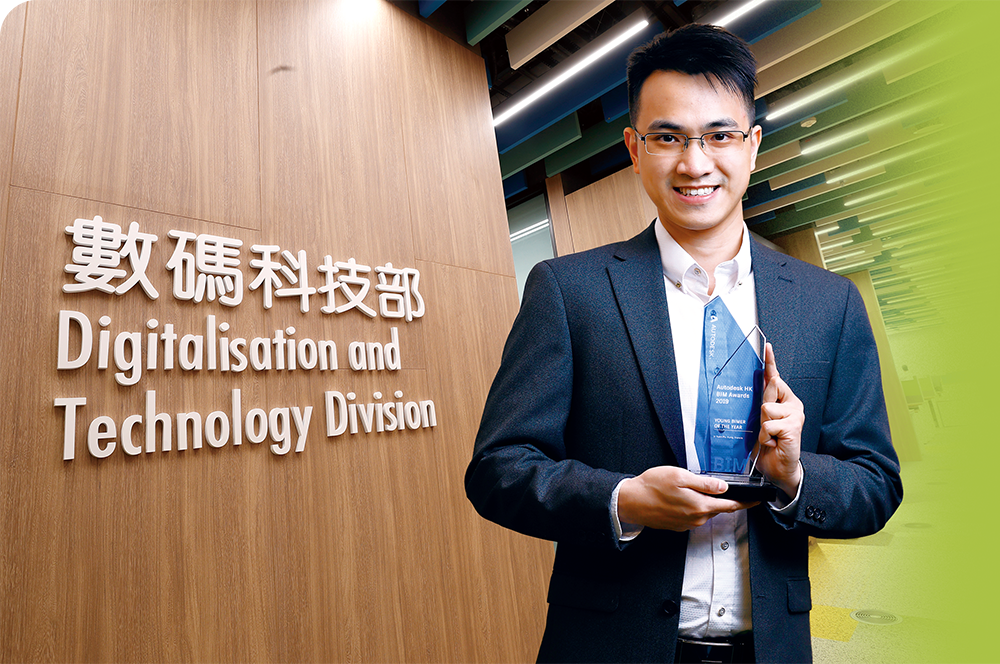
Hong Kong Young Public Officers to Work at the United Nations as Chinese Personnel
Mr Yuen Piu-hung, Francis, an engineer who has been involved in the development of BIM-AM projects since 2014, was awarded the “Young BIMer of the Year” in 2019, a recognition of his contribution in the development of BIM-AM in the trade.
It all began in December 2018, when Mr Yuen Piu-hung, Francis, an engineer of the Digitalisation and Technology Division, received an email notice from the Civil Service Bureau via his head of grade. It was a call from the Government for young public officers to take part in the United Nations (UN) Junior Professional Officer (JPO) Programme. Successful candidates would be posted to UN agencies in the US or Europe to work as JPOs for two years as Chinese personnel. After talking to his wife, who was very supportive, Mr Yuen put in his application.
“Competition was keen,” he said. After going through a series of interviews in Hong Kong, shortlisted candidates were invited to Beijing in July 2019 for a one-week training on China’s national policies, foreign affairs and governance strategies. Candidates’ performance in the training formed part of the assessment.
Mr Yuen and another EMSD engineer were two of five young public officers from the Government eventually recommended by the Ministry of Foreign Affairs of the People's Republic of China to participate in the UN’s JPO Programme. Mr Yuen will be working in the UN office in Geneva for two years. “I am really looking forward to this unique opportunity to gain more experience in a multi-cultural environment with diverse perspectives and considerations,” he said.
“Competition was keen,” he said. After going through a series of interviews in Hong Kong, shortlisted candidates were invited to Beijing in July 2019 for a one-week training on China’s national policies, foreign affairs and governance strategies. Candidates’ performance in the training formed part of the assessment.
Mr Yuen and another EMSD engineer were two of five young public officers from the Government eventually recommended by the Ministry of Foreign Affairs of the People's Republic of China to participate in the UN’s JPO Programme. Mr Yuen will be working in the UN office in Geneva for two years. “I am really looking forward to this unique opportunity to gain more experience in a multi-cultural environment with diverse perspectives and considerations,” he said.

Making the most of the “Golden Two Hours” in Railway Maintenance to Ensure Passenger Safety
As the city sleeps, Railways Branch Engineer Ms Chan Ching-man, Kitty, is often working in the early hours of the morning to monitor MTR railway maintenance works. She explains the importance of the 2 a.m. to 4 a.m. "golden two-hour" window in ensuring railway safety.
Trained as an electrical engineer, Ms Chan Ching-man, Kitty, did not expect to be on call round the clock since she first joined the EMSD’s Railways Branch in October 2018. Since railway maintenance has to be completed within the “golden two-hour” window between 2 a.m. and 4 a.m., i.e. the short period of time during which MTR train services have ended and are yet to resume, Kitty has to be on site during this period, whenever there are maintenance works for the railway system, to ensure that the works are conducted in accordance with the relevant guidelines and procedures.
Kitty’s team is responsible for the matters relating to the East Rail Line (EAL) and its extension from Hung Hom to Admiralty. While the works on the new section can be done during the day, all works involving the operating section have to be conducted within the two-hour window at night. “Even seemingly minor railway incidents involve extensive maintenance and monitoring works. Due to the EAL’s relatively long history and open-air rails, it is prone to having emergency incidents such as cracks on rails, which requires us to be present to monitor the repair process late at night when the train services have ended,” Kitty said.
In addition to the routine railway safety inspections and the hectic regulatory work in preparing the new section of the EAL for commissioning, Kitty’s team has to conduct vetting and on-site testing in relation to the replacement of the signalling system of the EAL, as well as handle other railway-related emergency incidents. As a result, Kitty has to work at night five to six times a month on average. She once even worked at night three times in a week, travelling to distant areas such as Sheung Shui and Fanling. At first, her family was worried about her safety for having to leave home alone at night. Taxi drivers are often perplexed by why she has to travel by herself from urban Kowloon to a remote railway station that is already closed. However, Kitty has now gotten used to this work arrangement. Interestingly, her son, now in primary school, loves to listen to stories about her overnight “adventures” at work.
In order to meet operational needs, Kitty never switches off her mobile phone and is always ready for her job. “The emergency calls from the MTR Operations Control Centre always put me under pressure. While the pressure for frontline maintenance personnel stems from the tight timeframe and the challenging working environment, our pressure arises from our official duties as the regulator. We have to carefully monitor the entire repair process, so as to ensure railway safety. Only when the railway services resume normal and passengers are able to travel smoothly, will I truly have peace of mind,” Kitty said.
Kitty’s team is responsible for the matters relating to the East Rail Line (EAL) and its extension from Hung Hom to Admiralty. While the works on the new section can be done during the day, all works involving the operating section have to be conducted within the two-hour window at night. “Even seemingly minor railway incidents involve extensive maintenance and monitoring works. Due to the EAL’s relatively long history and open-air rails, it is prone to having emergency incidents such as cracks on rails, which requires us to be present to monitor the repair process late at night when the train services have ended,” Kitty said.
In addition to the routine railway safety inspections and the hectic regulatory work in preparing the new section of the EAL for commissioning, Kitty’s team has to conduct vetting and on-site testing in relation to the replacement of the signalling system of the EAL, as well as handle other railway-related emergency incidents. As a result, Kitty has to work at night five to six times a month on average. She once even worked at night three times in a week, travelling to distant areas such as Sheung Shui and Fanling. At first, her family was worried about her safety for having to leave home alone at night. Taxi drivers are often perplexed by why she has to travel by herself from urban Kowloon to a remote railway station that is already closed. However, Kitty has now gotten used to this work arrangement. Interestingly, her son, now in primary school, loves to listen to stories about her overnight “adventures” at work.
In order to meet operational needs, Kitty never switches off her mobile phone and is always ready for her job. “The emergency calls from the MTR Operations Control Centre always put me under pressure. While the pressure for frontline maintenance personnel stems from the tight timeframe and the challenging working environment, our pressure arises from our official duties as the regulator. We have to carefully monitor the entire repair process, so as to ensure railway safety. Only when the railway services resume normal and passengers are able to travel smoothly, will I truly have peace of mind,” Kitty said.
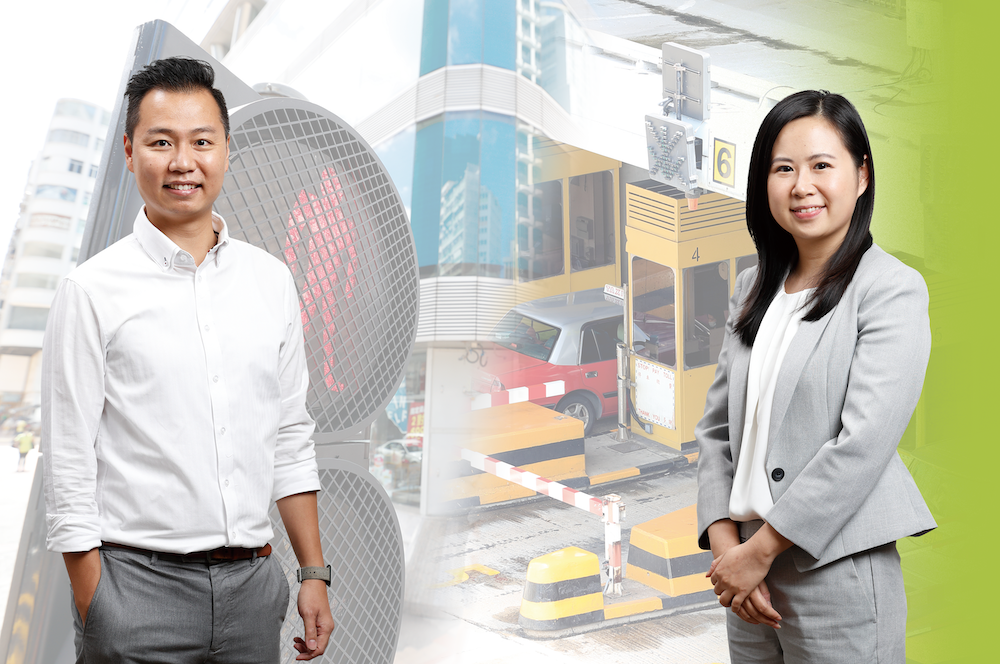
Restoring Normality to Traffic Lights and Cross-Harbour Tunnel
The series of public order events taken place in the second half of 2019 in Hong Kong resulted in extensive damage to a large number of public facilities. Ms Chan Ying-ying, Dorothy, a senior engineer, and Mr Chan Kin-hong, Keith, an engineer, both under the Boundary Crossing Facilities and Transport Services Division, remained dedicated and led our colleagues to make strenuous efforts to repair damaged traffic lights and the Cross-Harbour Tunnel for the public.
By mid-2019, Mr Chan Kin-hong, Keith, an engineer of the Boundary Crossing Facilities and Transport Services Division (BTSD), had been running its traffic lights maintenance unit for six years. Yet his team had never had to repair as many traffic lights as it would have to do in the second half year of 2019, when lights at some 750 road junctions were vandalised.
“The fact that we exhausted ten years’ supply of spare parts in just a few months shows the scale of the repair works,” said Mr Chan. Supported by several contractors, his team worked through numerous nights to repair traffic lights so that as many as possible could resume operation early next morning to ensure public safety. Some traffic light controllers were damaged too, which posed complications as road works would be necessary to replace the underground electric wiring. After months of hard work, all traffic junctions were back to operation by December 2019, and all repairs completed by July 2020. Protective measures were added to traffic lights and controllers at strategic locations as a precaution.
Meanwhile, BTSD senior engineer Ms Chan Ying-ying, Dorothy, led a team to repair the E&M facilities of the Cross-Harbour Tunnel, severely damaged in November 2019. Ms Chan co-ordinated and collaborated with various government departments and led a 100-plus EMSD team on-site. The Government’s target was to complete all repairs within 100 hours after site clearance.
“To make the most of precious time, we developed a rapid recovery plan and began repair works immediately after a half-day on-site assessment,” she recalled. Essential tasks were identified, such as resuming the normal operation of the toll systems, carrying out health checks for all E&M tunnel systems and finding enough spare parts for all repairs. “Sourcing spare parts was a challenge,” she said. Thanks to the help from other government departments and trade partners, the team got the spare parts needed for restoring systems. After working at full speed, all repairs were completed on schedule, and the tunnel was re-opened smoothly at 5 a.m. on 27 November 2019.
Ms Chan felt proud that the team had contributed to making life convenient for the public, which demonstrated EMSTF’s core service value and commitment.
“The fact that we exhausted ten years’ supply of spare parts in just a few months shows the scale of the repair works,” said Mr Chan. Supported by several contractors, his team worked through numerous nights to repair traffic lights so that as many as possible could resume operation early next morning to ensure public safety. Some traffic light controllers were damaged too, which posed complications as road works would be necessary to replace the underground electric wiring. After months of hard work, all traffic junctions were back to operation by December 2019, and all repairs completed by July 2020. Protective measures were added to traffic lights and controllers at strategic locations as a precaution.
Meanwhile, BTSD senior engineer Ms Chan Ying-ying, Dorothy, led a team to repair the E&M facilities of the Cross-Harbour Tunnel, severely damaged in November 2019. Ms Chan co-ordinated and collaborated with various government departments and led a 100-plus EMSD team on-site. The Government’s target was to complete all repairs within 100 hours after site clearance.
“To make the most of precious time, we developed a rapid recovery plan and began repair works immediately after a half-day on-site assessment,” she recalled. Essential tasks were identified, such as resuming the normal operation of the toll systems, carrying out health checks for all E&M tunnel systems and finding enough spare parts for all repairs. “Sourcing spare parts was a challenge,” she said. Thanks to the help from other government departments and trade partners, the team got the spare parts needed for restoring systems. After working at full speed, all repairs were completed on schedule, and the tunnel was re-opened smoothly at 5 a.m. on 27 November 2019.
Ms Chan felt proud that the team had contributed to making life convenient for the public, which demonstrated EMSTF’s core service value and commitment.
