Staff Highlights
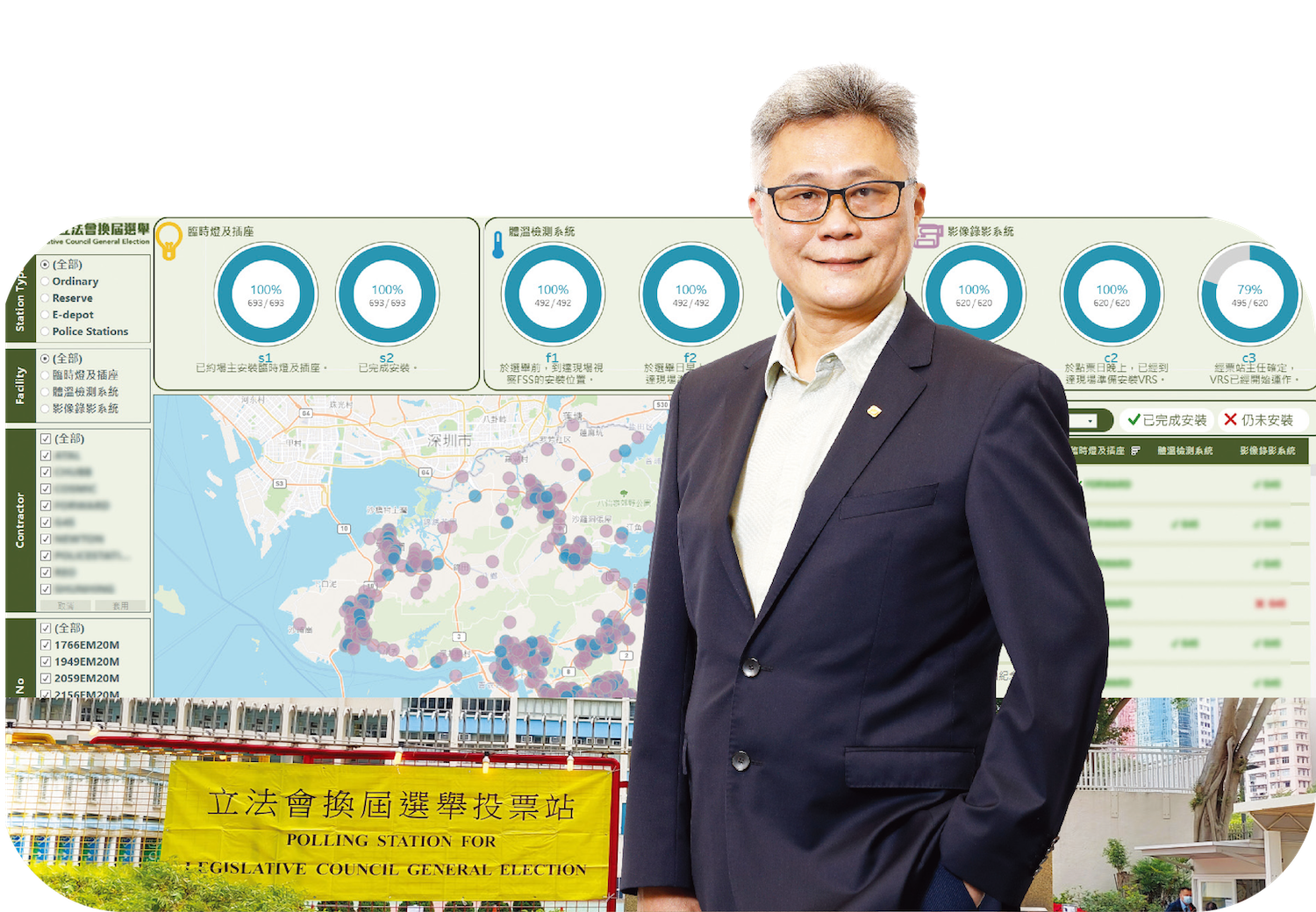
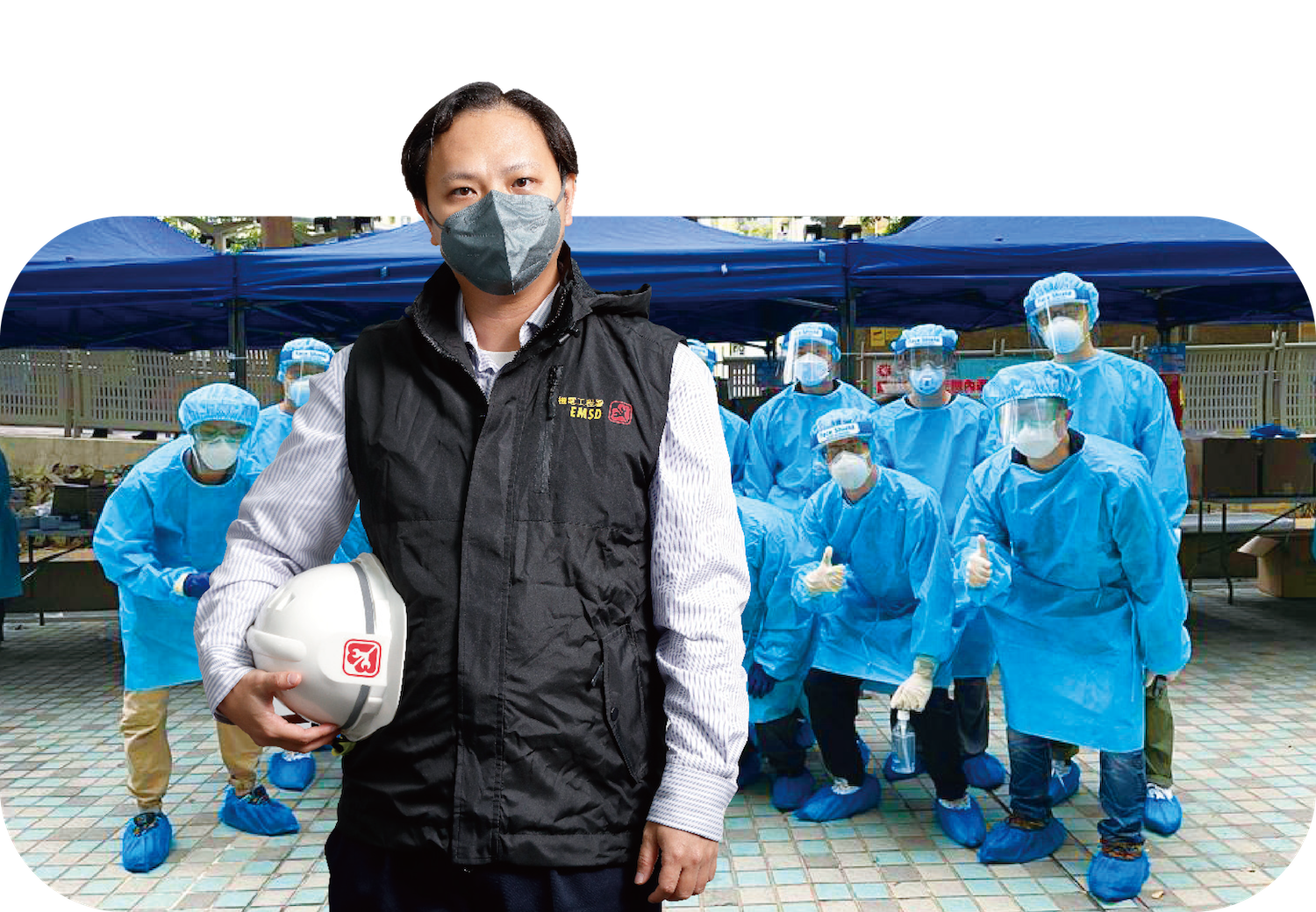
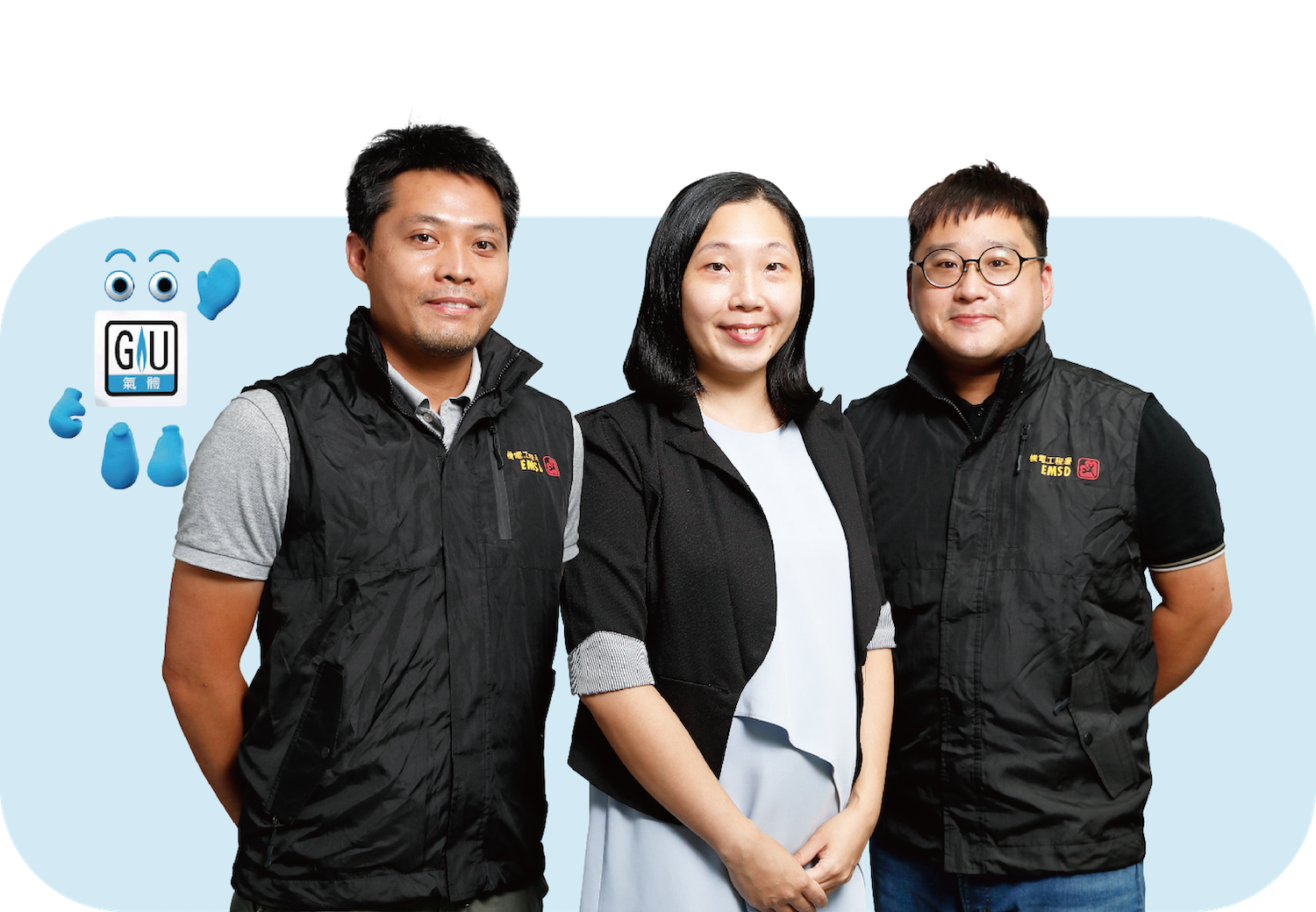
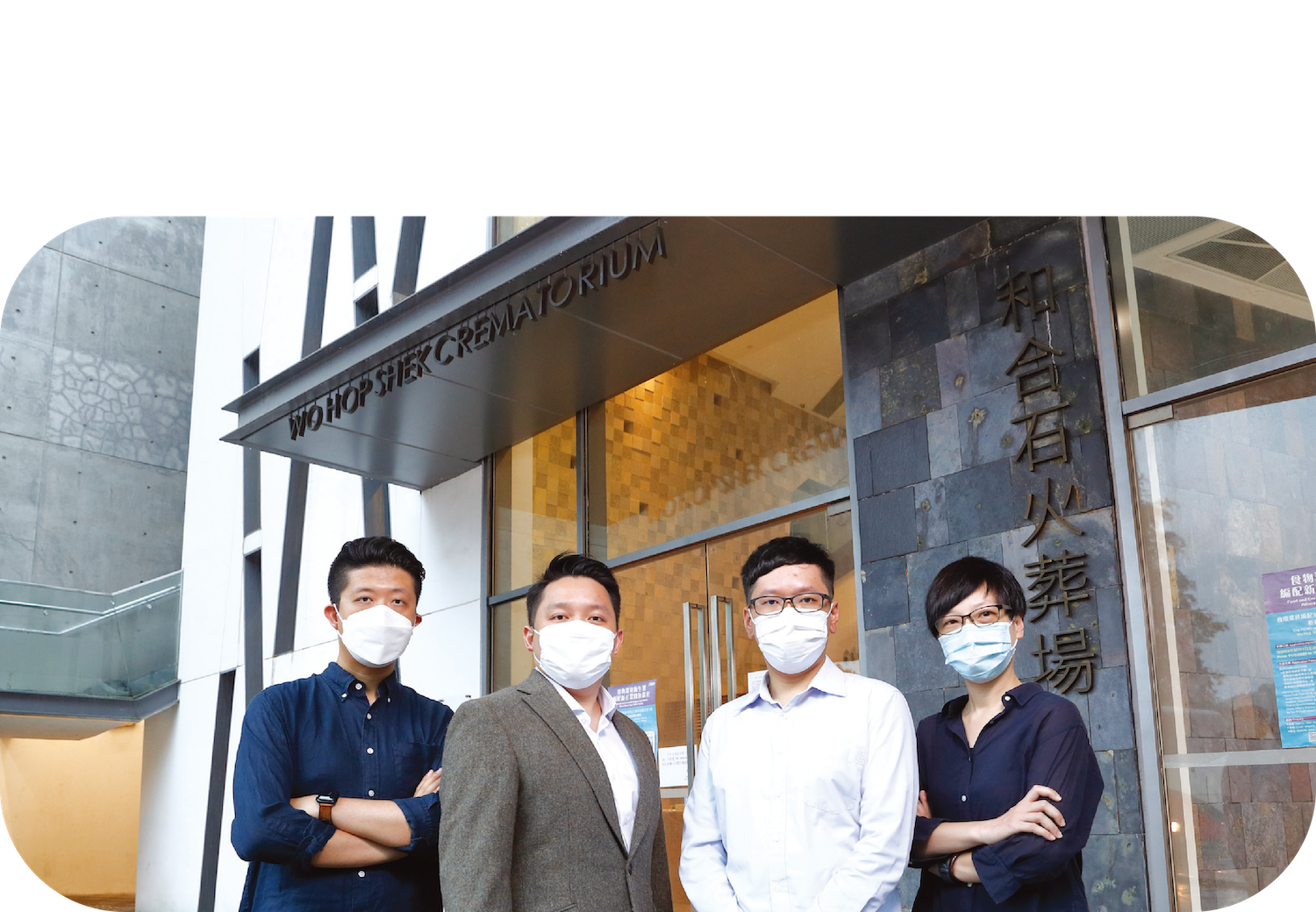
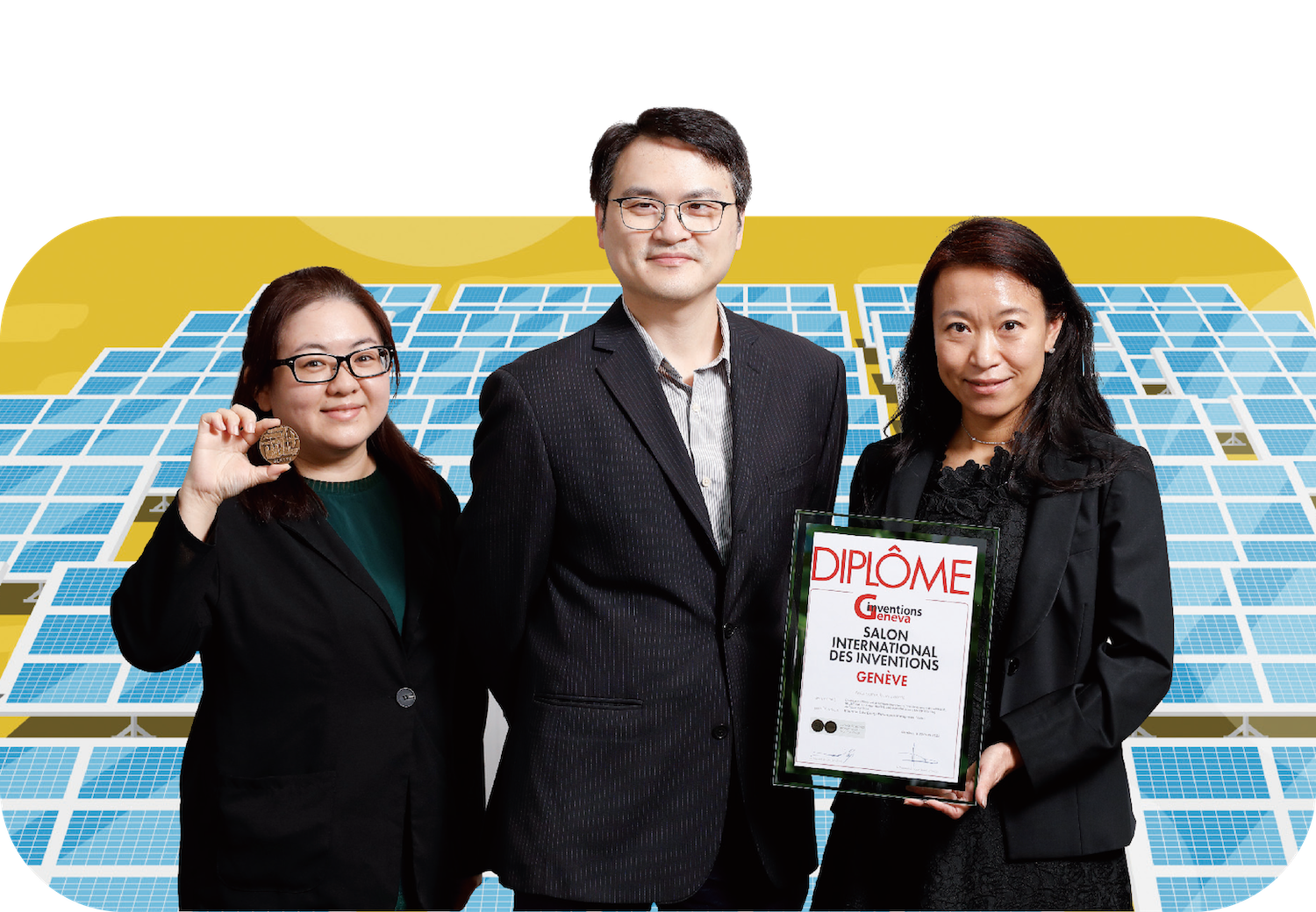