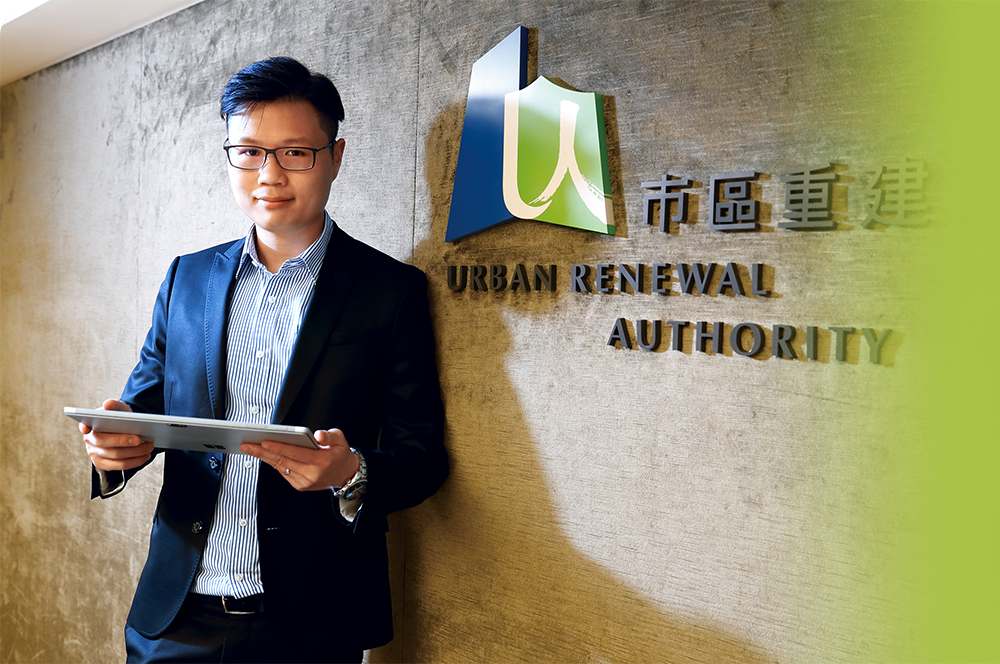
On Secondment to Help with Lift Modernisation in Community
Mr Cheung Ka-yu, Gary, Engineer of the General Legislation Division, has been seconded to the Urban Renewal Authority since August 2018 to support the implementation of the Government’s Lift Modernisation Subsidy Scheme. This is an account of his unusual assignment.
To enhance lift safety and further protect public safety, the Government has launched the Lift Modernisation Subsidy Scheme (LIMSS) to provide financial incentives and appropriate professional support for building owners in need to modernise their aged lifts. The LIMSS has been implemented in partnership with the Urban Renewal Authority (URA), which serves as the scheme’s administrator.
While the URA has considerable experience in implementing subsidy schemes for the rehabilitation of old buildings, the EMSD has the expertise of lift works as well as a sound understanding of the lift industry. Therefore, the EMSD deployed a professional team to the URA to provide technical support for the LIMSS. The partnership aims to ensure that the scheme is people-oriented and fairly conducted, taking into consideration the capacity of the lift industry. Mr Cheung Ka-yu, Gary, an Electrical and Mechanical Engineer of the General Legislation Division, together with a Senior Electrical and Mechanical Engineer, has been seconded to the URA since August 2018 to help with the drawing up of the details of the LIMSS and its implementation. Gary said, “Initially, the scheme had only a framework. Our first and foremost task was to finalise the details, including the scope of subsidy, setting of priorities, application details, etc., with a view to receiving the first round of applications in the first quarter of 2019.” With the concerted efforts of the team, the first round of applications was launched as scheduled.
Two rounds of applications were arranged, with overwhelming responses. About 1200 applications involving about 5000 lifts were received in the first round, which was close to the original target of the LIMSS. “In the past, owners might hesitate to upgrade their lifts due to financial considerations and a lack of technical knowledge and organisational capacity when implementing lift modernisation works. The introduction of the LIMSS can help them expedite the progress of lift modernisation,” Gary said.
Apart from working out the details of the LIMSS, Gary also applied his professional knowledge about lifts to help the URA recruit a resident consultant and prepare standard tender documents for lift modernisation works to ensure that every project would meet the relevant technical and safety standards. “To ensure smooth implementation and one-stop support for participating building owners, we took into consideration multiple factors when working out the technical details of the tender documents, including maintenance arrangements upon completion of modernisation works,” Gary added. Technical issues aside, the team also had to take on the challenges of how to minimise the inconvenience inevitably caused to residents, especially the elderly, in buildings with only one lift or lifts serving alternate floors, when their lifts were out of service for several months. “After discussions and joint studies with the Development Bureau (DEVB) and the URA, it was decided that the LIMSS would provide support services in this aspect, including delivery of meals, purchasing daily necessities on residents’ behalf, and provision of mechanised stair climbing devices,” Gary said.
Challenges continued to emerge. The second round of applications was launched in January 2020 during the COVID-19 outbreak. In the light of the epidemic, many owners’ corporations were unable to hold general meetings to discuss if they should join the LIMSS. “We have to be prepared to resolve problems come what may. As building owners could not meet to pass resolutions about applying for the LIMSS, we have, after discussions with the DEVB and the URA, decided to streamline the application process and allow flexibility for building owners to join the scheme by “submitting application forms first and providing supporting documents later”. We have also extended the application deadline to give owners more time to prepare their applications,” Gary said.
From conceptual framework to implementation, the EMSD has applied its professional expertise to successfully implement the LIMSS in collaboration with the URA. The scheme not only helps buildings in need to expedite modernisation of their aged lifts, but also raises public awareness of the importance of lift maintenance and safety. Gary believes that it is meaningful to be part of the professional team of the scheme to help enhance the safety of aged lifts.
While the URA has considerable experience in implementing subsidy schemes for the rehabilitation of old buildings, the EMSD has the expertise of lift works as well as a sound understanding of the lift industry. Therefore, the EMSD deployed a professional team to the URA to provide technical support for the LIMSS. The partnership aims to ensure that the scheme is people-oriented and fairly conducted, taking into consideration the capacity of the lift industry. Mr Cheung Ka-yu, Gary, an Electrical and Mechanical Engineer of the General Legislation Division, together with a Senior Electrical and Mechanical Engineer, has been seconded to the URA since August 2018 to help with the drawing up of the details of the LIMSS and its implementation. Gary said, “Initially, the scheme had only a framework. Our first and foremost task was to finalise the details, including the scope of subsidy, setting of priorities, application details, etc., with a view to receiving the first round of applications in the first quarter of 2019.” With the concerted efforts of the team, the first round of applications was launched as scheduled.
Two rounds of applications were arranged, with overwhelming responses. About 1200 applications involving about 5000 lifts were received in the first round, which was close to the original target of the LIMSS. “In the past, owners might hesitate to upgrade their lifts due to financial considerations and a lack of technical knowledge and organisational capacity when implementing lift modernisation works. The introduction of the LIMSS can help them expedite the progress of lift modernisation,” Gary said.
Apart from working out the details of the LIMSS, Gary also applied his professional knowledge about lifts to help the URA recruit a resident consultant and prepare standard tender documents for lift modernisation works to ensure that every project would meet the relevant technical and safety standards. “To ensure smooth implementation and one-stop support for participating building owners, we took into consideration multiple factors when working out the technical details of the tender documents, including maintenance arrangements upon completion of modernisation works,” Gary added. Technical issues aside, the team also had to take on the challenges of how to minimise the inconvenience inevitably caused to residents, especially the elderly, in buildings with only one lift or lifts serving alternate floors, when their lifts were out of service for several months. “After discussions and joint studies with the Development Bureau (DEVB) and the URA, it was decided that the LIMSS would provide support services in this aspect, including delivery of meals, purchasing daily necessities on residents’ behalf, and provision of mechanised stair climbing devices,” Gary said.
Challenges continued to emerge. The second round of applications was launched in January 2020 during the COVID-19 outbreak. In the light of the epidemic, many owners’ corporations were unable to hold general meetings to discuss if they should join the LIMSS. “We have to be prepared to resolve problems come what may. As building owners could not meet to pass resolutions about applying for the LIMSS, we have, after discussions with the DEVB and the URA, decided to streamline the application process and allow flexibility for building owners to join the scheme by “submitting application forms first and providing supporting documents later”. We have also extended the application deadline to give owners more time to prepare their applications,” Gary said.
From conceptual framework to implementation, the EMSD has applied its professional expertise to successfully implement the LIMSS in collaboration with the URA. The scheme not only helps buildings in need to expedite modernisation of their aged lifts, but also raises public awareness of the importance of lift maintenance and safety. Gary believes that it is meaningful to be part of the professional team of the scheme to help enhance the safety of aged lifts.
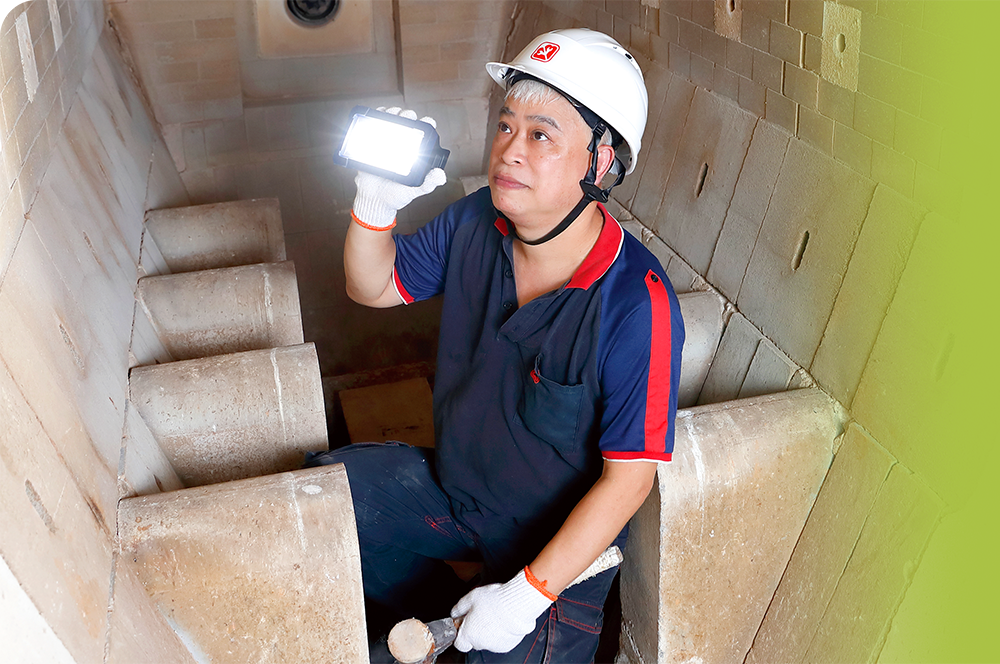
Perfecting the Art of Cremator Maintenance
Mr Fu King-wai, who has been handling brick-repairing work for cremators for almost 40 years, considers his duty to be a test of endurance. He has to repair cracked bricks and conduct condition checking of bricks inside the cremator with limited space.
Mr Fu King-wai has spent almost 40 years perfecting the art of cremator maintenance. Now a works supervisor I of our Municipal Sector Division, he has served at most government crematoria in Hong Kong since joining the EMSD in 1982. The Secretary for the Civil Service’s Commendation Award 2019 that he received last year was a well-earned recognition of his outstanding contribution.
“In the old days, the overseas cremator manufacturer would not release the design drawings to us. I had no choice but to stand at the cremator door and quietly observe how the manufacturer’s people laid the firebricks, making a pencil drawing as a guide,” Mr Fu explained. It took a full month for the manufacturer’s people to lay all five layers of firebricks against the cremator’s metal frame, which was as tall as a three-storey building. This month of careful observation and drawing sparked Mr Fu’s interest in firebricks and cremators, leading to a life-long vocation.
“Since a damaged brick may be buried between layers of ‘healthy’ bricks, it is important that we can correctly re-lay the ‘healthy’ bricks after replacing the damaged one, otherwise the whole structure may collapse,” he said. He is also a walking encyclopaedia of cremator systems and an expert in O&M and troubleshooting. Recognising the great potential of technology in improving cremator system monitoring and performance as well as occupational safety, his team has piloted many technological solutions and devices in recent years. This was on top of carrying out rigorous scheduled maintenance of cremators every two to six days, plus an annual overhaul that sees all parts dismantled, cleaned and repaired.
Now working at Kwai Chung Crematorium, Mr Fu never forgets that the team’s mission is to provide quality O&M service so that the deceased can complete their last journey with dignity and the family can receive the ashes promptly, on the day after cremation. Two years to retirement, Mr Fu looks forward to passing the baton to the younger generation, for whom he advises “patience and experience”.
“In the old days, the overseas cremator manufacturer would not release the design drawings to us. I had no choice but to stand at the cremator door and quietly observe how the manufacturer’s people laid the firebricks, making a pencil drawing as a guide,” Mr Fu explained. It took a full month for the manufacturer’s people to lay all five layers of firebricks against the cremator’s metal frame, which was as tall as a three-storey building. This month of careful observation and drawing sparked Mr Fu’s interest in firebricks and cremators, leading to a life-long vocation.
“Since a damaged brick may be buried between layers of ‘healthy’ bricks, it is important that we can correctly re-lay the ‘healthy’ bricks after replacing the damaged one, otherwise the whole structure may collapse,” he said. He is also a walking encyclopaedia of cremator systems and an expert in O&M and troubleshooting. Recognising the great potential of technology in improving cremator system monitoring and performance as well as occupational safety, his team has piloted many technological solutions and devices in recent years. This was on top of carrying out rigorous scheduled maintenance of cremators every two to six days, plus an annual overhaul that sees all parts dismantled, cleaned and repaired.
Now working at Kwai Chung Crematorium, Mr Fu never forgets that the team’s mission is to provide quality O&M service so that the deceased can complete their last journey with dignity and the family can receive the ashes promptly, on the day after cremation. Two years to retirement, Mr Fu looks forward to passing the baton to the younger generation, for whom he advises “patience and experience”.

Expediting Lift Modernisation Works Approval for Users’ Convenience
Mechanical inspector Mr Fung Siu-hang and his team helped expedite the approval of resumption permits for the only two lifts in a factory building in Chai Wan, making life much easier for its tenants.
Inspection, investigation, enforcement… regulatory tasks sound rigid, but the team at General Legislation Division (GLD) is accommodating. For example, when Hop Shi Factory Building in Chai Wan decided to simultaneously modernise the only two lifts serving the building, which caused unspeakable inconvenience to the tenants in the building, the GLD team pulled out all the stops to expedite the approval process for issuing a resumption permit. What would normally take more than 10 days was done within two days. Their work was shortlisted in EMSD’s 2019/20 “Good People, Good Deeds Commendation Scheme” campaign, and shows that regulators are empathetic.