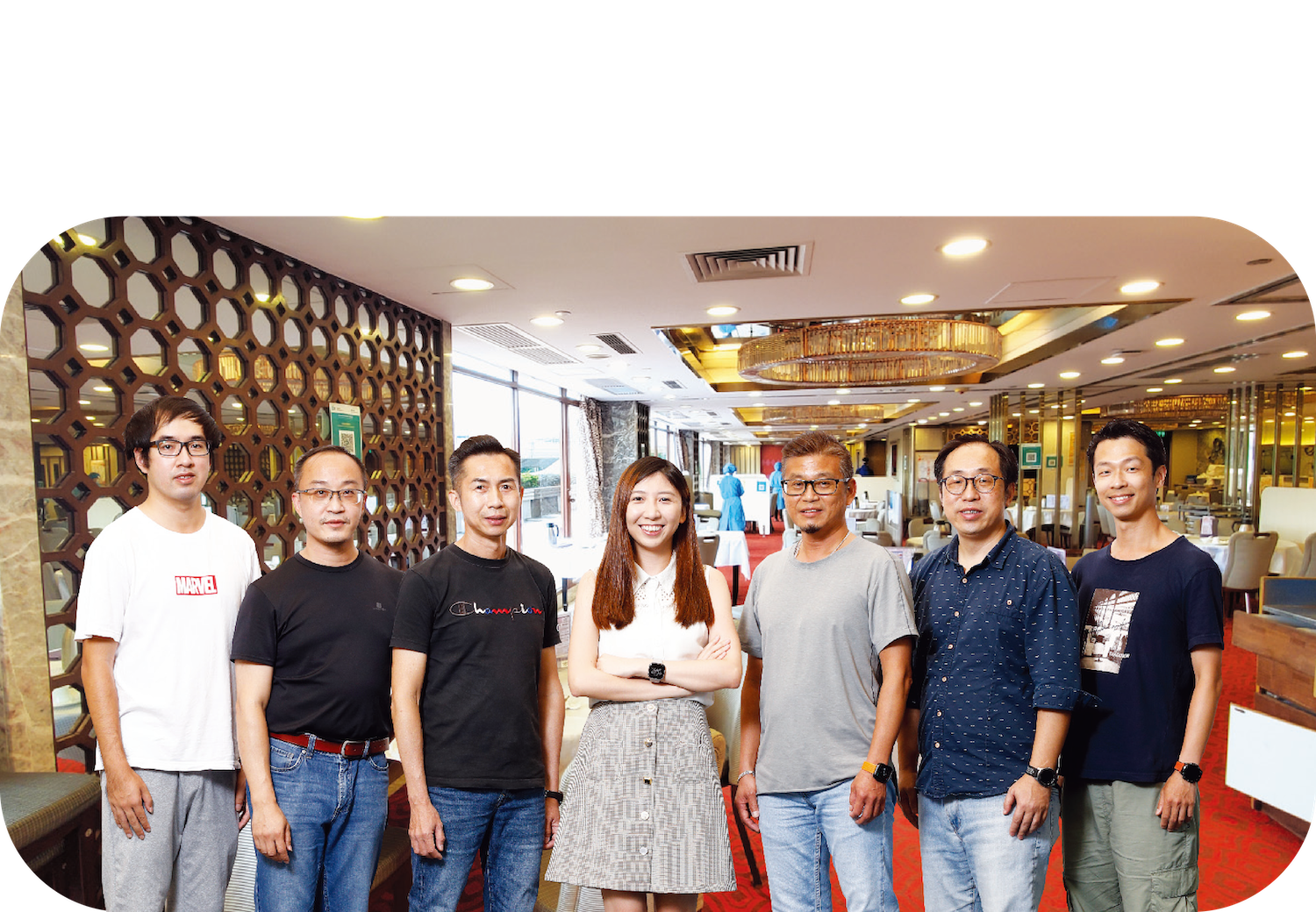
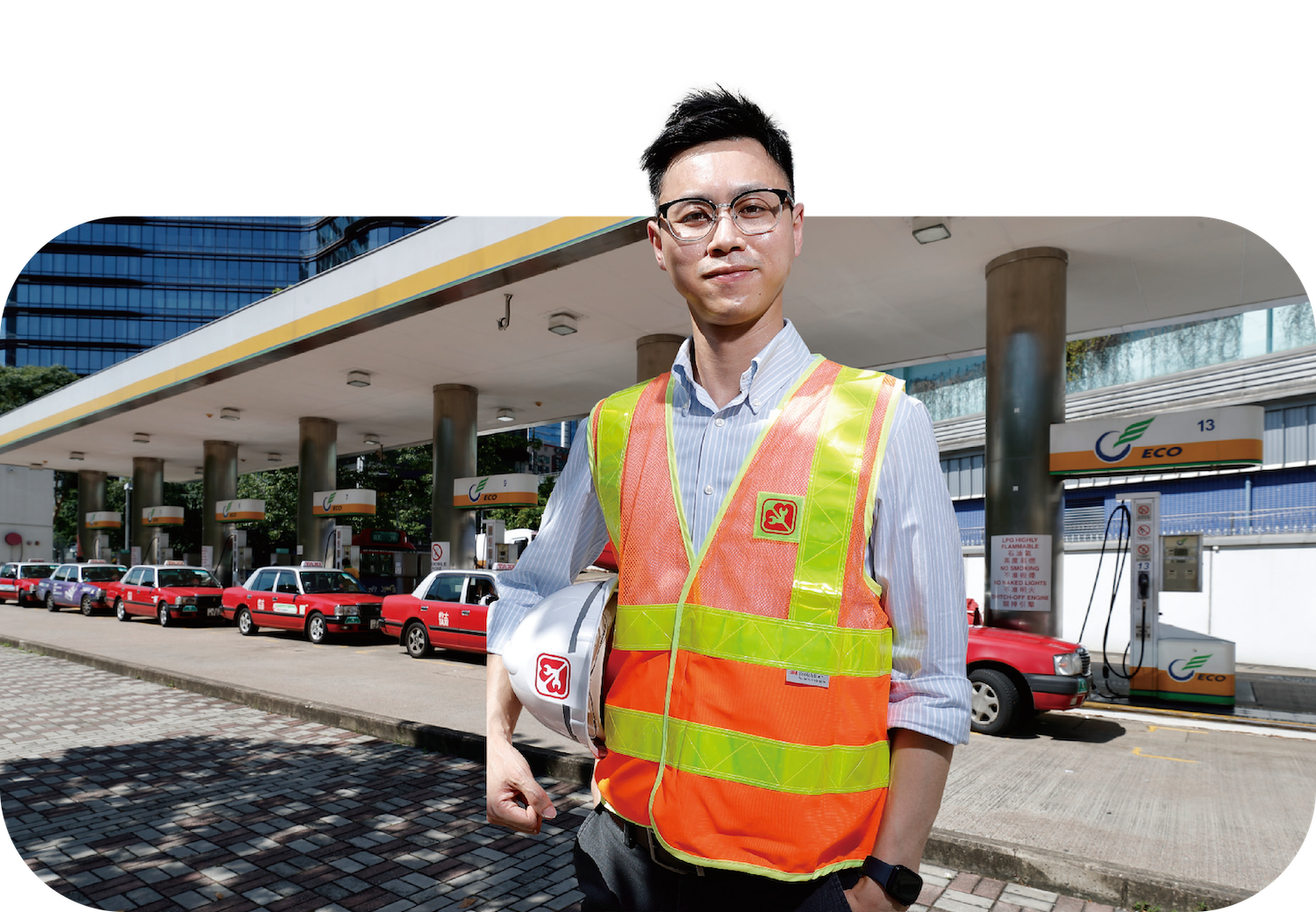