Mechanical inspector Mr Fung Siu-hang was part of the team handling this case. He recalled that the EMSD issued a notice to the Owners’ Corporation of the building to advise adding an unintended car movement protector to its aged lifts that had been in use for many years and missing the safety installations compliant with the latest safety standards. The building however had both lifts out of service at the same time for the lift modernisation works. Its tenants were forced to put up makeshift planks on staircases to strenuously move goods up and down.
“The building’s management called us to ask for speeding up the approval process. We wondered why the urgency, so we made a site inspection, and found that the tenants were indeed in a dire situation. In the spirit of serving the public, we agreed to facilitate the approval process after they fulfilled all application requirements,” Siu-hang said.
As promised, the team dispatched two teams of inspectors to simultaneously monitor the testing of the two lifts by the contractors after receiving the building’s application. Enforcement standards were not compromised for speed, though. As the loading test was missing, the team asked the contractors to get it done that afternoon to make sure the lifts were safe even if overloaded.
“The whole process involved three groups of colleagues: inspectors monitored onsite testing, engineers verified test results and administrative colleagues prepared documents for the chief engineer to sign off on the resumption permit. We worked together flexibly to complete the entire process that night.” The helpful initiative has been commended, not only as a model case of “Good People, Good Deeds Commendation Scheme” but also by the factory building’s owner, who sent a note to the team to express gratitude.
Mechanical inspector Mr Fung Siu-hang was part of the team handling this case. He recalled that the EMSD issued a notice to the Owners’ Corporation of the building to advise adding an unintended car movement protector to its aged lifts that had been in use for many years and missing the safety installations compliant with the latest safety standards. The building however had both lifts out of service at the same time for the lift modernisation works. Its tenants were forced to put up makeshift planks on staircases to strenuously move goods up and down.
“The building’s management called us to ask for speeding up the approval process. We wondered why the urgency, so we made a site inspection, and found that the tenants were indeed in a dire situation. In the spirit of serving the public, we agreed to facilitate the approval process after they fulfilled all application requirements,” Siu-hang said.
As promised, the team dispatched two teams of inspectors to simultaneously monitor the testing of the two lifts by the contractors after receiving the building’s application. Enforcement standards were not compromised for speed, though. As the loading test was missing, the team asked the contractors to get it done that afternoon to make sure the lifts were safe even if overloaded.
“The whole process involved three groups of colleagues: inspectors monitored onsite testing, engineers verified test results and administrative colleagues prepared documents for the chief engineer to sign off on the resumption permit. We worked together flexibly to complete the entire process that night.” The helpful initiative has been commended, not only as a model case of “Good People, Good Deeds Commendation Scheme” but also by the factory building’s owner, who sent a note to the team to express gratitude.
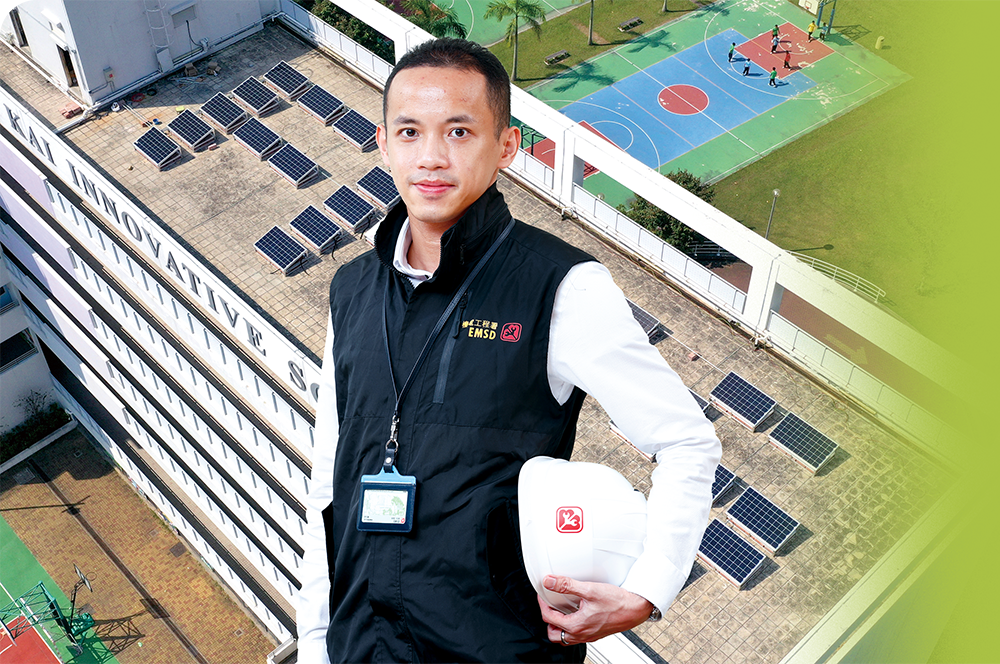
Connecting Future Generations with Renewable Energy
The Solar Harvest programme has taken Mr Lee Hang-mun, Edward, an engineer in our Energy Efficiency Office, to work with students and teachers at schools to build small-scale solar photovoltaic systems. He shares his experience in promoting renewable energy to our future generation.
Mr Lee Hang-mun, Edward, is keen to contribute to the field of environmental protection through his profession as an engineer. After a number of years in the private sector, Edward joined the Energy Efficiency Office of the EMSD in July 2019 as a Building Services Engineer. He is responsible for implementing the new Solar Harvest programme, which is designed to provide one-stop service and full subsidy to help eligible schools and welfare non-governmental organisations (welfare NGOs) install small-scale solar photovoltaic (PV) systems and join the Feed-in Tariff (FiT) Scheme offered by the two local power companies.
“Through Solar Harvest, we promote renewable energy (RE) to schools and welfare NGOs from different perspectives, thereby obtaining multiple environmental achievements, including the enhancement of environmental awareness among students, young people and people from different sectors,” Edward said.
After joining the EMSD, Edward first implemented the programme for the first batch of shortlisted schools including Fung Kai Innovative School in Sheung Shui. To explore the school’s expectations for the programme, Edward and the designer paid a visit to the school to meet with the principal and teachers-in-charge. In addition, Edward’s team added sensors to the school’s solar PV system to collect data on solar power generation for the development of teaching materials on renewable energy. Through this programme, students were able to track the data and experience first-hand the benefits of renewable energy, adding more fun to learning. Edward’s team also interacted with students, encouraging them to unleash their creativity by designing patterns for the placement of solar PV panels. Other than alphabets, many interesting designs were also presented. A number of schools adopted the students’ designs, thus enhancing their sense of engagement with the programme.
Well-received by schools and welfare NGOs, the five-year Solar Harvest programme received more than 210 applications in its first year of implementation. Last year, Edward’s team assisted 50 schools and welfare NGOs to install solar PV systems. Participating schools and welfare NGOs also received payments from the FiT Scheme. In order to benefit even more schools and welfare NGOs, Edward’s team will be expanded to complete more installation works in 2020/21.
“We hope to benefit more schools and welfare NGOs with our Solar Harvest programme as quickly as possible. We will also showcase successful cases, such as Fung Kai Innovative School, in order to promote the programme to schools through their sponsoring bodies. With more schools taking part in the programme, more students will be able to learn about RE and the importance of energy efficiency with first-hand experience. I am most motivated to combat climate change by cultivating and harvesting electricity together with the participating schools and welfare NGOs,” Edward said.
“Through Solar Harvest, we promote renewable energy (RE) to schools and welfare NGOs from different perspectives, thereby obtaining multiple environmental achievements, including the enhancement of environmental awareness among students, young people and people from different sectors,” Edward said.
After joining the EMSD, Edward first implemented the programme for the first batch of shortlisted schools including Fung Kai Innovative School in Sheung Shui. To explore the school’s expectations for the programme, Edward and the designer paid a visit to the school to meet with the principal and teachers-in-charge. In addition, Edward’s team added sensors to the school’s solar PV system to collect data on solar power generation for the development of teaching materials on renewable energy. Through this programme, students were able to track the data and experience first-hand the benefits of renewable energy, adding more fun to learning. Edward’s team also interacted with students, encouraging them to unleash their creativity by designing patterns for the placement of solar PV panels. Other than alphabets, many interesting designs were also presented. A number of schools adopted the students’ designs, thus enhancing their sense of engagement with the programme.
Well-received by schools and welfare NGOs, the five-year Solar Harvest programme received more than 210 applications in its first year of implementation. Last year, Edward’s team assisted 50 schools and welfare NGOs to install solar PV systems. Participating schools and welfare NGOs also received payments from the FiT Scheme. In order to benefit even more schools and welfare NGOs, Edward’s team will be expanded to complete more installation works in 2020/21.
“We hope to benefit more schools and welfare NGOs with our Solar Harvest programme as quickly as possible. We will also showcase successful cases, such as Fung Kai Innovative School, in order to promote the programme to schools through their sponsoring bodies. With more schools taking part in the programme, more students will be able to learn about RE and the importance of energy efficiency with first-hand experience. I am most motivated to combat climate change by cultivating and harvesting electricity together with the participating schools and welfare NGOs,” Edward said.
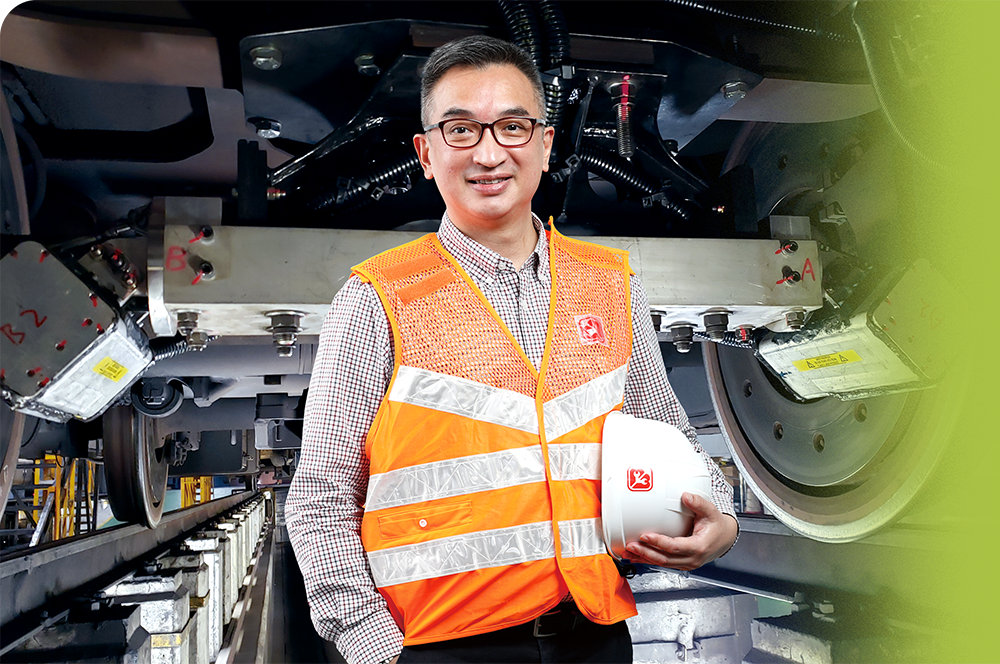
Staying Calm to Co-ordinate Major Railway Incident Investigation
Major incident investigations are never easy, as onsite situations are unpredictable and the evidences must be gathered promptly. Railways Branch Senior Engineer Mr Li Yick-fai, Ernest, recalls how he co-ordinates the investigation into the MTR Hung Hom Station derailment incident.
On 17 September 2019, at the time when Mr Li Yick-fai, Ernest, Senior Engineer of the Railways Branch (RB), returned to the EMSD Headquarters for work, he received a call about a serious incident, in which an East Rail Line (EAL) train had derailed while entering Hung Hom Station. He ran into the office to gather colleagues and rushed to the scene with about ten people. Ernest is a veteran in handling electrical and gas incidents as he has served in various posts in the EMSD. Although he was nervous, Ernest could still remain calm in the face of this serious incident, the firstever derailment of an EAL train carrying passengers.
The site of the incident was extensive, making the investigation and evidence collection even more complicated and difficult. “First, we had to gauge the situation of the scene to ascertain how serious the incident was, and whether there were casualties. Then we had to determine how services were affected and what might have caused the incident. We did a quick tabulation of parts and equipment on site, and the degree of damage to the tracks, and then checked if any CCTV systems near the Station had captured footage of the incident. Additionally, we had to gather relevant information for the Secretary for Transport and Housing and our Director to make responses to media enquiries, as well as co-ordinating with the MTR Corporation Limited (MTRCL) on their repair plans and work flow,” Ernest recalled.
While the RB team was conducting on-site evidence collection, the MTRCL carried out repairs. Train services at Hung Hom Station partially resumed by 6 a.m. the next morning. Repairs continued for several nights after EAL services had finished for the day. Throughout this period, Ernest and his colleagues took turns to monitor the repairs and testing of key components including track gauge, welded joints, sleepers, and point machines at turnouts. A test run with an empty train was also carried out to confirm the safe and smooth operation of the service. The team approved a full resumption of services by the MTRCL through the affected rail section only after all the test data was satisfactory.
After the incident, the RB sought assistance from overseas experts experienced in investigating major railway incidents. Subsequently, the “Technical Investigation Report on Train Derailment Incident at Hung Hom Station on MTR East Rail Line” was released in March 2020, which recommended a number of improvement measures for the MTRCL to implement, so as to ensure that similar incidents would not happen again.
Ernest said, “As a regulator, the EMSD focuses on using our expertise to protect public safety. Upon completion of the report, we kept monitoring the MTRCL’s implementation of the recommended remedial measures. Since this serious incident, the RB has stepped up its regulatory work to ensure railway safety and to regain public confidence in our railway systems.”
The site of the incident was extensive, making the investigation and evidence collection even more complicated and difficult. “First, we had to gauge the situation of the scene to ascertain how serious the incident was, and whether there were casualties. Then we had to determine how services were affected and what might have caused the incident. We did a quick tabulation of parts and equipment on site, and the degree of damage to the tracks, and then checked if any CCTV systems near the Station had captured footage of the incident. Additionally, we had to gather relevant information for the Secretary for Transport and Housing and our Director to make responses to media enquiries, as well as co-ordinating with the MTR Corporation Limited (MTRCL) on their repair plans and work flow,” Ernest recalled.