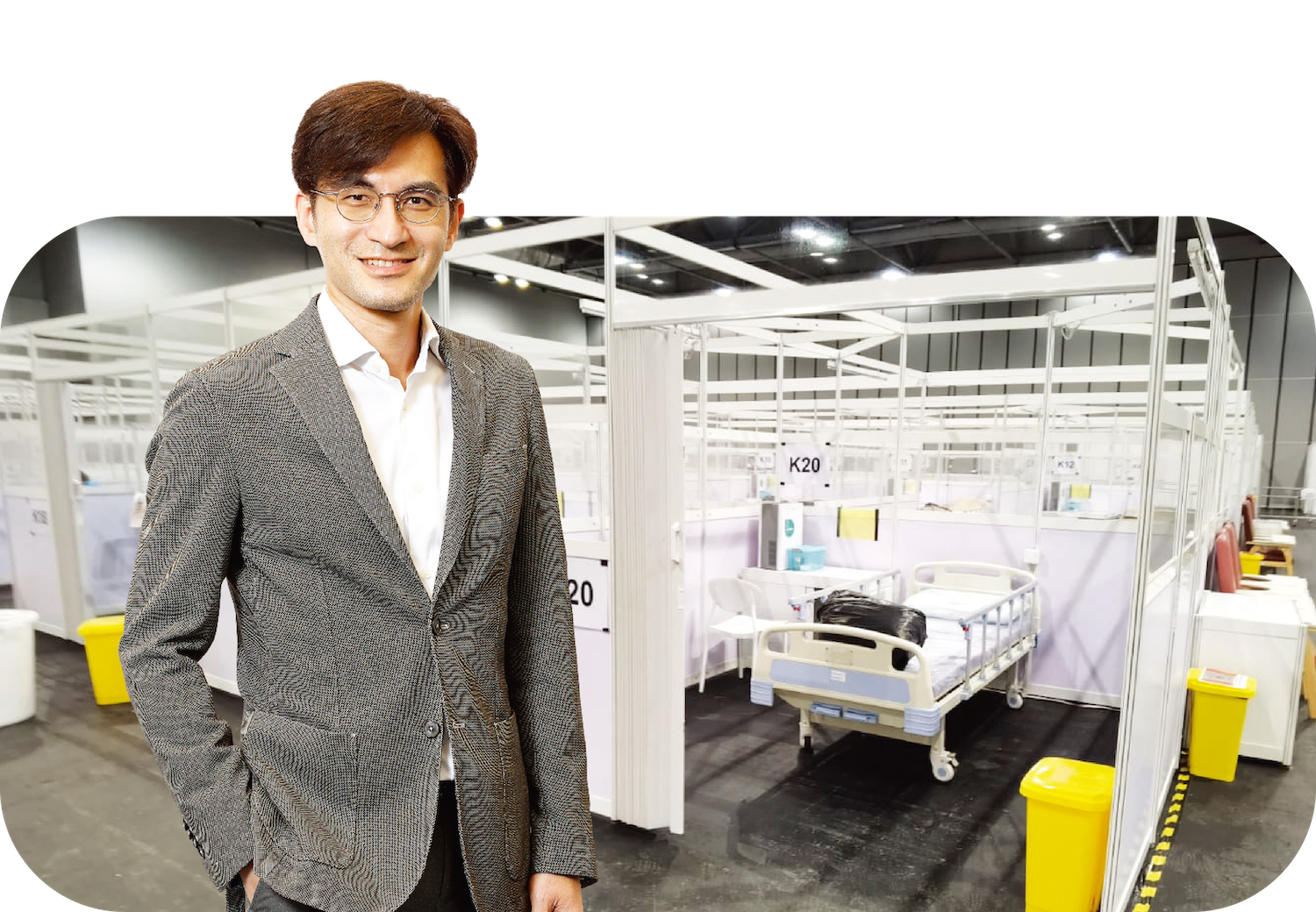
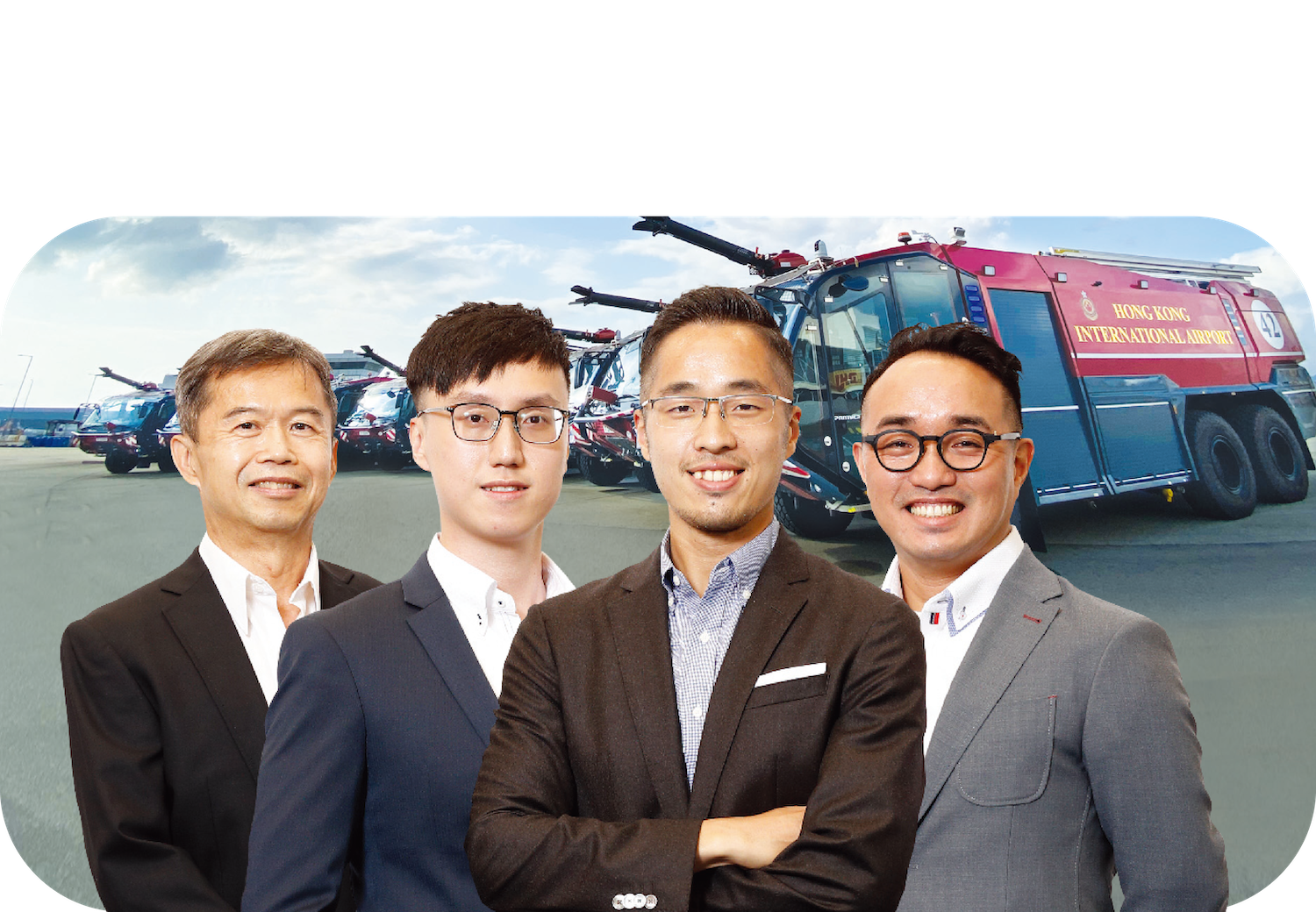