While the RB team was conducting on-site evidence collection, the MTRCL carried out repairs. Train services at Hung Hom Station partially resumed by 6 a.m. the next morning. Repairs continued for several nights after EAL services had finished for the day. Throughout this period, Ernest and his colleagues took turns to monitor the repairs and testing of key components including track gauge, welded joints, sleepers, and point machines at turnouts. A test run with an empty train was also carried out to confirm the safe and smooth operation of the service. The team approved a full resumption of services by the MTRCL through the affected rail section only after all the test data was satisfactory.
After the incident, the RB sought assistance from overseas experts experienced in investigating major railway incidents. Subsequently, the “Technical Investigation Report on Train Derailment Incident at Hung Hom Station on MTR East Rail Line” was released in March 2020, which recommended a number of improvement measures for the MTRCL to implement, so as to ensure that similar incidents would not happen again.
Ernest said, “As a regulator, the EMSD focuses on using our expertise to protect public safety. Upon completion of the report, we kept monitoring the MTRCL’s implementation of the recommended remedial measures. Since this serious incident, the RB has stepped up its regulatory work to ensure railway safety and to regain public confidence in our railway systems.”
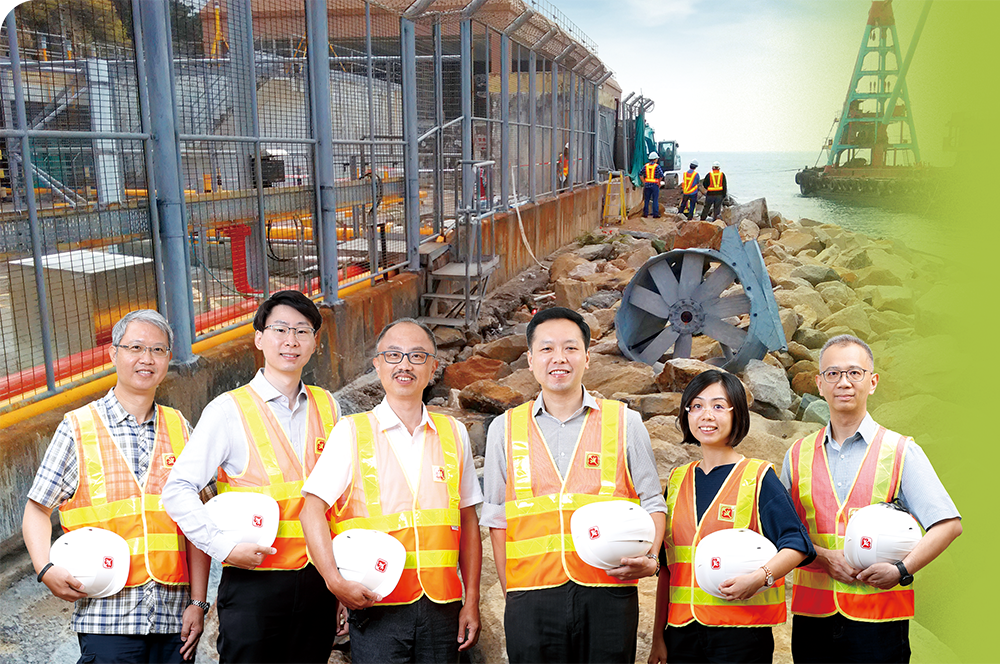
Learn from the Experience and be Well-prepared to Enhance the Safety of Near-shore Gas Storage Facilities
This team from our Gas Standards Office co-ordinated an inter-departmental group to expedite the recovery of a seawall near an LPG storage facility in Ap Lei Chau, severely damaged by super typhoon Manghkut. The works also improved safety for the community. Ms Laura Ngai and Mr Anthony Leung share the story.
During the passage of super typhoon Mangkhut on 16 September 2018, the seawall at Lee Nam Road, Ap Lei Chau, was battered by huge waves and high winds, resulting in unprecedented damage to an LPG storage facility nearby. Settlement occurred at part of the facility and a peripheral structure had to be demolished due to serious structural damage. While assessment results suggested that the damage did not pose gas safety hazards nor affect gas supply, the facility owner should repair and reinforce the facility before the next typhoon season arrives. In view of this, the Gas Standards Office (GasSO) of the EMSD took the lead to form an interdepartmental working group with the Buildings Department, the Civil Engineering and Development Department, the Drainage Services Department and the Lands Department to render assistance to the facility owner. Members of the working group met on a bi-weekly basis to co-ordinate relevant tasks and expedite the monitoring and approval of repair works. GasSO engineers Ms Ngai Nga-man, Laura, and Mr Leung Kwan-kit, Anthony, spearheaded the tasks.
“As Hong Kong’s Gas Authority, the EMSD attaches great importance to maintaining gas safety. Thus, we took the initiative to co-ordinate the inter-departmental working group and communicate closely with other departments. Thanks to their unfailing support, the assistance of our experienced colleagues and supervisors, the on-site supervision of our inspectors as well as the efforts of the facility owner, the complicated approval processes and repair works were completed swiftly within just six months,” Laura said.
During the works period, Laura, Anthony and the GasSO team closely liaised with the facility owner to explore the most practicable reinforcement solutions, such as introducing settlement measuring devices to monitor the settlement risk of the LPG pipes and storage tanks near the collapsed grounds, reinforcing and moving inland a gas supply main of 200 mm diameter, installing wire meshes with high durability and aluminium panels to a sea-facing water boiler room to shield it from strong winds and debris, etc. The team also reminded the facility owner to maintain sufficient spare parts for timely replacement in the future.
“Thanks to the collaborative efforts of our team, the LPG supply to about 8000 households in the neighbourhood was unaffected throughout the works period. The facility is now sturdier to withstand future typhoons. Learning from this experience, we immediately conducted a comprehensive risk assessment of all LPG storage facilities in Hong Kong and urged owners of near-shore gas storage facilities to make reference to the reinforcement works of the facility at Ap Lei Chau, including the provision of similar protective measures to their sea-facing installations, trimming of tree branches before the typhoon season to prevent damage of facilities due to fallen trees, etc.,” Anthony said.
Collaboration between the GasSO team and the Ap Lei Chau facility owner kept the LPG storage facility safe and ensured that all repair and reinforcement works were completed before the typhoon season in July 2019. At the same time, owners of other near-shore facilities drew reference from the works of the Ap Lei Chau facility and adopted precautions against heavy wind. Together, we will ride out the storms ahead.
“As Hong Kong’s Gas Authority, the EMSD attaches great importance to maintaining gas safety. Thus, we took the initiative to co-ordinate the inter-departmental working group and communicate closely with other departments. Thanks to their unfailing support, the assistance of our experienced colleagues and supervisors, the on-site supervision of our inspectors as well as the efforts of the facility owner, the complicated approval processes and repair works were completed swiftly within just six months,” Laura said.
During the works period, Laura, Anthony and the GasSO team closely liaised with the facility owner to explore the most practicable reinforcement solutions, such as introducing settlement measuring devices to monitor the settlement risk of the LPG pipes and storage tanks near the collapsed grounds, reinforcing and moving inland a gas supply main of 200 mm diameter, installing wire meshes with high durability and aluminium panels to a sea-facing water boiler room to shield it from strong winds and debris, etc. The team also reminded the facility owner to maintain sufficient spare parts for timely replacement in the future.
“Thanks to the collaborative efforts of our team, the LPG supply to about 8000 households in the neighbourhood was unaffected throughout the works period. The facility is now sturdier to withstand future typhoons. Learning from this experience, we immediately conducted a comprehensive risk assessment of all LPG storage facilities in Hong Kong and urged owners of near-shore gas storage facilities to make reference to the reinforcement works of the facility at Ap Lei Chau, including the provision of similar protective measures to their sea-facing installations, trimming of tree branches before the typhoon season to prevent damage of facilities due to fallen trees, etc.,” Anthony said.
Collaboration between the GasSO team and the Ap Lei Chau facility owner kept the LPG storage facility safe and ensured that all repair and reinforcement works were completed before the typhoon season in July 2019. At the same time, owners of other near-shore facilities drew reference from the works of the Ap Lei Chau facility and adopted precautions against heavy wind. Together, we will ride out the storms ahead.
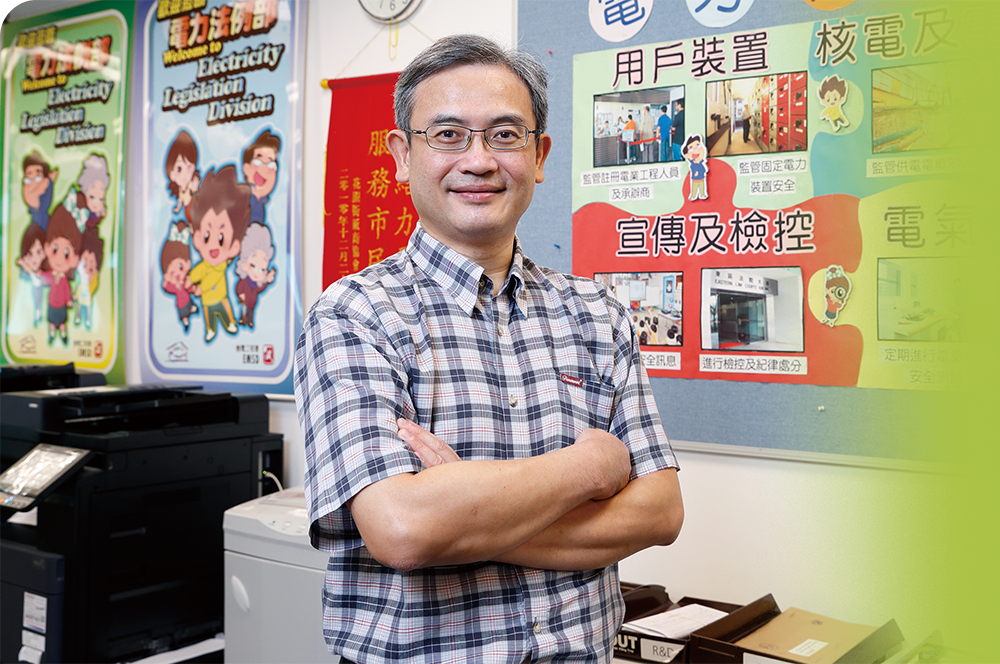
Promoting Electrical Safety with the EMSD for Four Decades
Mr Pang Nai-tai has served more than 22 years at the Electricity Legislation Division and worked in all of its sub-divisions. He shares his experiences from his almost 40-year long career at the EMSD, most of which was devoted to promoting electrical safety.
Mr Pang Nai-tai began his career with the EMSD as an apprentice and rose through the ranks to become a Senior Electrical Inspector before his retirement in July 2020. Throughout his service of nearly 40 years with the EMSD, he served more than 22 years at the Electricity Legislation Division (ELD) and worked in each of its four subdivisions, undertaking nearly all of its functions, including inspection, monitoring, investigation, evidence gathering, publicity, prosecution, etc., thereby contributing to the electrical safety of Hong Kong.
From 1997 to 2006, Mr Pang was posted to the Electrical Products Sub-division, where he participated in shop inspections, with the aim of monitoring and promoting electrical product safety, so as to ensure compliance with the Electrical Products (Safety) Regulation. He also took part in investigation and evidence gathering for electrical incidents. Among the handled cases, one was a fatal electrocution incident involving an air-conditioning technician who was dismantling an air-conditioner. During investigation, he discovered that the cable of the appliance was compressed during installation and subsequently damaged during removal. As the cable was still energised during the process, the metal frame of the air-conditioner was live, resulting in the fatal accident. Mr Pang also found that the building’s responsible persons failed to correctly label the switches. He promptly reminded the responsible contractor to carry out regular inspections in strict accordance with the relevant ordinance to prevent similar incidents in future.
His next stint was with the Publicity and Prosecution Sub-division from 2006 to 2010. Apart from handling prosecution cases based on the evidence collected by other sub-divisions, he was also involved in a range of promotional activities, with a view to enhancing public awareness of electrical safety by means of non-law enforcement work.
After posting outside of the ELD between 2010 and 2012, Mr Pang, having been promoted, returned to the Nuclear and Utility Safety Sub-division of the ELD in 2012. One of the key responsibilities of Mr Pang was to inspect construction sites to prevent workers from damaging underground cables during their works. He was also responsible for reminding the trade and workers through various channels such as seminars to adopt safety measures to protect both the cables and the workers. Besides, this Sub-division was also responsible for ensuring that the electromagnetic field of the power companies’ pylons were in compliance with the World Health Organization’s regulations. As a member of the inter-departmental emergency response team for the Daya Bay Nuclear Power Station, this Sub-division participated in the regular meetings and drills to maintain effective teamwork and agility to deal with incidents. Mr Pang was thankful that the emergency response team did not need to be activated during this time.
In mid-2019, Mr Pang was transferred to the Consumer Installations Sub-division, where he took up the duties of monitoring annual inspections of fixed electrical installations and the registration of generating facilities to tie in with the implementation of the Feed-in Tariff Scheme, which motivated members of the public to install renewable energy generating facilities. Mr Pang was also involved in facilitating the understanding of and compliance with the relevant electrical safety requirements by generating facility owners and the trade while contributing to sustainability.
Devoted most of his career to promoting electrical safety, Mr Pang was delighted to observe a continuing reduction in electrical incidents in the territory before his retirement.
From 1997 to 2006, Mr Pang was posted to the Electrical Products Sub-division, where he participated in shop inspections, with the aim of monitoring and promoting electrical product safety, so as to ensure compliance with the Electrical Products (Safety) Regulation. He also took part in investigation and evidence gathering for electrical incidents. Among the handled cases, one was a fatal electrocution incident involving an air-conditioning technician who was dismantling an air-conditioner. During investigation, he discovered that the cable of the appliance was compressed during installation and subsequently damaged during removal. As the cable was still energised during the process, the metal frame of the air-conditioner was live, resulting in the fatal accident. Mr Pang also found that the building’s responsible persons failed to correctly label the switches. He promptly reminded the responsible contractor to carry out regular inspections in strict accordance with the relevant ordinance to prevent similar incidents in future.