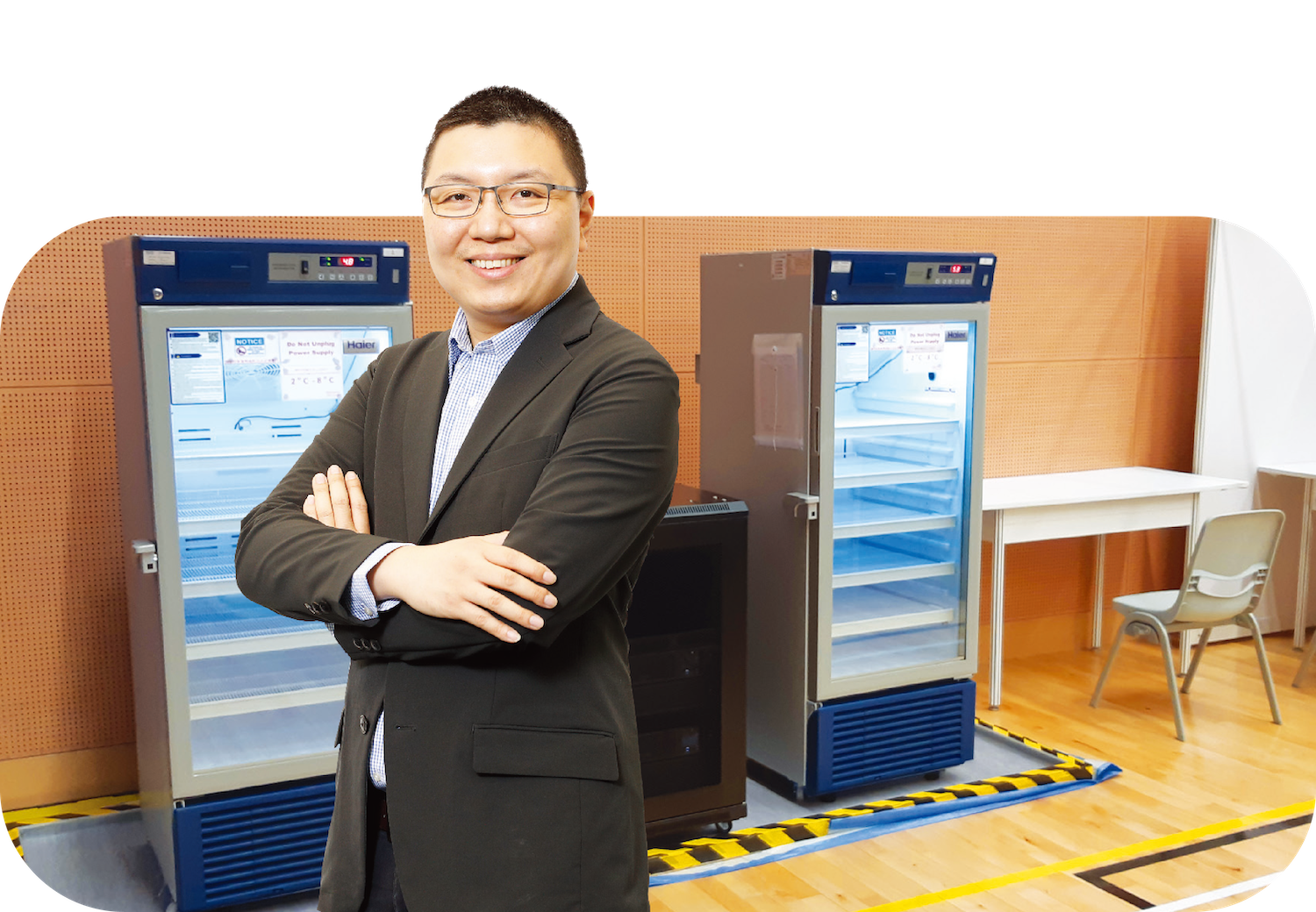
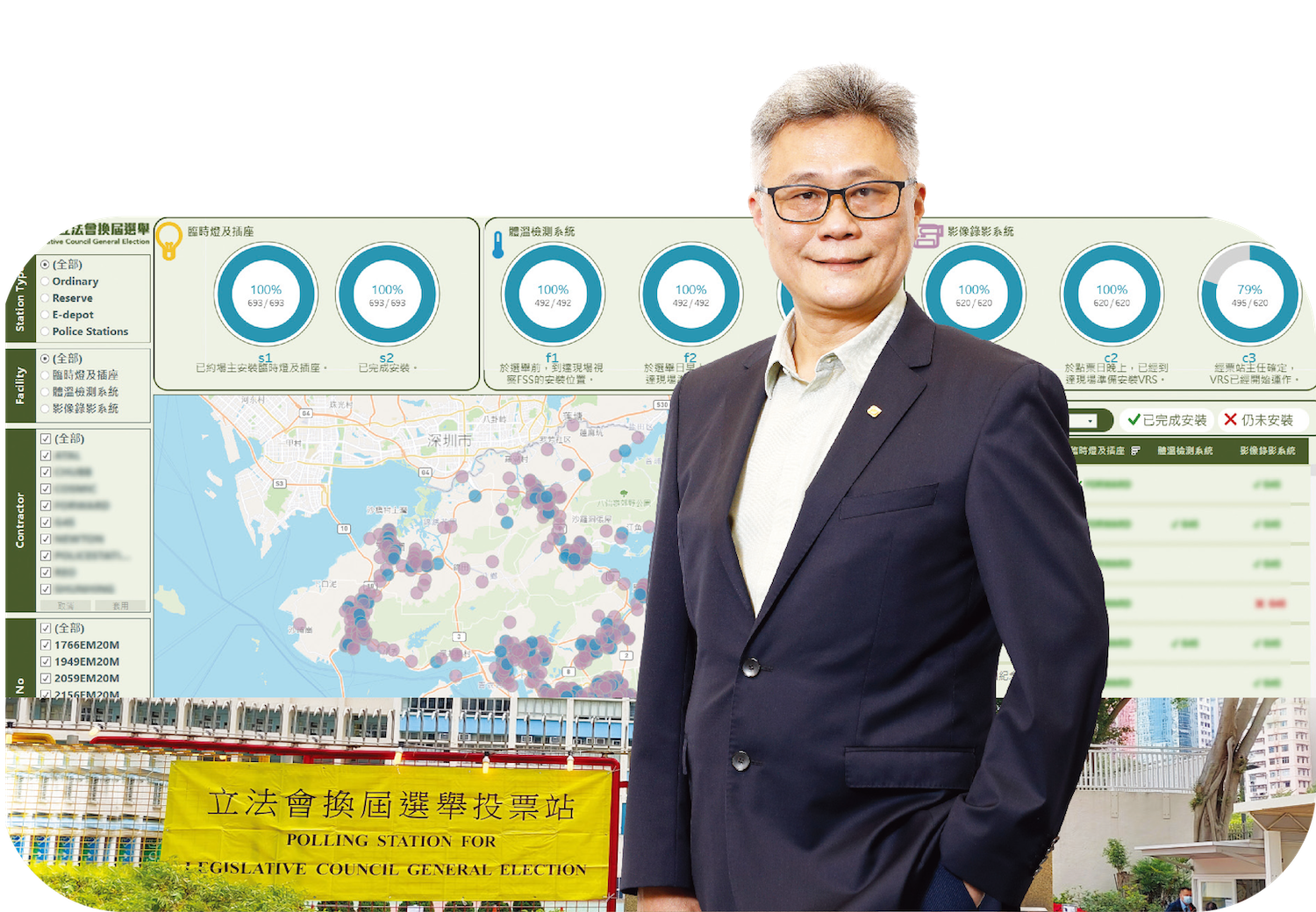
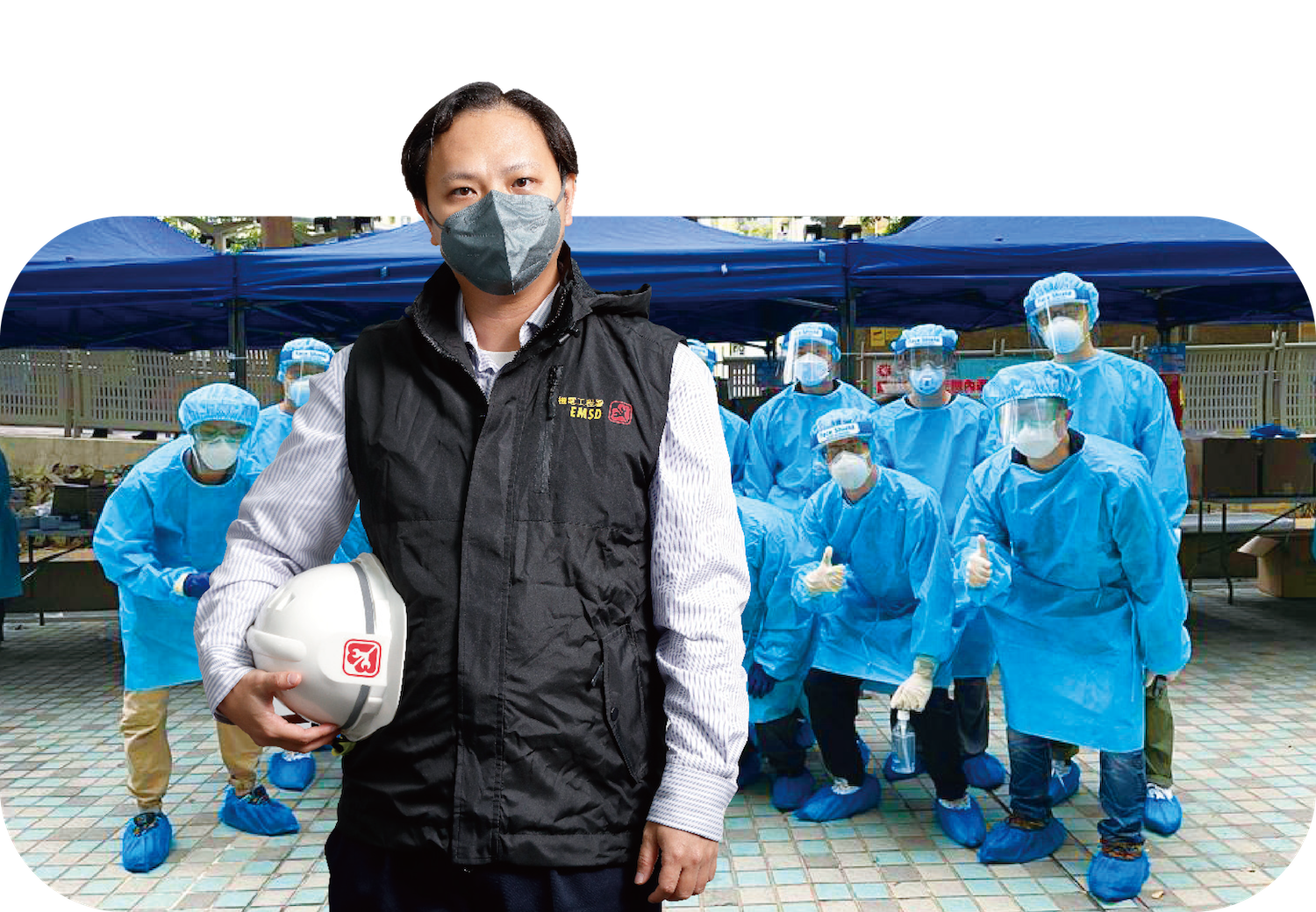
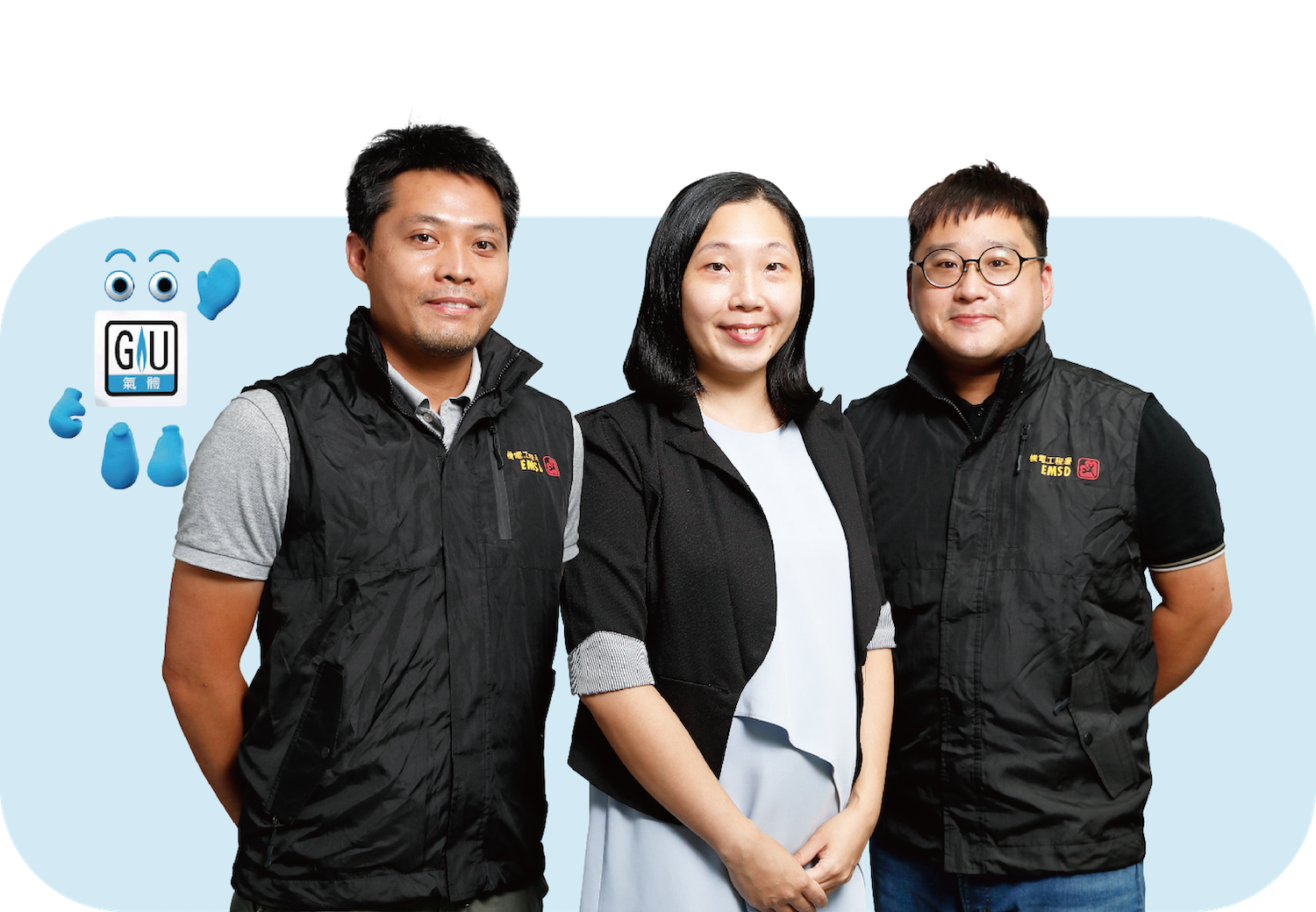
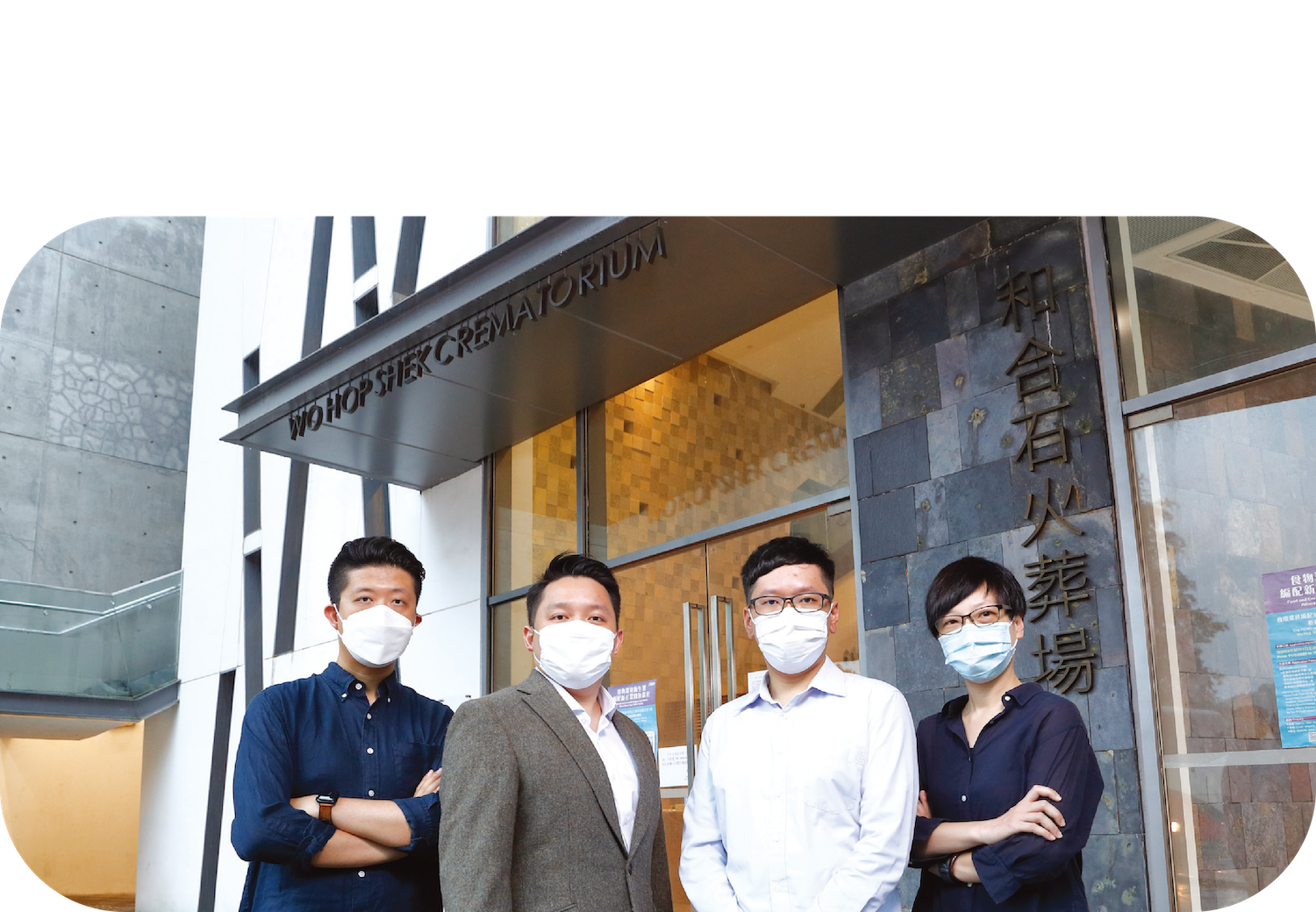
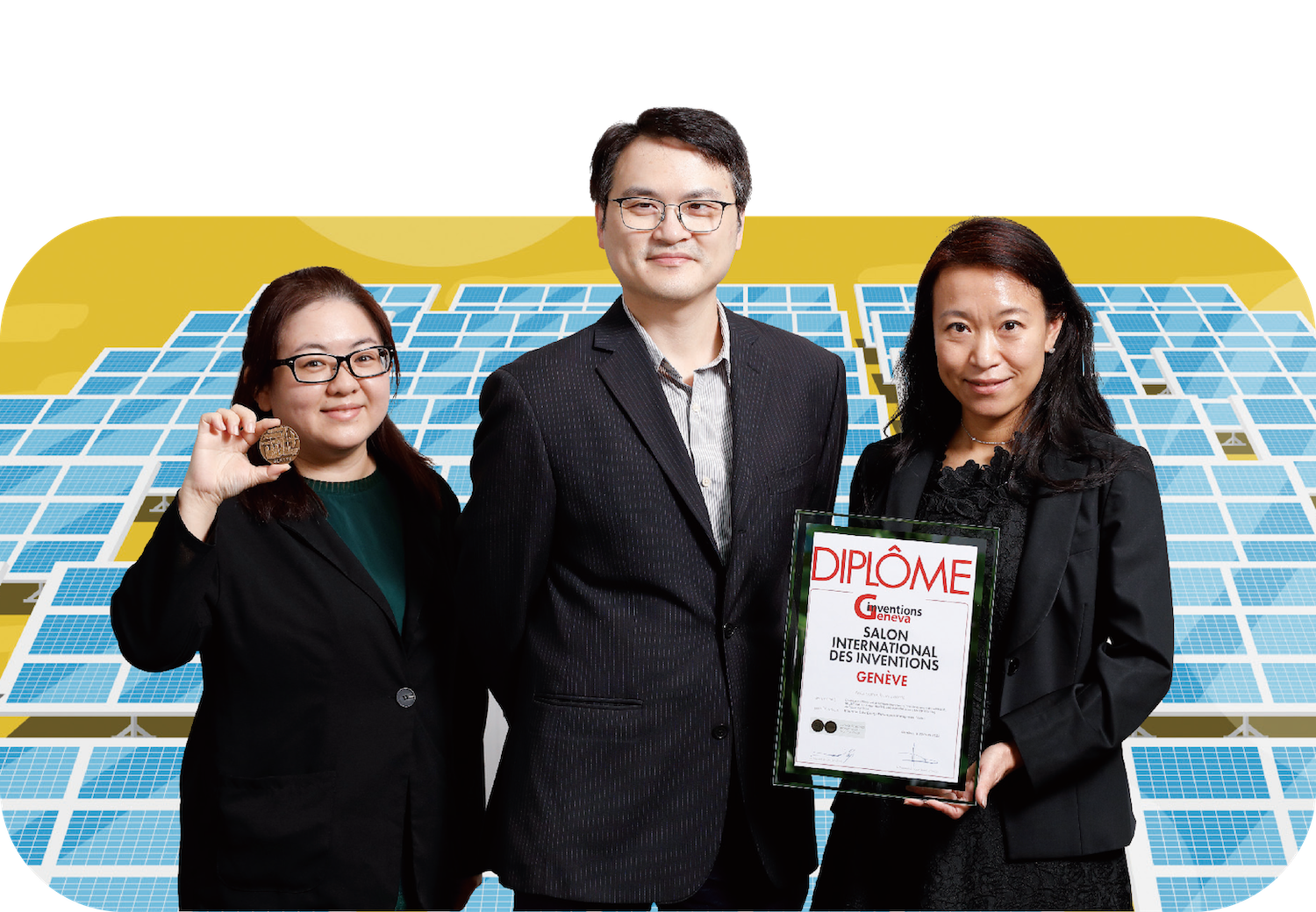