His next stint was with the Publicity and Prosecution Sub-division from 2006 to 2010. Apart from handling prosecution cases based on the evidence collected by other sub-divisions, he was also involved in a range of promotional activities, with a view to enhancing public awareness of electrical safety by means of non-law enforcement work.
After posting outside of the ELD between 2010 and 2012, Mr Pang, having been promoted, returned to the Nuclear and Utility Safety Sub-division of the ELD in 2012. One of the key responsibilities of Mr Pang was to inspect construction sites to prevent workers from damaging underground cables during their works. He was also responsible for reminding the trade and workers through various channels such as seminars to adopt safety measures to protect both the cables and the workers. Besides, this Sub-division was also responsible for ensuring that the electromagnetic field of the power companies’ pylons were in compliance with the World Health Organization’s regulations. As a member of the inter-departmental emergency response team for the Daya Bay Nuclear Power Station, this Sub-division participated in the regular meetings and drills to maintain effective teamwork and agility to deal with incidents. Mr Pang was thankful that the emergency response team did not need to be activated during this time.
In mid-2019, Mr Pang was transferred to the Consumer Installations Sub-division, where he took up the duties of monitoring annual inspections of fixed electrical installations and the registration of generating facilities to tie in with the implementation of the Feed-in Tariff Scheme, which motivated members of the public to install renewable energy generating facilities. Mr Pang was also involved in facilitating the understanding of and compliance with the relevant electrical safety requirements by generating facility owners and the trade while contributing to sustainability.
Devoted most of his career to promoting electrical safety, Mr Pang was delighted to observe a continuing reduction in electrical incidents in the territory before his retirement.

Regional Digital Control Centre: Vision Comes to Life
Mr So Pok-man, Patrick, and his team are responsible for the design and implementation of the EMSD’s first Regional Digital Control Centre with an aim to achieve E&M digitisation and lay the foundation for building a smart city.
Standing in front of the huge light-emitting diode dashboard in the EMSD’s first Regional Digital Control Centre (RDCC) is like being in a sci-fi movie. Graphical visualisations of operational data, tracking everything from the energy efficiency performance of air-conditioning systems to the status of lifts and escalators, can be called up and analysed to enable rapid troubleshooting, more effective predictive maintenance and even real-time facility management.
Overseeing the implementation of this pilot RDCC is Mr So Pok-man, Patrick, an engineer of the General Engineering Services Division (GESD). This RDCC will eventually be connected to 400 major government buildings maintained by the GESD, each with annual electricity consumption of over 500000 kWh, to monitor and optimise their E&M systems’ energy efficiency and operational performance.
“RDCC is one of the initiatives under the second EMSTF Five-year Strategic Plan,” Mr So noted. In 2018, he and his team were tasked with turning the RDCC vision into reality. As the concept was new and no off-the-shelf solution was available, the team partnered with a start-up to work on design and implementation. The RDCC began operations in February 2020.
“In the long run, RDCC is the way forward for the management of smart buildings,” Mr So said. The EMSTF also has the unique advantage of having access to a rich database of government building E&M facilities, especially from newer buildings that have deployed integrated Building Management Systems in the past five to seven years. Once integrated with machine learning and artificial intelligence, the database will generate useful digital tools to help make buildings smarter and greener. Both the hardware and software have been designed to run on an open platform so that all future EMSD RDCCs can communicate with each other.
Overseeing the implementation of this pilot RDCC is Mr So Pok-man, Patrick, an engineer of the General Engineering Services Division (GESD). This RDCC will eventually be connected to 400 major government buildings maintained by the GESD, each with annual electricity consumption of over 500000 kWh, to monitor and optimise their E&M systems’ energy efficiency and operational performance.
“RDCC is one of the initiatives under the second EMSTF Five-year Strategic Plan,” Mr So noted. In 2018, he and his team were tasked with turning the RDCC vision into reality. As the concept was new and no off-the-shelf solution was available, the team partnered with a start-up to work on design and implementation. The RDCC began operations in February 2020.
“In the long run, RDCC is the way forward for the management of smart buildings,” Mr So said. The EMSTF also has the unique advantage of having access to a rich database of government building E&M facilities, especially from newer buildings that have deployed integrated Building Management Systems in the past five to seven years. Once integrated with machine learning and artificial intelligence, the database will generate useful digital tools to help make buildings smarter and greener. Both the hardware and software have been designed to run on an open platform so that all future EMSD RDCCs can communicate with each other.

Racing Against Time to Convert Chun Yeung Estate
Mr Tang Choi-chin participated in the on-site preparation works, such as Towngas water heater installation, at the Chun Yeung Estate quarantine centre. With the experience of fighting against SARS in 2003, he is proficient in taking part in the anti-epidemic preparation works this time.
On Chinese New Year’s Eve in January 2020, Mr Tang Choi-chin, a chief technical officer of our Health Sector Division, received a call from his senior asking him to quickly assemble a team to get ready to convert a new but unoccupied housing estate into a COVID-19 quarantine centre as requested by the DH. Mr Tang, with experience in building negative pressure wards during the SARS outbreak in 2003, mobilised a team overnight and took immediate action. Unfortunately, a number of facilities in the housing estate were promptly vandalised. Hence, the newly converted quarantine units could not be put into operation.
Chun Yeung Estate in Fo Tan, another new housing estate, was soon identified for conversion. Mr Tang needed to mobilise an inter-divisional team to commence the work there at full steam on 9 February 2020. “The EMSTF’s role was to install more than 16000 light bulbs in around 3200 units, and to install and test around 3200 gas water heaters, one in each unit by phases,” he said.
Time was tight, and first-phase installation had to be completed by 19 February 2020 when the first batch of Hong Kong residents on board the Diamond Princess cruise ship, was expected to return to Hong Kong on a Government-chartered flight for their 14-day quarantine at the Estate. “It turned out that testing the gas water heaters was the biggest challenge,” Mr Tang recalled. “Though Towngas had provided manpower to help install the water heaters, it was necessary for the EMSTF team to conduct the testing, which was time consuming.”
According to Mr Tang, the Government’s inter-departmental drill exercise code-named Jadeite in 2012 to test contingency actions in the event of a virus outbreak, proved highly valuable in 2020. “Thanks to the drill I participated eight years ago, I was able to equip team members this time with the necessary knowledge and resolve infection control concerns that some had,” he said.
The conversion at Chun Yeung Estate was completed on time. “Our colleagues’ team spirit of mutual trust and seamless collaboration in this cross-divisional mission was most impressive. Exercise Jadeite also proves the value of training and the importance of passing on experience,” Mr Tang concluded.
Chun Yeung Estate in Fo Tan, another new housing estate, was soon identified for conversion. Mr Tang needed to mobilise an inter-divisional team to commence the work there at full steam on 9 February 2020. “The EMSTF’s role was to install more than 16000 light bulbs in around 3200 units, and to install and test around 3200 gas water heaters, one in each unit by phases,” he said.
Time was tight, and first-phase installation had to be completed by 19 February 2020 when the first batch of Hong Kong residents on board the Diamond Princess cruise ship, was expected to return to Hong Kong on a Government-chartered flight for their 14-day quarantine at the Estate. “It turned out that testing the gas water heaters was the biggest challenge,” Mr Tang recalled. “Though Towngas had provided manpower to help install the water heaters, it was necessary for the EMSTF team to conduct the testing, which was time consuming.”
According to Mr Tang, the Government’s inter-departmental drill exercise code-named Jadeite in 2012 to test contingency actions in the event of a virus outbreak, proved highly valuable in 2020. “Thanks to the drill I participated eight years ago, I was able to equip team members this time with the necessary knowledge and resolve infection control concerns that some had,” he said.
The conversion at Chun Yeung Estate was completed on time. “Our colleagues’ team spirit of mutual trust and seamless collaboration in this cross-divisional mission was most impressive. Exercise Jadeite also proves the value of training and the importance of passing on experience,” Mr Tang concluded.
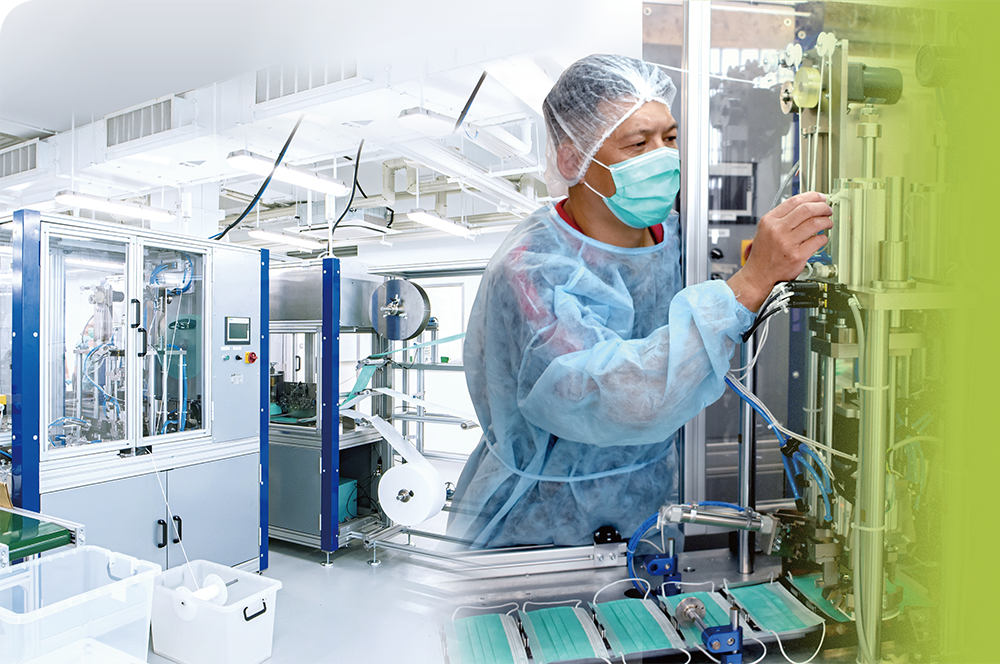
Close Encounters with Face Mask Machines
Mr Wu Tai-suen and his team support the maintenance work of mechanical facilities at Lo Wu Correctional Institution. They have overcome all technical obstacles and equipped themselves with skills of assembly, testing and commissioning of mask-making machines in a short time to ensure reliability and high productivity of the machines.
Demand for surgical masks suddenly shot up after the COVID-19 outbreak in January 2020. In early February 2020, Mr Wu Tai-suen, a works supervisor II at the Security and Vehicle Services Division, who heads up the resident team responsible for mechanical systems maintenance at Lo Wu Correctional Institution, was tasked with installing and calibrating several new mask-making machines from the Mainland to cope with increasing demand.
“Installing and calibrating mask-making machines was new to us” said Mr Wu. “The machines were of different types and origins, with no operating manuals. What’s more, the technical person who was supposed to come to Hong Kong to set the machines up had his trip postponed due to the Mainland lockdown.” What followed was a few months of challenging work and a steep learning curve, drawing on the team’s mechanical experience, online research and advice from local trade partners and manufacturers familiar with mask machines.
“The biggest challenge was calibrating the earloop machines,” he explained. Each mask-making machine comes with two earloop machines, each churning out 40 earloops per minute. The earloops must be of the right tensile strength so the mask can cover the face snugly, and calibration of the machine is important to make sure the earloops are not too tight or too loose. As the mask and earloop machines must operate 24x7 at high speed to satisfy demand, this heavy use meant they had to be calibrated often and their parts replaced frequently. “We soon realised that though the machines are not involved with high tech, the mask-making steps are complex and the specification requirements are actually very high,” he recalled. “Luckily, we got the hang of it after a while and managed to find locally all the spare parts we need.”
Mr Wu’s team had to work round the clock in shifts in those months to keep the machines running, which was on top of normal maintenance duties for the CSD. Any insight from the experience? “What looks simple, may not be simple at all. There is always something new to learn,” Mr Wu concluded.
“Installing and calibrating mask-making machines was new to us” said Mr Wu. “The machines were of different types and origins, with no operating manuals. What’s more, the technical person who was supposed to come to Hong Kong to set the machines up had his trip postponed due to the Mainland lockdown.” What followed was a few months of challenging work and a steep learning curve, drawing on the team’s mechanical experience, online research and advice from local trade partners and manufacturers familiar with mask machines.
“The biggest challenge was calibrating the earloop machines,” he explained. Each mask-making machine comes with two earloop machines, each churning out 40 earloops per minute. The earloops must be of the right tensile strength so the mask can cover the face snugly, and calibration of the machine is important to make sure the earloops are not too tight or too loose. As the mask and earloop machines must operate 24x7 at high speed to satisfy demand, this heavy use meant they had to be calibrated often and their parts replaced frequently. “We soon realised that though the machines are not involved with high tech, the mask-making steps are complex and the specification requirements are actually very high,” he recalled. “Luckily, we got the hang of it after a while and managed to find locally all the spare parts we need.”
Mr Wu’s team had to work round the clock in shifts in those months to keep the machines running, which was on top of normal maintenance duties for the CSD. Any insight from the experience? “What looks simple, may not be simple at all. There is always something new to learn,” Mr Wu concluded.
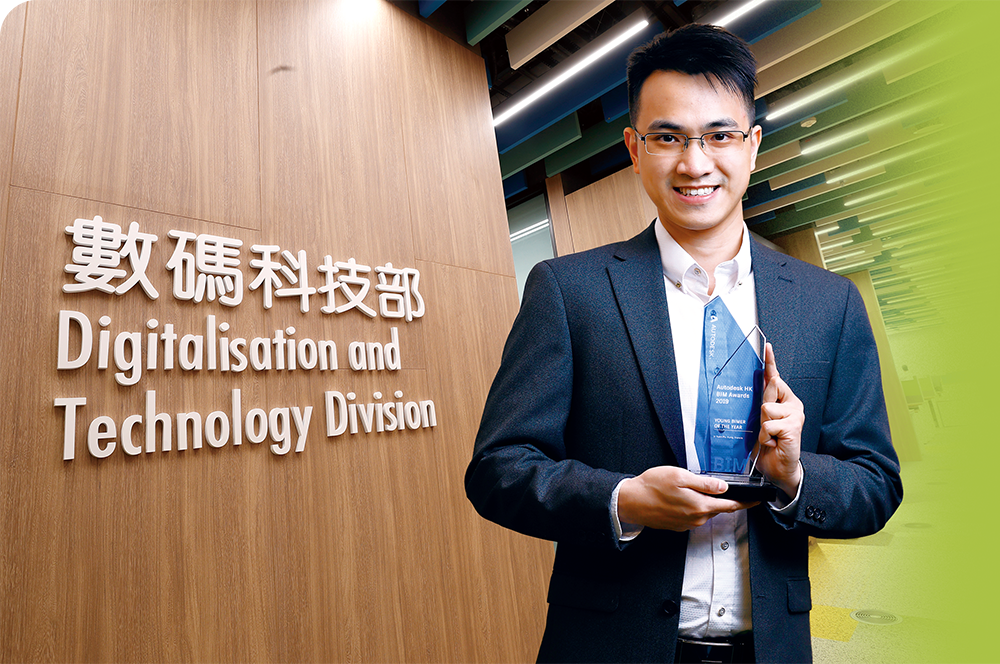
Hong Kong Young Public Officers to Work at the United Nations as Chinese Personnel
Mr Yuen Piu-hung, Francis, an engineer who has been involved in the development of BIM-AM projects since 2014, was awarded the “Young BIMer of the Year” in 2019, a recognition of his contribution in the development of BIM-AM in the trade.
It all began in December 2018, when Mr Yuen Piu-hung, Francis, an engineer of the Digitalisation and Technology Division, received an email notice from the Civil Service Bureau via his head of grade. It was a call from the Government for young public officers to take part in the United Nations (UN) Junior Professional Officer (JPO) Programme. Successful candidates would be posted to UN agencies in the US or Europe to work as JPOs for two years as Chinese personnel. After talking to his wife, who was very supportive, Mr Yuen put in his application.
“Competition was keen,” he said. After going through a series of interviews in Hong Kong, shortlisted candidates were invited to Beijing in July 2019 for a one-week training on China’s national policies, foreign affairs and governance strategies. Candidates’ performance in the training formed part of the assessment.
Mr Yuen and another EMSD engineer were two of five young public officers from the Government eventually recommended by the Ministry of Foreign Affairs of the People's Republic of China to participate in the UN’s JPO Programme. Mr Yuen will be working in the UN office in Geneva for two years. “I am really looking forward to this unique opportunity to gain more experience in a multi-cultural environment with diverse perspectives and considerations,” he said.
“Competition was keen,” he said. After going through a series of interviews in Hong Kong, shortlisted candidates were invited to Beijing in July 2019 for a one-week training on China’s national policies, foreign affairs and governance strategies. Candidates’ performance in the training formed part of the assessment.
Mr Yuen and another EMSD engineer were two of five young public officers from the Government eventually recommended by the Ministry of Foreign Affairs of the People's Republic of China to participate in the UN’s JPO Programme. Mr Yuen will be working in the UN office in Geneva for two years. “I am really looking forward to this unique opportunity to gain more experience in a multi-cultural environment with diverse perspectives and considerations,” he said.

Making the most of the “Golden Two Hours” in Railway Maintenance to Ensure Passenger Safety
As the city sleeps, Railways Branch Engineer Ms Chan Ching-man, Kitty, is often working in the early hours of the morning to monitor MTR railway maintenance works. She explains the importance of the 2 a.m. to 4 a.m. "golden two-hour" window in ensuring railway safety.
Trained as an electrical engineer, Ms Chan Ching-man, Kitty, did not expect to be on call round the clock since she first joined the EMSD’s Railways Branch in October 2018. Since railway maintenance has to be completed within the “golden two-hour” window between 2 a.m. and 4 a.m., i.e. the short period of time during which MTR train services have ended and are yet to resume, Kitty has to be on site during this period, whenever there are maintenance works for the railway system, to ensure that the works are conducted in accordance with the relevant guidelines and procedures.
Kitty’s team is responsible for the matters relating to the East Rail Line (EAL) and its extension from Hung Hom to Admiralty. While the works on the new section can be done during the day, all works involving the operating section have to be conducted within the two-hour window at night. “Even seemingly minor railway incidents involve extensive maintenance and monitoring works. Due to the EAL’s relatively long history and open-air rails, it is prone to having emergency incidents such as cracks on rails, which requires us to be present to monitor the repair process late at night when the train services have ended,” Kitty said.
In addition to the routine railway safety inspections and the hectic regulatory work in preparing the new section of the EAL for commissioning, Kitty’s team has to conduct vetting and on-site testing in relation to the replacement of the signalling system of the EAL, as well as handle other railway-related emergency incidents. As a result, Kitty has to work at night five to six times a month on average. She once even worked at night three times in a week, travelling to distant areas such as Sheung Shui and Fanling. At first, her family was worried about her safety for having to leave home alone at night. Taxi drivers are often perplexed by why she has to travel by herself from urban Kowloon to a remote railway station that is already closed. However, Kitty has now gotten used to this work arrangement. Interestingly, her son, now in primary school, loves to listen to stories about her overnight “adventures” at work.
In order to meet operational needs, Kitty never switches off her mobile phone and is always ready for her job. “The emergency calls from the MTR Operations Control Centre always put me under pressure. While the pressure for frontline maintenance personnel stems from the tight timeframe and the challenging working environment, our pressure arises from our official duties as the regulator. We have to carefully monitor the entire repair process, so as to ensure railway safety. Only when the railway services resume normal and passengers are able to travel smoothly, will I truly have peace of mind,” Kitty said.
Kitty’s team is responsible for the matters relating to the East Rail Line (EAL) and its extension from Hung Hom to Admiralty. While the works on the new section can be done during the day, all works involving the operating section have to be conducted within the two-hour window at night. “Even seemingly minor railway incidents involve extensive maintenance and monitoring works. Due to the EAL’s relatively long history and open-air rails, it is prone to having emergency incidents such as cracks on rails, which requires us to be present to monitor the repair process late at night when the train services have ended,” Kitty said.
In addition to the routine railway safety inspections and the hectic regulatory work in preparing the new section of the EAL for commissioning, Kitty’s team has to conduct vetting and on-site testing in relation to the replacement of the signalling system of the EAL, as well as handle other railway-related emergency incidents. As a result, Kitty has to work at night five to six times a month on average. She once even worked at night three times in a week, travelling to distant areas such as Sheung Shui and Fanling. At first, her family was worried about her safety for having to leave home alone at night. Taxi drivers are often perplexed by why she has to travel by herself from urban Kowloon to a remote railway station that is already closed. However, Kitty has now gotten used to this work arrangement. Interestingly, her son, now in primary school, loves to listen to stories about her overnight “adventures” at work.
In order to meet operational needs, Kitty never switches off her mobile phone and is always ready for her job. “The emergency calls from the MTR Operations Control Centre always put me under pressure. While the pressure for frontline maintenance personnel stems from the tight timeframe and the challenging working environment, our pressure arises from our official duties as the regulator. We have to carefully monitor the entire repair process, so as to ensure railway safety. Only when the railway services resume normal and passengers are able to travel smoothly, will I truly have peace of mind,” Kitty said.
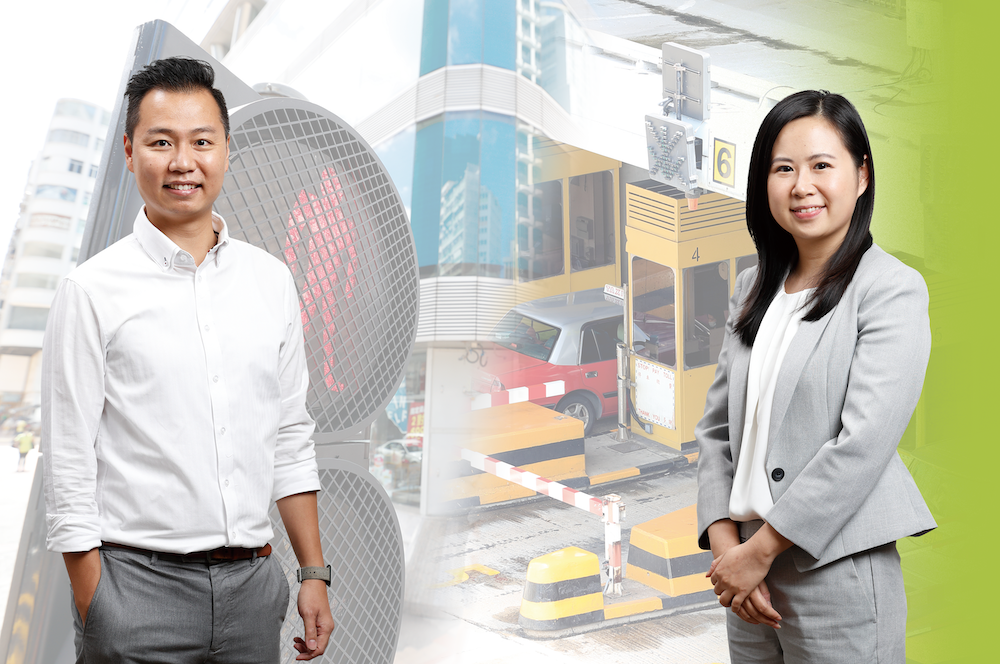
Restoring Normality to Traffic Lights and Cross-Harbour Tunnel
The series of public order events taken place in the second half of 2019 in Hong Kong resulted in extensive damage to a large number of public facilities. Ms Chan Ying-ying, Dorothy, a senior engineer, and Mr Chan Kin-hong, Keith, an engineer, both under the Boundary Crossing Facilities and Transport Services Division, remained dedicated and led our colleagues to make strenuous efforts to repair damaged traffic lights and the Cross-Harbour Tunnel for the public.
By mid-2019, Mr Chan Kin-hong, Keith, an engineer of the Boundary Crossing Facilities and Transport Services Division (BTSD), had been running its traffic lights maintenance unit for six years. Yet his team had never had to repair as many traffic lights as it would have to do in the second half year of 2019, when lights at some 750 road junctions were vandalised.
“The fact that we exhausted ten years’ supply of spare parts in just a few months shows the scale of the repair works,” said Mr Chan. Supported by several contractors, his team worked through numerous nights to repair traffic lights so that as many as possible could resume operation early next morning to ensure public safety. Some traffic light controllers were damaged too, which posed complications as road works would be necessary to replace the underground electric wiring. After months of hard work, all traffic junctions were back to operation by December 2019, and all repairs completed by July 2020. Protective measures were added to traffic lights and controllers at strategic locations as a precaution.
Meanwhile, BTSD senior engineer Ms Chan Ying-ying, Dorothy, led a team to repair the E&M facilities of the Cross-Harbour Tunnel, severely damaged in November 2019. Ms Chan co-ordinated and collaborated with various government departments and led a 100-plus EMSD team on-site. The Government’s target was to complete all repairs within 100 hours after site clearance.
“To make the most of precious time, we developed a rapid recovery plan and began repair works immediately after a half-day on-site assessment,” she recalled. Essential tasks were identified, such as resuming the normal operation of the toll systems, carrying out health checks for all E&M tunnel systems and finding enough spare parts for all repairs. “Sourcing spare parts was a challenge,” she said. Thanks to the help from other government departments and trade partners, the team got the spare parts needed for restoring systems. After working at full speed, all repairs were completed on schedule, and the tunnel was re-opened smoothly at 5 a.m. on 27 November 2019.
Ms Chan felt proud that the team had contributed to making life convenient for the public, which demonstrated EMSTF’s core service value and commitment.
“The fact that we exhausted ten years’ supply of spare parts in just a few months shows the scale of the repair works,” said Mr Chan. Supported by several contractors, his team worked through numerous nights to repair traffic lights so that as many as possible could resume operation early next morning to ensure public safety. Some traffic light controllers were damaged too, which posed complications as road works would be necessary to replace the underground electric wiring. After months of hard work, all traffic junctions were back to operation by December 2019, and all repairs completed by July 2020. Protective measures were added to traffic lights and controllers at strategic locations as a precaution.
Meanwhile, BTSD senior engineer Ms Chan Ying-ying, Dorothy, led a team to repair the E&M facilities of the Cross-Harbour Tunnel, severely damaged in November 2019. Ms Chan co-ordinated and collaborated with various government departments and led a 100-plus EMSD team on-site. The Government’s target was to complete all repairs within 100 hours after site clearance.
“To make the most of precious time, we developed a rapid recovery plan and began repair works immediately after a half-day on-site assessment,” she recalled. Essential tasks were identified, such as resuming the normal operation of the toll systems, carrying out health checks for all E&M tunnel systems and finding enough spare parts for all repairs. “Sourcing spare parts was a challenge,” she said. Thanks to the help from other government departments and trade partners, the team got the spare parts needed for restoring systems. After working at full speed, all repairs were completed on schedule, and the tunnel was re-opened smoothly at 5 a.m. on 27 November 2019.
Ms Chan felt proud that the team had contributed to making life convenient for the public, which demonstrated EMSTF’s core service value and commitment.
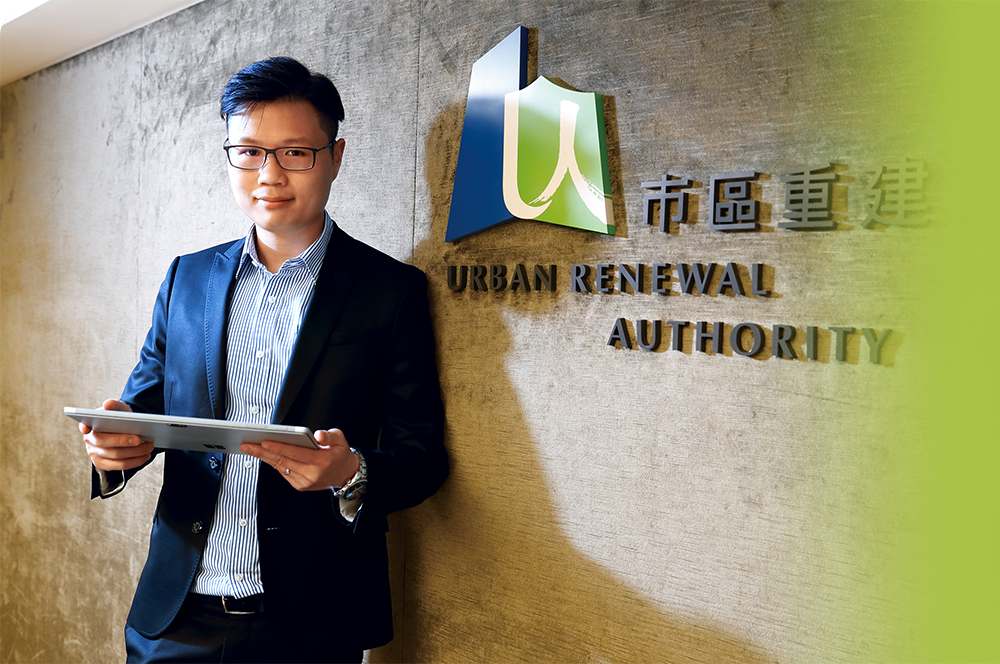
On Secondment to Help with Lift Modernisation in Community
Mr Cheung Ka-yu, Gary, Engineer of the General Legislation Division, has been seconded to the Urban Renewal Authority since August 2018 to support the implementation of the Government’s Lift Modernisation Subsidy Scheme. This is an account of his unusual assignment.