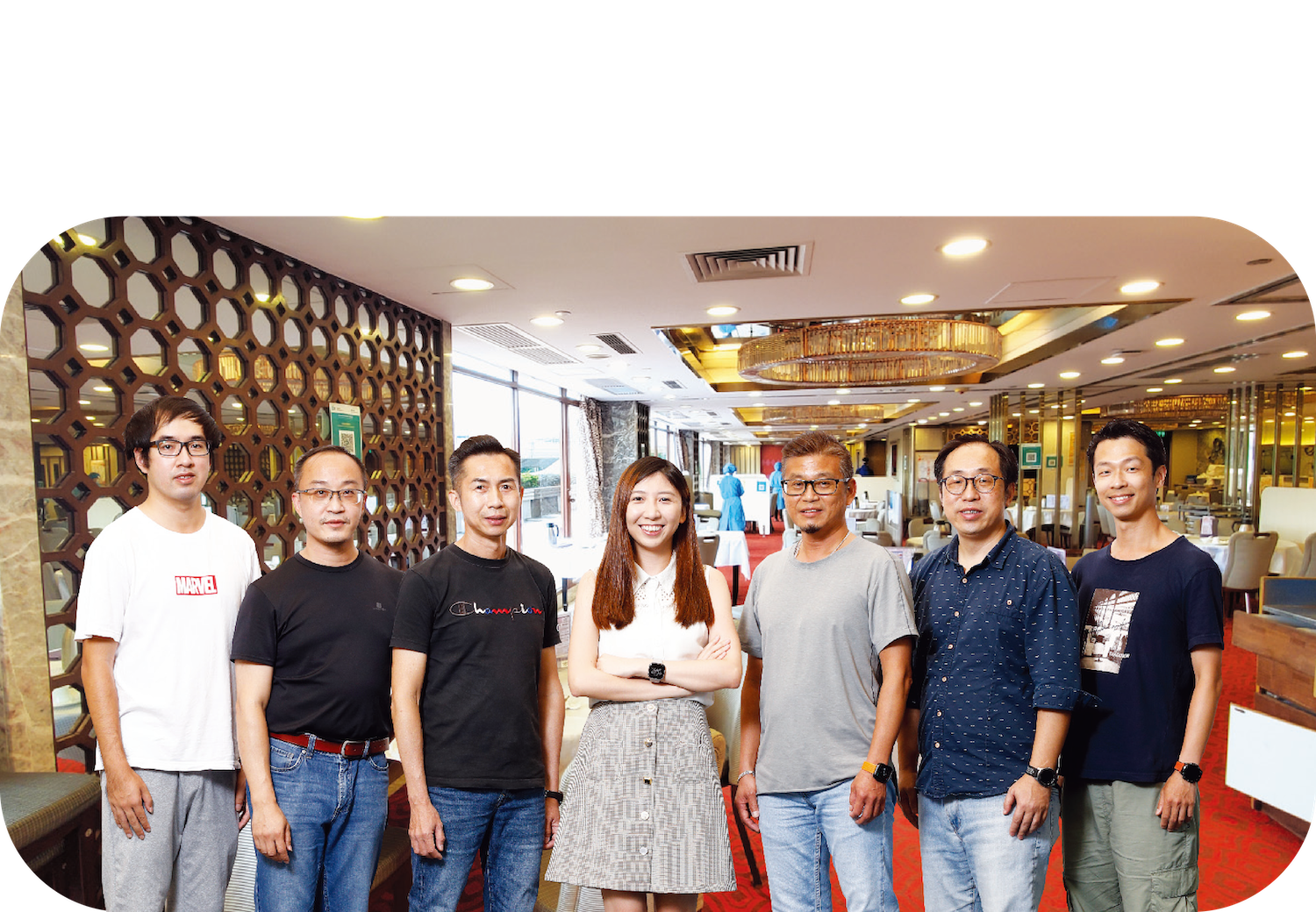
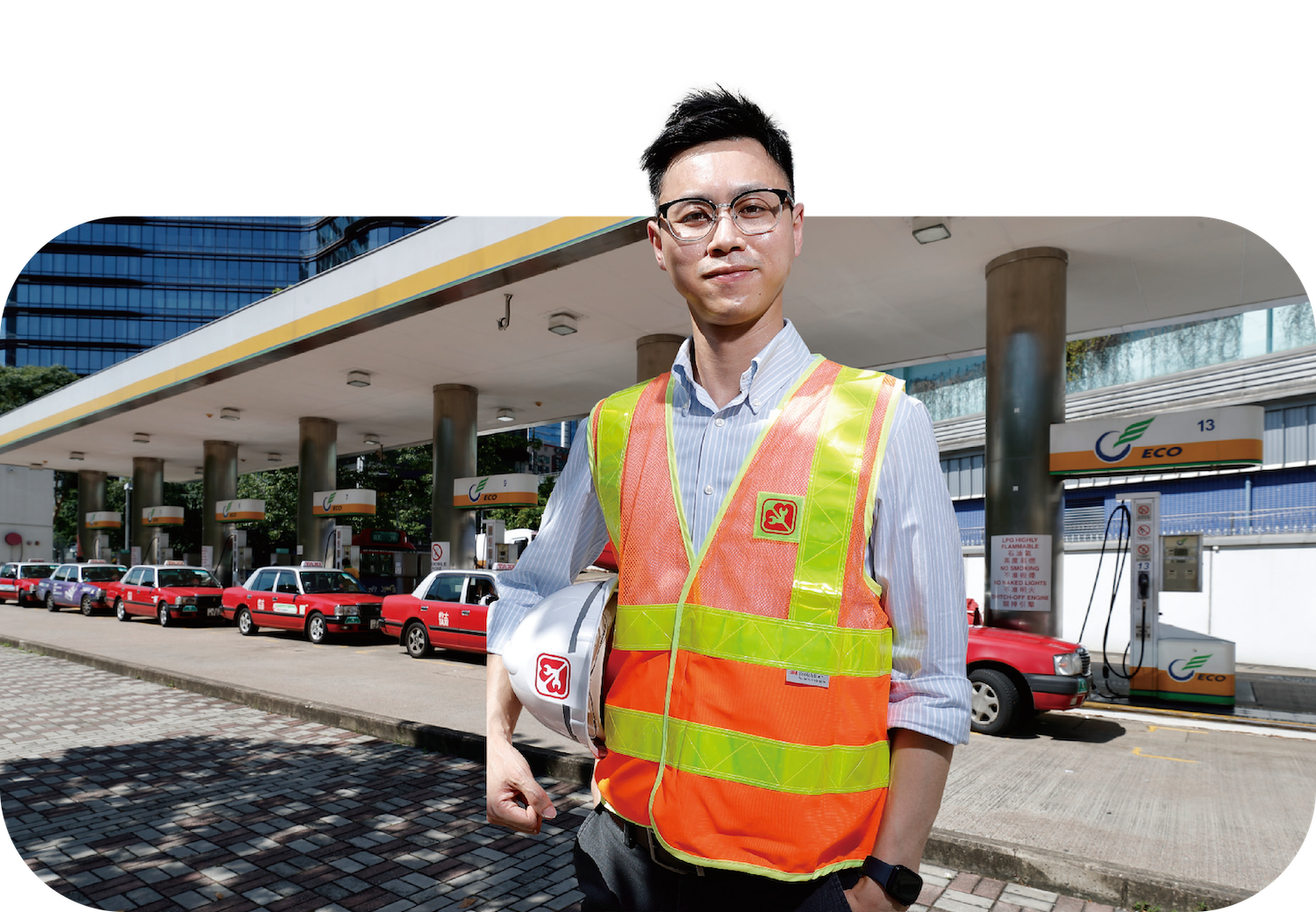