To enhance lift safety and further protect public safety, the Government has launched the Lift Modernisation Subsidy Scheme (LIMSS) to provide financial incentives and appropriate professional support for building owners in need to modernise their aged lifts. The LIMSS has been implemented in partnership with the Urban Renewal Authority (URA), which serves as the scheme’s administrator.
While the URA has considerable experience in implementing subsidy schemes for the rehabilitation of old buildings, the EMSD has the expertise of lift works as well as a sound understanding of the lift industry. Therefore, the EMSD deployed a professional team to the URA to provide technical support for the LIMSS. The partnership aims to ensure that the scheme is people-oriented and fairly conducted, taking into consideration the capacity of the lift industry. Mr Cheung Ka-yu, Gary, an Electrical and Mechanical Engineer of the General Legislation Division, together with a Senior Electrical and Mechanical Engineer, has been seconded to the URA since August 2018 to help with the drawing up of the details of the LIMSS and its implementation. Gary said, “Initially, the scheme had only a framework. Our first and foremost task was to finalise the details, including the scope of subsidy, setting of priorities, application details, etc., with a view to receiving the first round of applications in the first quarter of 2019.” With the concerted efforts of the team, the first round of applications was launched as scheduled.
Two rounds of applications were arranged, with overwhelming responses. About 1200 applications involving about 5000 lifts were received in the first round, which was close to the original target of the LIMSS. “In the past, owners might hesitate to upgrade their lifts due to financial considerations and a lack of technical knowledge and organisational capacity when implementing lift modernisation works. The introduction of the LIMSS can help them expedite the progress of lift modernisation,” Gary said.
Apart from working out the details of the LIMSS, Gary also applied his professional knowledge about lifts to help the URA recruit a resident consultant and prepare standard tender documents for lift modernisation works to ensure that every project would meet the relevant technical and safety standards. “To ensure smooth implementation and one-stop support for participating building owners, we took into consideration multiple factors when working out the technical details of the tender documents, including maintenance arrangements upon completion of modernisation works,” Gary added. Technical issues aside, the team also had to take on the challenges of how to minimise the inconvenience inevitably caused to residents, especially the elderly, in buildings with only one lift or lifts serving alternate floors, when their lifts were out of service for several months. “After discussions and joint studies with the Development Bureau (DEVB) and the URA, it was decided that the LIMSS would provide support services in this aspect, including delivery of meals, purchasing daily necessities on residents’ behalf, and provision of mechanised stair climbing devices,” Gary said.
Challenges continued to emerge. The second round of applications was launched in January 2020 during the COVID-19 outbreak. In the light of the epidemic, many owners’ corporations were unable to hold general meetings to discuss if they should join the LIMSS. “We have to be prepared to resolve problems come what may. As building owners could not meet to pass resolutions about applying for the LIMSS, we have, after discussions with the DEVB and the URA, decided to streamline the application process and allow flexibility for building owners to join the scheme by “submitting application forms first and providing supporting documents later”. We have also extended the application deadline to give owners more time to prepare their applications,” Gary said.
From conceptual framework to implementation, the EMSD has applied its professional expertise to successfully implement the LIMSS in collaboration with the URA. The scheme not only helps buildings in need to expedite modernisation of their aged lifts, but also raises public awareness of the importance of lift maintenance and safety. Gary believes that it is meaningful to be part of the professional team of the scheme to help enhance the safety of aged lifts.
While the URA has considerable experience in implementing subsidy schemes for the rehabilitation of old buildings, the EMSD has the expertise of lift works as well as a sound understanding of the lift industry. Therefore, the EMSD deployed a professional team to the URA to provide technical support for the LIMSS. The partnership aims to ensure that the scheme is people-oriented and fairly conducted, taking into consideration the capacity of the lift industry. Mr Cheung Ka-yu, Gary, an Electrical and Mechanical Engineer of the General Legislation Division, together with a Senior Electrical and Mechanical Engineer, has been seconded to the URA since August 2018 to help with the drawing up of the details of the LIMSS and its implementation. Gary said, “Initially, the scheme had only a framework. Our first and foremost task was to finalise the details, including the scope of subsidy, setting of priorities, application details, etc., with a view to receiving the first round of applications in the first quarter of 2019.” With the concerted efforts of the team, the first round of applications was launched as scheduled.
Two rounds of applications were arranged, with overwhelming responses. About 1200 applications involving about 5000 lifts were received in the first round, which was close to the original target of the LIMSS. “In the past, owners might hesitate to upgrade their lifts due to financial considerations and a lack of technical knowledge and organisational capacity when implementing lift modernisation works. The introduction of the LIMSS can help them expedite the progress of lift modernisation,” Gary said.
Apart from working out the details of the LIMSS, Gary also applied his professional knowledge about lifts to help the URA recruit a resident consultant and prepare standard tender documents for lift modernisation works to ensure that every project would meet the relevant technical and safety standards. “To ensure smooth implementation and one-stop support for participating building owners, we took into consideration multiple factors when working out the technical details of the tender documents, including maintenance arrangements upon completion of modernisation works,” Gary added. Technical issues aside, the team also had to take on the challenges of how to minimise the inconvenience inevitably caused to residents, especially the elderly, in buildings with only one lift or lifts serving alternate floors, when their lifts were out of service for several months. “After discussions and joint studies with the Development Bureau (DEVB) and the URA, it was decided that the LIMSS would provide support services in this aspect, including delivery of meals, purchasing daily necessities on residents’ behalf, and provision of mechanised stair climbing devices,” Gary said.
Challenges continued to emerge. The second round of applications was launched in January 2020 during the COVID-19 outbreak. In the light of the epidemic, many owners’ corporations were unable to hold general meetings to discuss if they should join the LIMSS. “We have to be prepared to resolve problems come what may. As building owners could not meet to pass resolutions about applying for the LIMSS, we have, after discussions with the DEVB and the URA, decided to streamline the application process and allow flexibility for building owners to join the scheme by “submitting application forms first and providing supporting documents later”. We have also extended the application deadline to give owners more time to prepare their applications,” Gary said.
From conceptual framework to implementation, the EMSD has applied its professional expertise to successfully implement the LIMSS in collaboration with the URA. The scheme not only helps buildings in need to expedite modernisation of their aged lifts, but also raises public awareness of the importance of lift maintenance and safety. Gary believes that it is meaningful to be part of the professional team of the scheme to help enhance the safety of aged lifts.
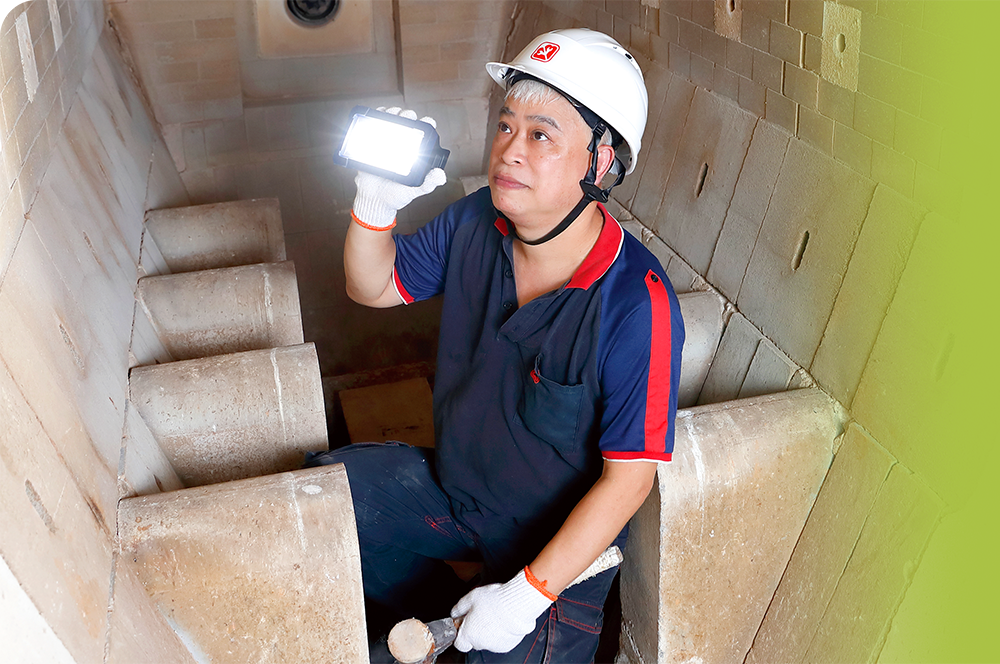
Perfecting the Art of Cremator Maintenance
Mr Fu King-wai, who has been handling brick-repairing work for cremators for almost 40 years, considers his duty to be a test of endurance. He has to repair cracked bricks and conduct condition checking of bricks inside the cremator with limited space.
Mr Fu King-wai has spent almost 40 years perfecting the art of cremator maintenance. Now a works supervisor I of our Municipal Sector Division, he has served at most government crematoria in Hong Kong since joining the EMSD in 1982. The Secretary for the Civil Service’s Commendation Award 2019 that he received last year was a well-earned recognition of his outstanding contribution.
“In the old days, the overseas cremator manufacturer would not release the design drawings to us. I had no choice but to stand at the cremator door and quietly observe how the manufacturer’s people laid the firebricks, making a pencil drawing as a guide,” Mr Fu explained. It took a full month for the manufacturer’s people to lay all five layers of firebricks against the cremator’s metal frame, which was as tall as a three-storey building. This month of careful observation and drawing sparked Mr Fu’s interest in firebricks and cremators, leading to a life-long vocation.
“Since a damaged brick may be buried between layers of ‘healthy’ bricks, it is important that we can correctly re-lay the ‘healthy’ bricks after replacing the damaged one, otherwise the whole structure may collapse,” he said. He is also a walking encyclopaedia of cremator systems and an expert in O&M and troubleshooting. Recognising the great potential of technology in improving cremator system monitoring and performance as well as occupational safety, his team has piloted many technological solutions and devices in recent years. This was on top of carrying out rigorous scheduled maintenance of cremators every two to six days, plus an annual overhaul that sees all parts dismantled, cleaned and repaired.
Now working at Kwai Chung Crematorium, Mr Fu never forgets that the team’s mission is to provide quality O&M service so that the deceased can complete their last journey with dignity and the family can receive the ashes promptly, on the day after cremation. Two years to retirement, Mr Fu looks forward to passing the baton to the younger generation, for whom he advises “patience and experience”.
“In the old days, the overseas cremator manufacturer would not release the design drawings to us. I had no choice but to stand at the cremator door and quietly observe how the manufacturer’s people laid the firebricks, making a pencil drawing as a guide,” Mr Fu explained. It took a full month for the manufacturer’s people to lay all five layers of firebricks against the cremator’s metal frame, which was as tall as a three-storey building. This month of careful observation and drawing sparked Mr Fu’s interest in firebricks and cremators, leading to a life-long vocation.
“Since a damaged brick may be buried between layers of ‘healthy’ bricks, it is important that we can correctly re-lay the ‘healthy’ bricks after replacing the damaged one, otherwise the whole structure may collapse,” he said. He is also a walking encyclopaedia of cremator systems and an expert in O&M and troubleshooting. Recognising the great potential of technology in improving cremator system monitoring and performance as well as occupational safety, his team has piloted many technological solutions and devices in recent years. This was on top of carrying out rigorous scheduled maintenance of cremators every two to six days, plus an annual overhaul that sees all parts dismantled, cleaned and repaired.
Now working at Kwai Chung Crematorium, Mr Fu never forgets that the team’s mission is to provide quality O&M service so that the deceased can complete their last journey with dignity and the family can receive the ashes promptly, on the day after cremation. Two years to retirement, Mr Fu looks forward to passing the baton to the younger generation, for whom he advises “patience and experience”.

Expediting Lift Modernisation Works Approval for Users’ Convenience
Mechanical inspector Mr Fung Siu-hang and his team helped expedite the approval of resumption permits for the only two lifts in a factory building in Chai Wan, making life much easier for its tenants.
Inspection, investigation, enforcement… regulatory tasks sound rigid, but the team at General Legislation Division (GLD) is accommodating. For example, when Hop Shi Factory Building in Chai Wan decided to simultaneously modernise the only two lifts serving the building, which caused unspeakable inconvenience to the tenants in the building, the GLD team pulled out all the stops to expedite the approval process for issuing a resumption permit. What would normally take more than 10 days was done within two days. Their work was shortlisted in EMSD’s 2019/20 “Good People, Good Deeds Commendation Scheme” campaign, and shows that regulators are empathetic.
Mechanical inspector Mr Fung Siu-hang was part of the team handling this case. He recalled that the EMSD issued a notice to the Owners’ Corporation of the building to advise adding an unintended car movement protector to its aged lifts that had been in use for many years and missing the safety installations compliant with the latest safety standards. The building however had both lifts out of service at the same time for the lift modernisation works. Its tenants were forced to put up makeshift planks on staircases to strenuously move goods up and down.
“The building’s management called us to ask for speeding up the approval process. We wondered why the urgency, so we made a site inspection, and found that the tenants were indeed in a dire situation. In the spirit of serving the public, we agreed to facilitate the approval process after they fulfilled all application requirements,” Siu-hang said.
As promised, the team dispatched two teams of inspectors to simultaneously monitor the testing of the two lifts by the contractors after receiving the building’s application. Enforcement standards were not compromised for speed, though. As the loading test was missing, the team asked the contractors to get it done that afternoon to make sure the lifts were safe even if overloaded.