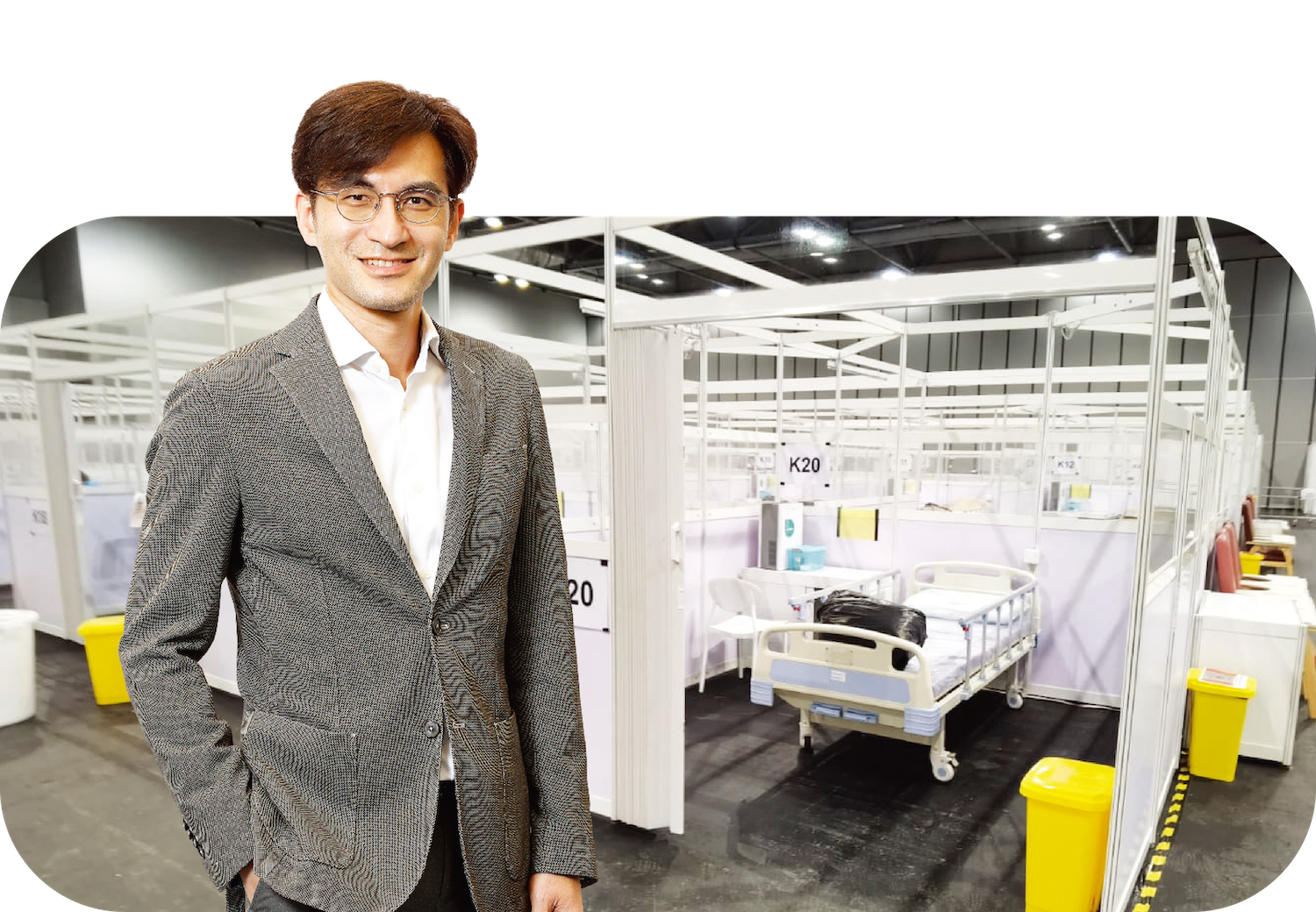
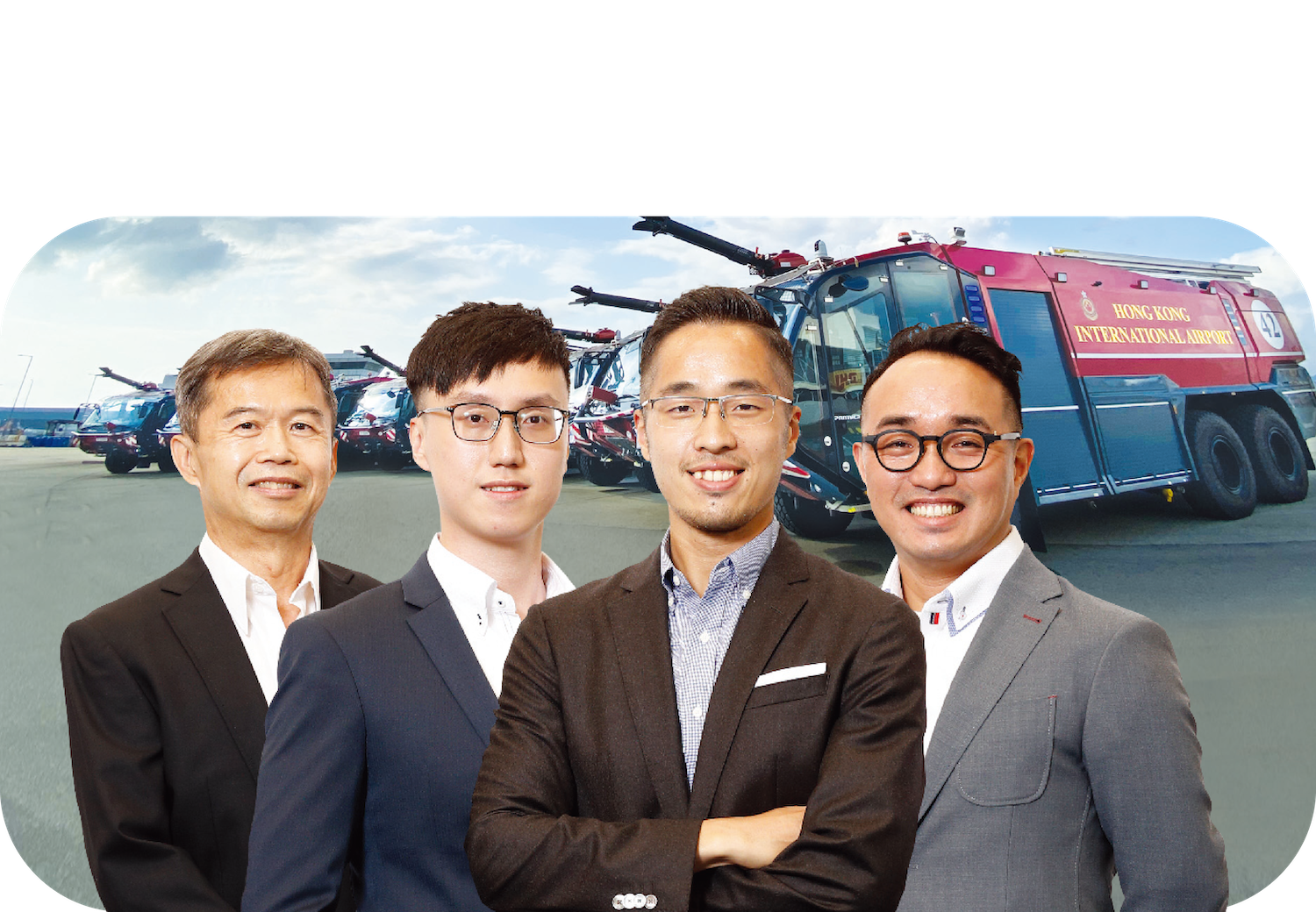

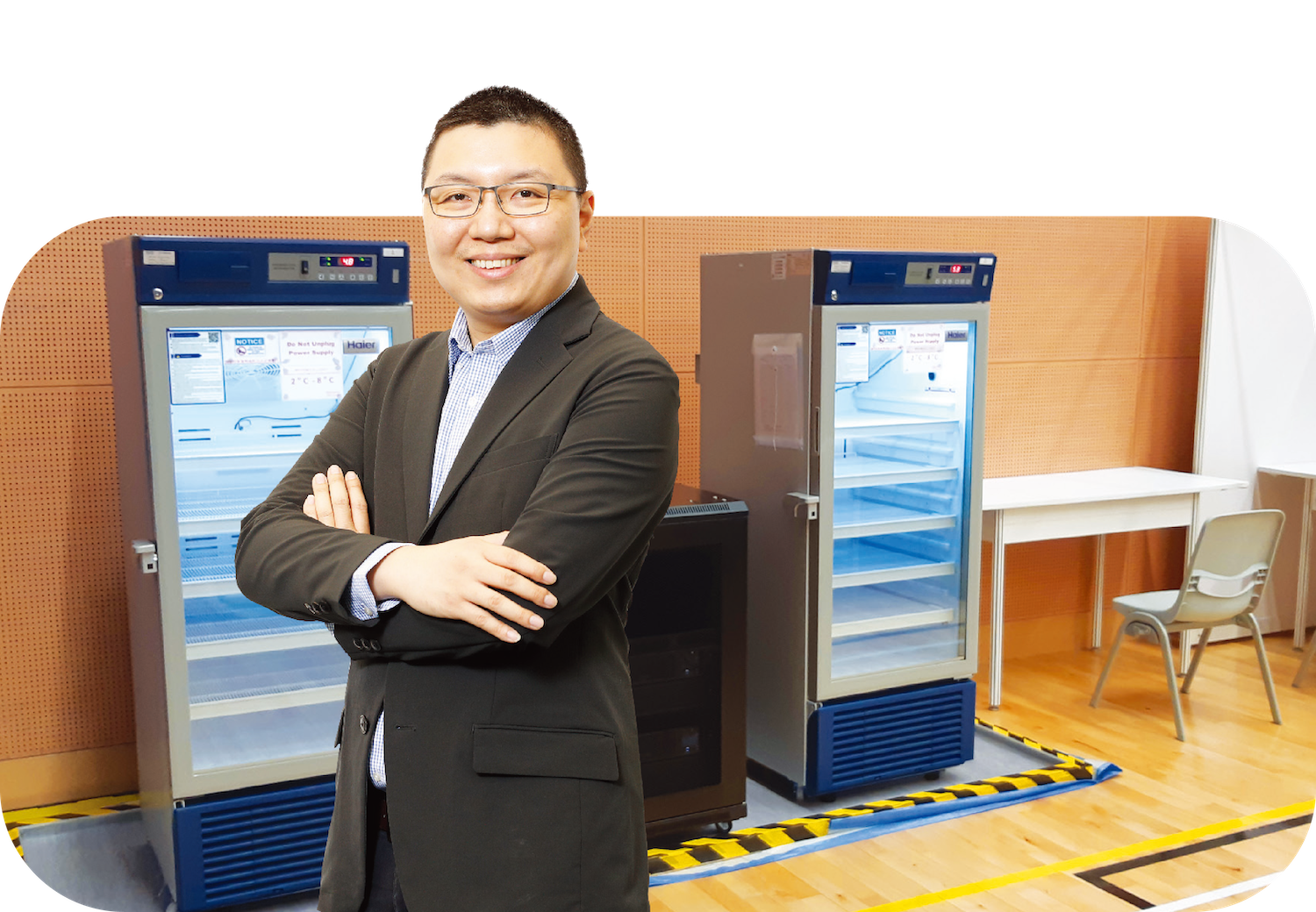
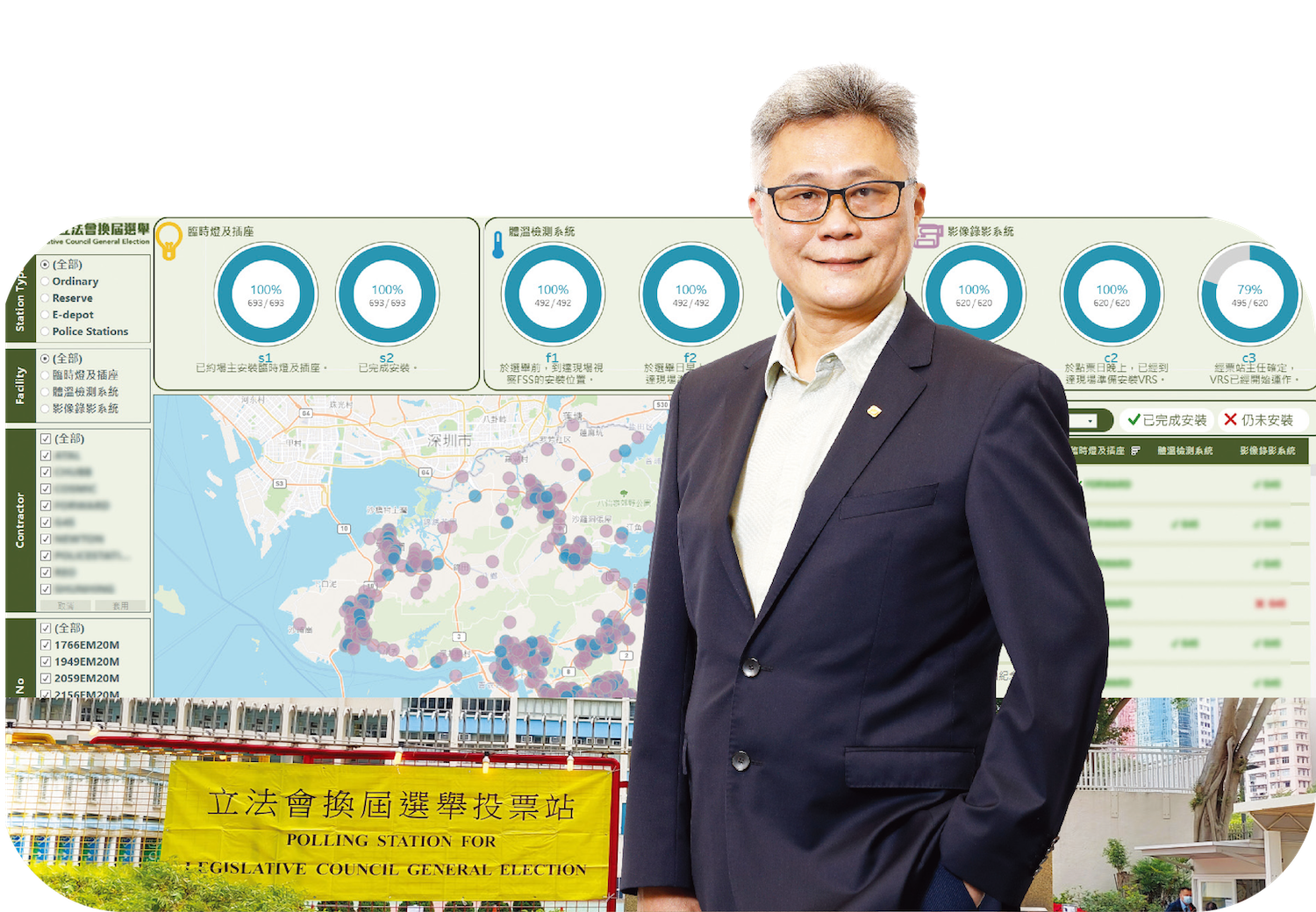
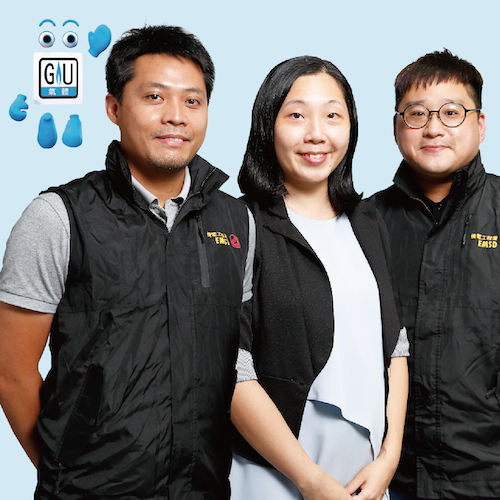
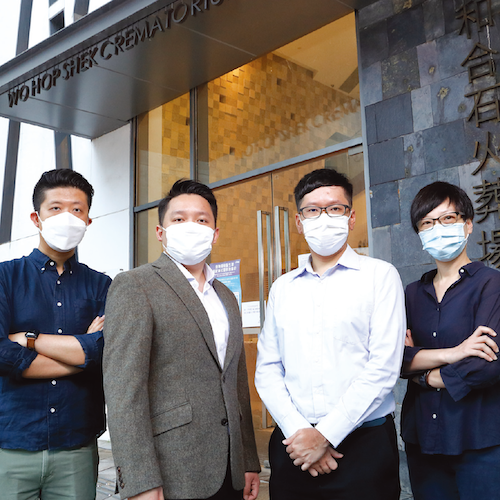
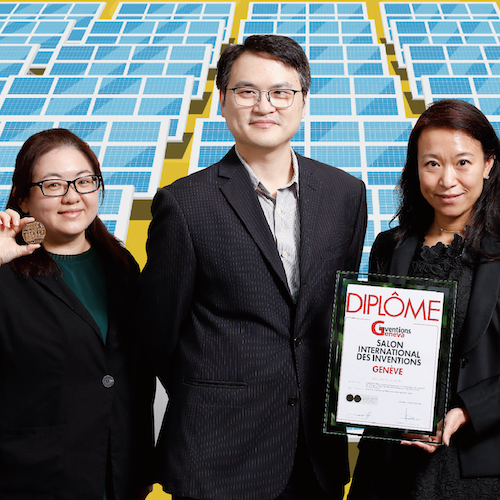
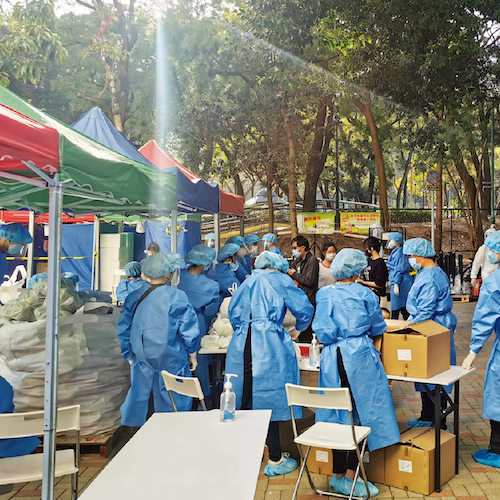
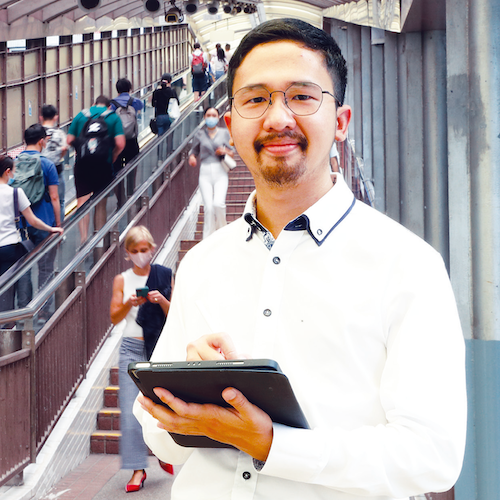