“The whole process involved three groups of colleagues: inspectors monitored onsite testing, engineers verified test results and administrative colleagues prepared documents for the chief engineer to sign off on the resumption permit. We worked together flexibly to complete the entire process that night.” The helpful initiative has been commended, not only as a model case of “Good People, Good Deeds Commendation Scheme” but also by the factory building’s owner, who sent a note to the team to express gratitude.
Mechanical inspector Mr Fung Siu-hang was part of the team handling this case. He recalled that the EMSD issued a notice to the Owners’ Corporation of the building to advise adding an unintended car movement protector to its aged lifts that had been in use for many years and missing the safety installations compliant with the latest safety standards. The building however had both lifts out of service at the same time for the lift modernisation works. Its tenants were forced to put up makeshift planks on staircases to strenuously move goods up and down.
“The building’s management called us to ask for speeding up the approval process. We wondered why the urgency, so we made a site inspection, and found that the tenants were indeed in a dire situation. In the spirit of serving the public, we agreed to facilitate the approval process after they fulfilled all application requirements,” Siu-hang said.
As promised, the team dispatched two teams of inspectors to simultaneously monitor the testing of the two lifts by the contractors after receiving the building’s application. Enforcement standards were not compromised for speed, though. As the loading test was missing, the team asked the contractors to get it done that afternoon to make sure the lifts were safe even if overloaded.
“The whole process involved three groups of colleagues: inspectors monitored onsite testing, engineers verified test results and administrative colleagues prepared documents for the chief engineer to sign off on the resumption permit. We worked together flexibly to complete the entire process that night.” The helpful initiative has been commended, not only as a model case of “Good People, Good Deeds Commendation Scheme” but also by the factory building’s owner, who sent a note to the team to express gratitude.
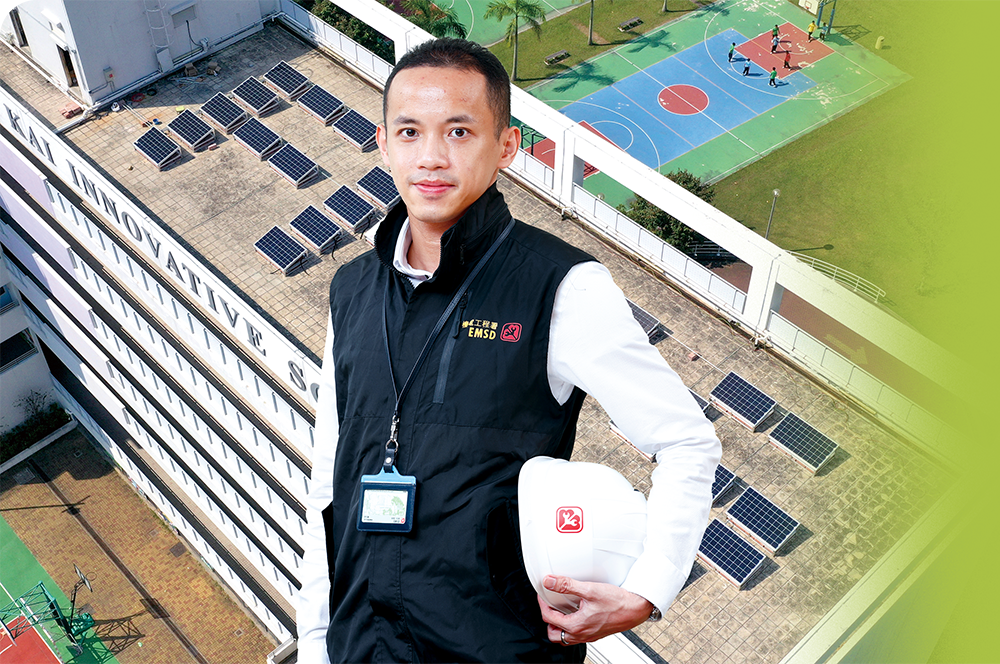
Connecting Future Generations with Renewable Energy
The Solar Harvest programme has taken Mr Lee Hang-mun, Edward, an engineer in our Energy Efficiency Office, to work with students and teachers at schools to build small-scale solar photovoltaic systems. He shares his experience in promoting renewable energy to our future generation.
Mr Lee Hang-mun, Edward, is keen to contribute to the field of environmental protection through his profession as an engineer. After a number of years in the private sector, Edward joined the Energy Efficiency Office of the EMSD in July 2019 as a Building Services Engineer. He is responsible for implementing the new Solar Harvest programme, which is designed to provide one-stop service and full subsidy to help eligible schools and welfare non-governmental organisations (welfare NGOs) install small-scale solar photovoltaic (PV) systems and join the Feed-in Tariff (FiT) Scheme offered by the two local power companies.
“Through Solar Harvest, we promote renewable energy (RE) to schools and welfare NGOs from different perspectives, thereby obtaining multiple environmental achievements, including the enhancement of environmental awareness among students, young people and people from different sectors,” Edward said.
After joining the EMSD, Edward first implemented the programme for the first batch of shortlisted schools including Fung Kai Innovative School in Sheung Shui. To explore the school’s expectations for the programme, Edward and the designer paid a visit to the school to meet with the principal and teachers-in-charge. In addition, Edward’s team added sensors to the school’s solar PV system to collect data on solar power generation for the development of teaching materials on renewable energy. Through this programme, students were able to track the data and experience first-hand the benefits of renewable energy, adding more fun to learning. Edward’s team also interacted with students, encouraging them to unleash their creativity by designing patterns for the placement of solar PV panels. Other than alphabets, many interesting designs were also presented. A number of schools adopted the students’ designs, thus enhancing their sense of engagement with the programme.
Well-received by schools and welfare NGOs, the five-year Solar Harvest programme received more than 210 applications in its first year of implementation. Last year, Edward’s team assisted 50 schools and welfare NGOs to install solar PV systems. Participating schools and welfare NGOs also received payments from the FiT Scheme. In order to benefit even more schools and welfare NGOs, Edward’s team will be expanded to complete more installation works in 2020/21.
“We hope to benefit more schools and welfare NGOs with our Solar Harvest programme as quickly as possible. We will also showcase successful cases, such as Fung Kai Innovative School, in order to promote the programme to schools through their sponsoring bodies. With more schools taking part in the programme, more students will be able to learn about RE and the importance of energy efficiency with first-hand experience. I am most motivated to combat climate change by cultivating and harvesting electricity together with the participating schools and welfare NGOs,” Edward said.
“Through Solar Harvest, we promote renewable energy (RE) to schools and welfare NGOs from different perspectives, thereby obtaining multiple environmental achievements, including the enhancement of environmental awareness among students, young people and people from different sectors,” Edward said.
After joining the EMSD, Edward first implemented the programme for the first batch of shortlisted schools including Fung Kai Innovative School in Sheung Shui. To explore the school’s expectations for the programme, Edward and the designer paid a visit to the school to meet with the principal and teachers-in-charge. In addition, Edward’s team added sensors to the school’s solar PV system to collect data on solar power generation for the development of teaching materials on renewable energy. Through this programme, students were able to track the data and experience first-hand the benefits of renewable energy, adding more fun to learning. Edward’s team also interacted with students, encouraging them to unleash their creativity by designing patterns for the placement of solar PV panels. Other than alphabets, many interesting designs were also presented. A number of schools adopted the students’ designs, thus enhancing their sense of engagement with the programme.
Well-received by schools and welfare NGOs, the five-year Solar Harvest programme received more than 210 applications in its first year of implementation. Last year, Edward’s team assisted 50 schools and welfare NGOs to install solar PV systems. Participating schools and welfare NGOs also received payments from the FiT Scheme. In order to benefit even more schools and welfare NGOs, Edward’s team will be expanded to complete more installation works in 2020/21.
“We hope to benefit more schools and welfare NGOs with our Solar Harvest programme as quickly as possible. We will also showcase successful cases, such as Fung Kai Innovative School, in order to promote the programme to schools through their sponsoring bodies. With more schools taking part in the programme, more students will be able to learn about RE and the importance of energy efficiency with first-hand experience. I am most motivated to combat climate change by cultivating and harvesting electricity together with the participating schools and welfare NGOs,” Edward said.
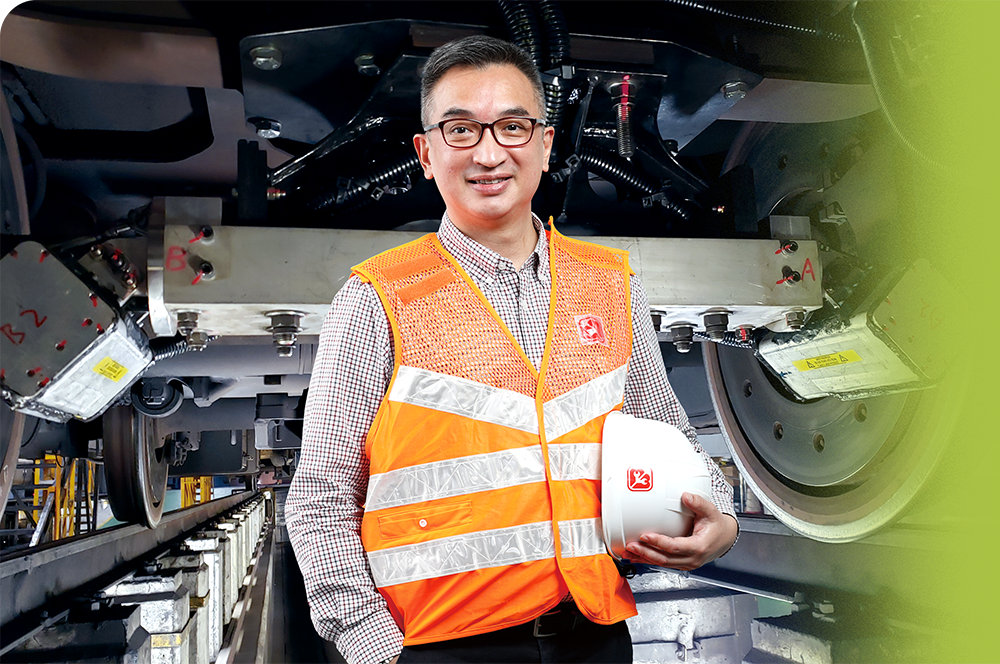
Staying Calm to Co-ordinate Major Railway Incident Investigation
Major incident investigations are never easy, as onsite situations are unpredictable and the evidences must be gathered promptly. Railways Branch Senior Engineer Mr Li Yick-fai, Ernest, recalls how he co-ordinates the investigation into the MTR Hung Hom Station derailment incident.
On 17 September 2019, at the time when Mr Li Yick-fai, Ernest, Senior Engineer of the Railways Branch (RB), returned to the EMSD Headquarters for work, he received a call about a serious incident, in which an East Rail Line (EAL) train had derailed while entering Hung Hom Station. He ran into the office to gather colleagues and rushed to the scene with about ten people. Ernest is a veteran in handling electrical and gas incidents as he has served in various posts in the EMSD. Although he was nervous, Ernest could still remain calm in the face of this serious incident, the firstever derailment of an EAL train carrying passengers.
The site of the incident was extensive, making the investigation and evidence collection even more complicated and difficult. “First, we had to gauge the situation of the scene to ascertain how serious the incident was, and whether there were casualties. Then we had to determine how services were affected and what might have caused the incident. We did a quick tabulation of parts and equipment on site, and the degree of damage to the tracks, and then checked if any CCTV systems near the Station had captured footage of the incident. Additionally, we had to gather relevant information for the Secretary for Transport and Housing and our Director to make responses to media enquiries, as well as co-ordinating with the MTR Corporation Limited (MTRCL) on their repair plans and work flow,” Ernest recalled.
While the RB team was conducting on-site evidence collection, the MTRCL carried out repairs. Train services at Hung Hom Station partially resumed by 6 a.m. the next morning. Repairs continued for several nights after EAL services had finished for the day. Throughout this period, Ernest and his colleagues took turns to monitor the repairs and testing of key components including track gauge, welded joints, sleepers, and point machines at turnouts. A test run with an empty train was also carried out to confirm the safe and smooth operation of the service. The team approved a full resumption of services by the MTRCL through the affected rail section only after all the test data was satisfactory.
After the incident, the RB sought assistance from overseas experts experienced in investigating major railway incidents. Subsequently, the “Technical Investigation Report on Train Derailment Incident at Hung Hom Station on MTR East Rail Line” was released in March 2020, which recommended a number of improvement measures for the MTRCL to implement, so as to ensure that similar incidents would not happen again.
Ernest said, “As a regulator, the EMSD focuses on using our expertise to protect public safety. Upon completion of the report, we kept monitoring the MTRCL’s implementation of the recommended remedial measures. Since this serious incident, the RB has stepped up its regulatory work to ensure railway safety and to regain public confidence in our railway systems.”
The site of the incident was extensive, making the investigation and evidence collection even more complicated and difficult. “First, we had to gauge the situation of the scene to ascertain how serious the incident was, and whether there were casualties. Then we had to determine how services were affected and what might have caused the incident. We did a quick tabulation of parts and equipment on site, and the degree of damage to the tracks, and then checked if any CCTV systems near the Station had captured footage of the incident. Additionally, we had to gather relevant information for the Secretary for Transport and Housing and our Director to make responses to media enquiries, as well as co-ordinating with the MTR Corporation Limited (MTRCL) on their repair plans and work flow,” Ernest recalled.
While the RB team was conducting on-site evidence collection, the MTRCL carried out repairs. Train services at Hung Hom Station partially resumed by 6 a.m. the next morning. Repairs continued for several nights after EAL services had finished for the day. Throughout this period, Ernest and his colleagues took turns to monitor the repairs and testing of key components including track gauge, welded joints, sleepers, and point machines at turnouts. A test run with an empty train was also carried out to confirm the safe and smooth operation of the service. The team approved a full resumption of services by the MTRCL through the affected rail section only after all the test data was satisfactory.
After the incident, the RB sought assistance from overseas experts experienced in investigating major railway incidents. Subsequently, the “Technical Investigation Report on Train Derailment Incident at Hung Hom Station on MTR East Rail Line” was released in March 2020, which recommended a number of improvement measures for the MTRCL to implement, so as to ensure that similar incidents would not happen again.
Ernest said, “As a regulator, the EMSD focuses on using our expertise to protect public safety. Upon completion of the report, we kept monitoring the MTRCL’s implementation of the recommended remedial measures. Since this serious incident, the RB has stepped up its regulatory work to ensure railway safety and to regain public confidence in our railway systems.”