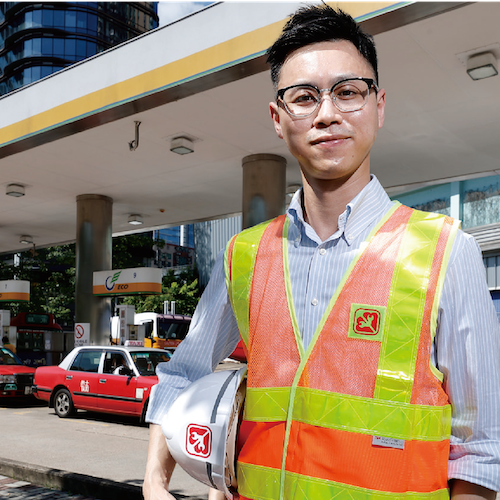
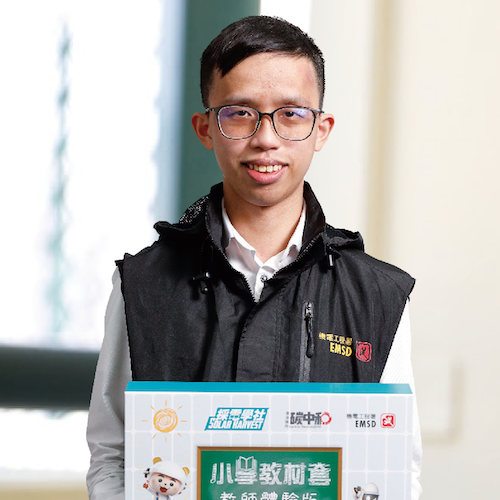


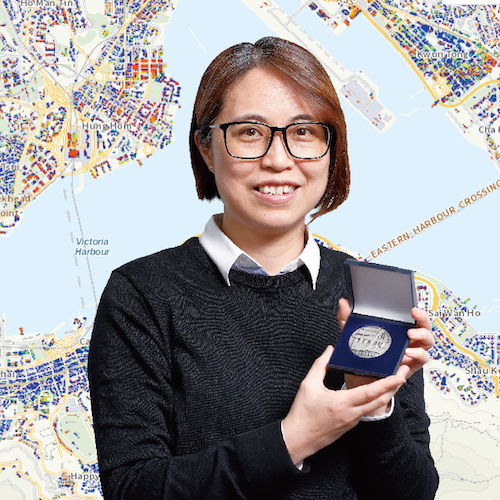


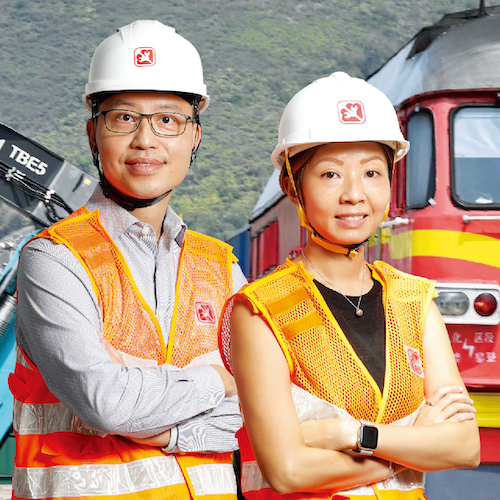

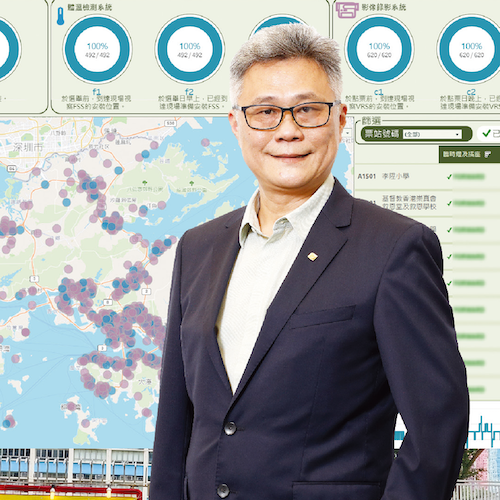
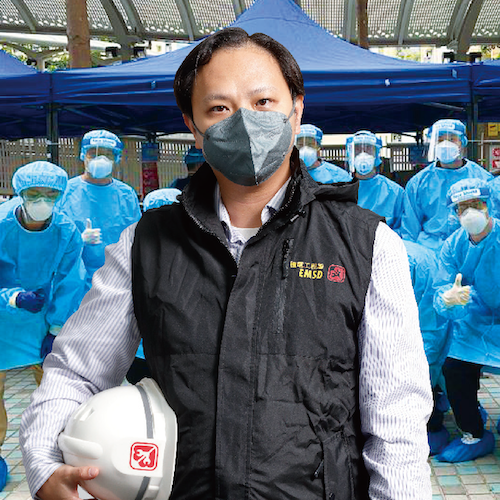
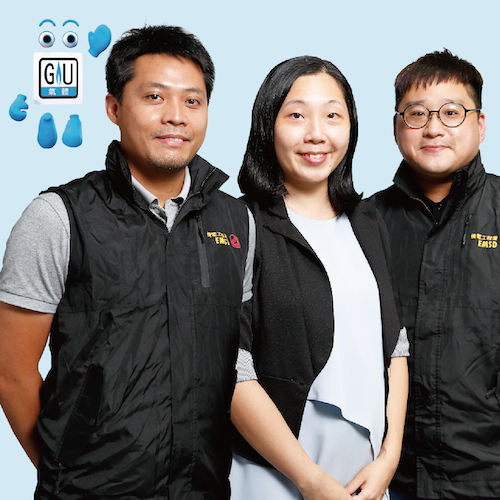
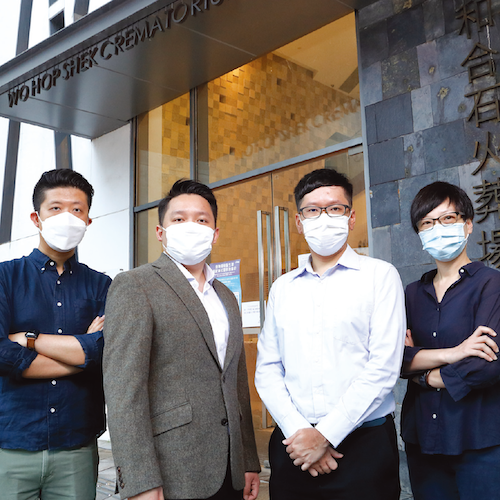
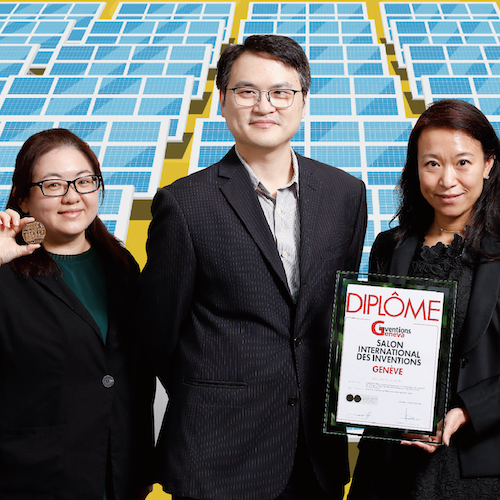
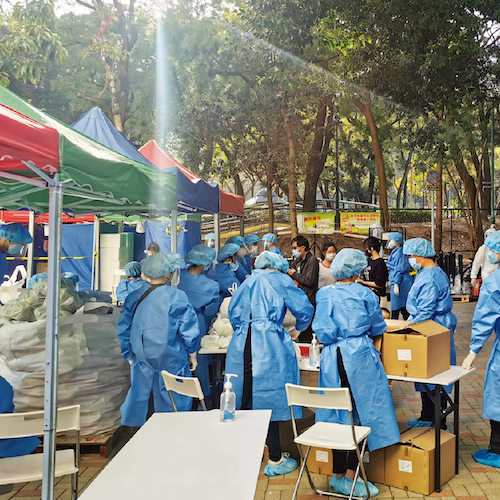
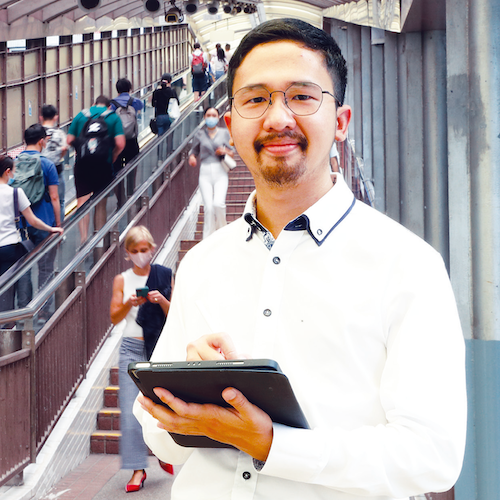

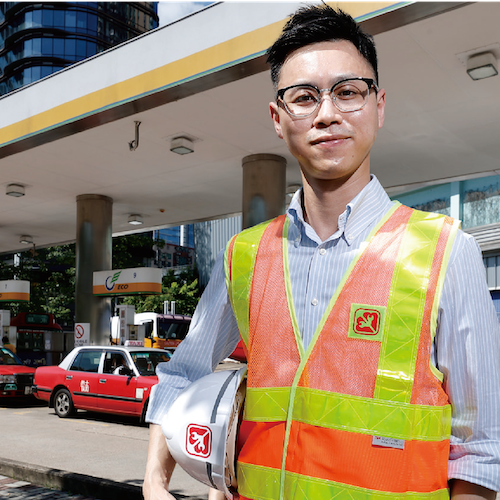
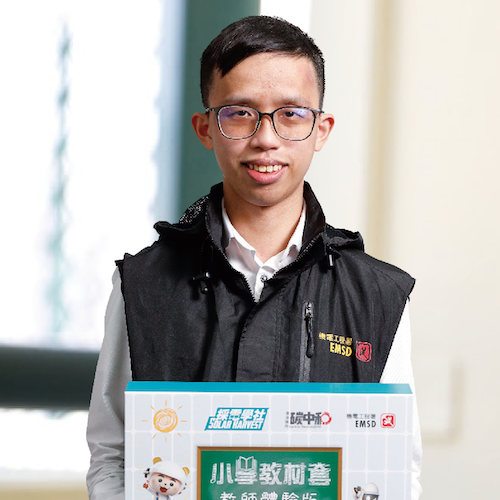


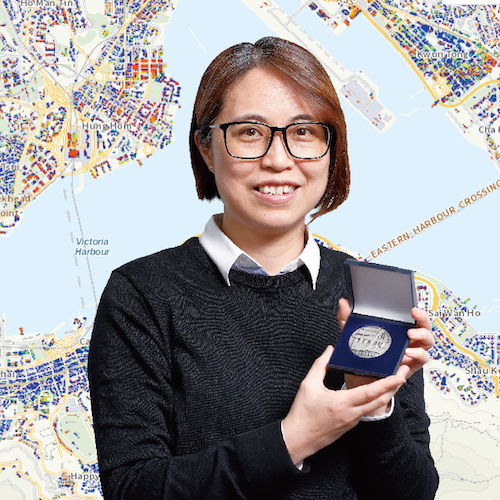


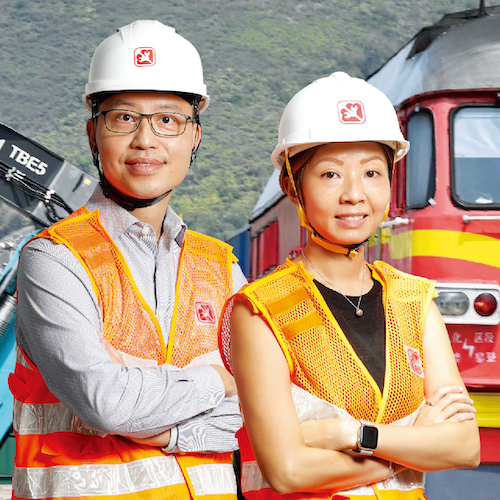

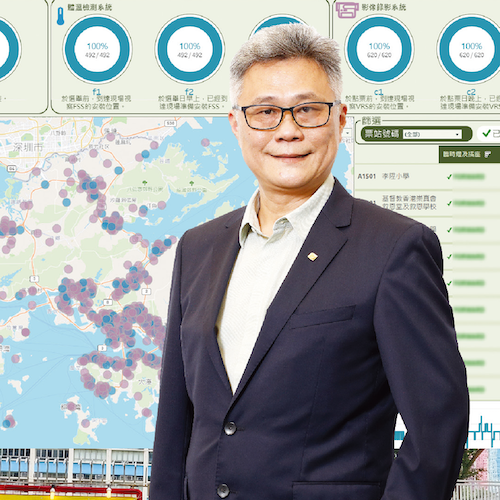
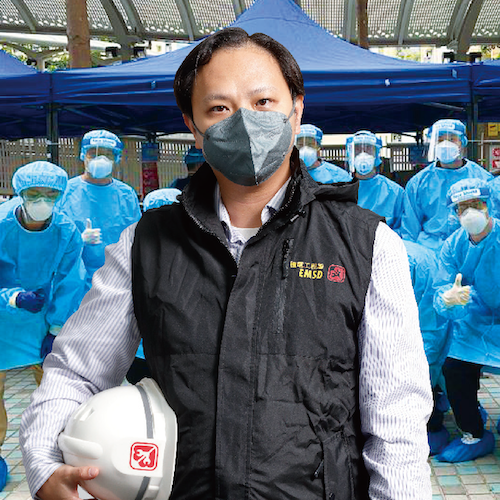
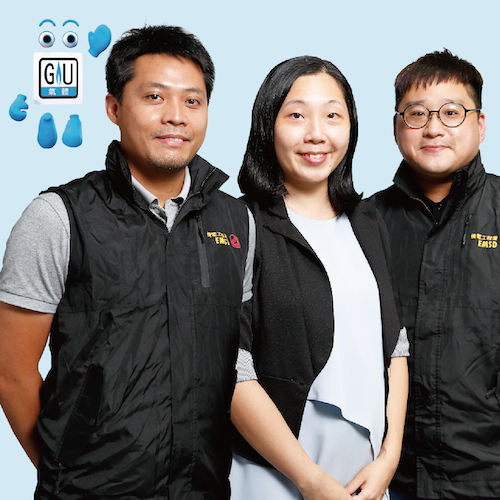
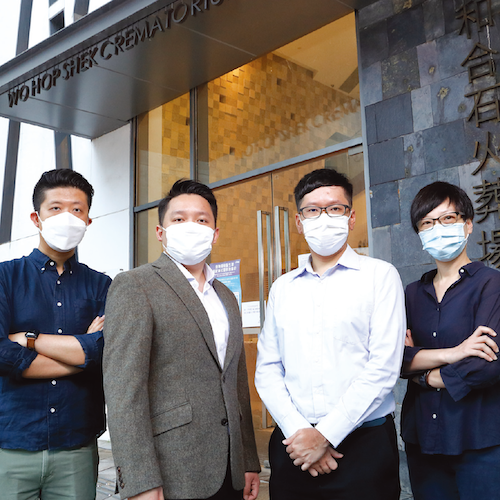
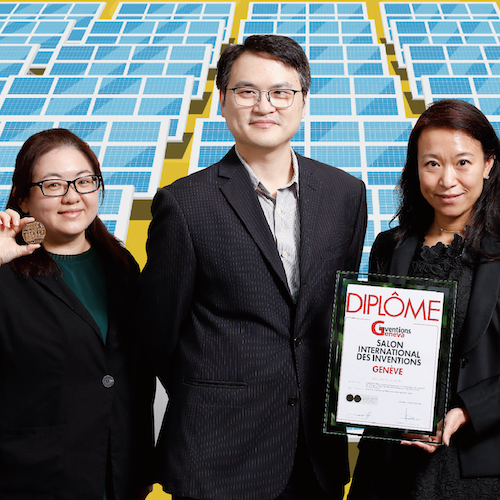
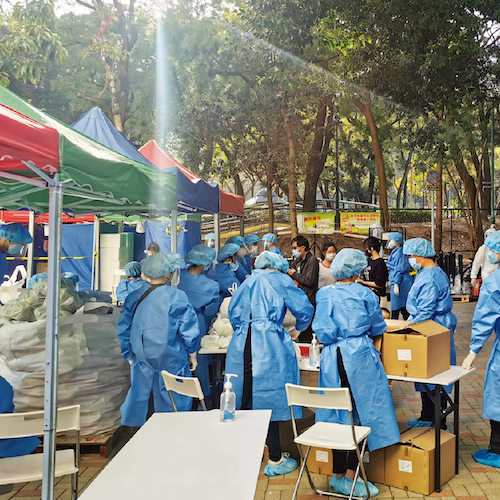
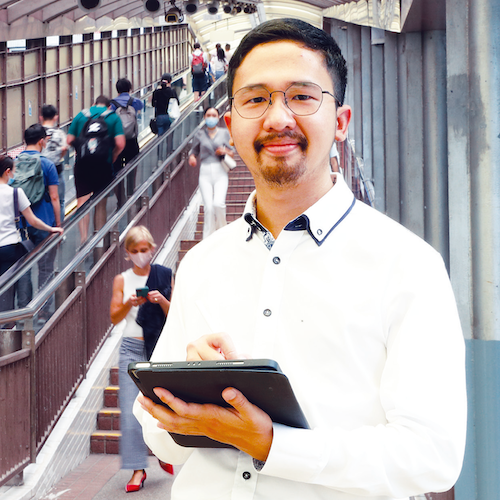

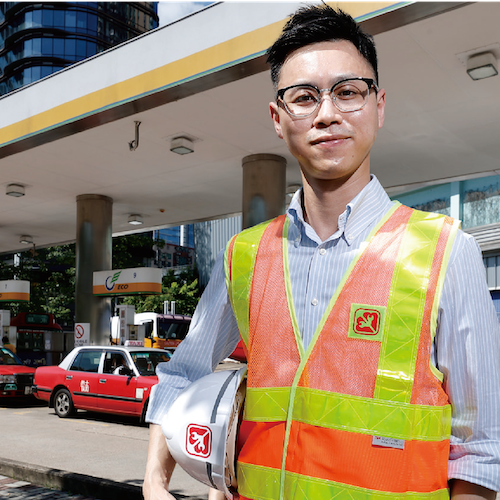
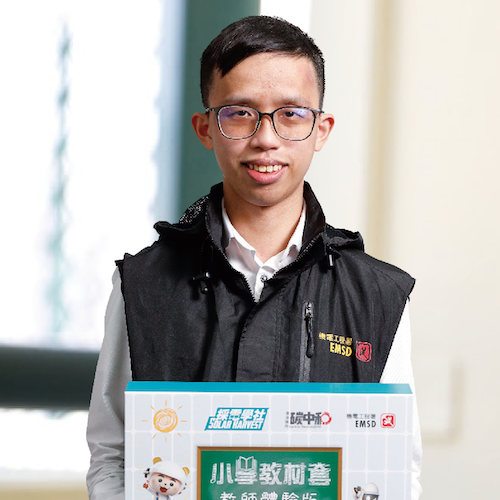


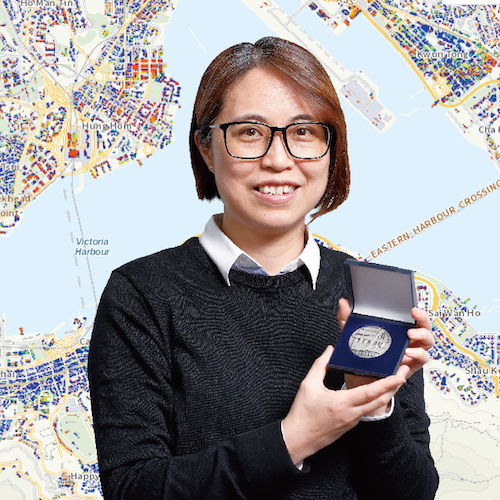


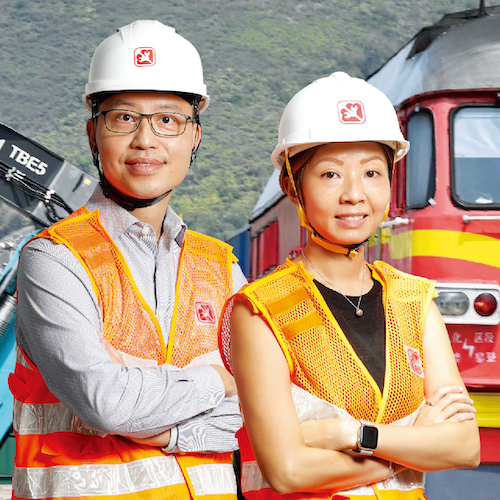

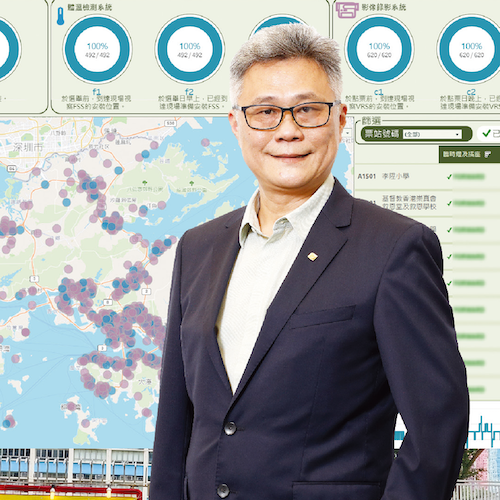
Leveraging Digital Tools to Support the LegCo Election
Mr Yuen Wai-yip, Lobee, a senior engineer, led his team members to deploy new innovation and technology tools in the 2021 Legislative Council (LegCo) General Election to enhance work efficiency and effectiveness. Despite the immense pressure, they devoted their best efforts and completed all the tasks on time, contributing to the smooth running of the election.
The EMSTF has always provided E&M support to LegCo elections, for example, through the provision of electricity and lighting at polling stations. The latest LegCo General Election held on 19 December 2021 was no exception. Mr Yuen Wai-yip, Lobee, a senior engineer of the General Engineering Services Division (GESD), led his team to provide relevant support to the Registration and Electoral Office (REO) and opened up a new digital era for holding elections in Hong Kong.
Preparations for the 2021 LegCo General Election began soon after the District Council election in 2019. The efforts were translated into several “firsts” in this LegCo election, including the first-ever use of an Electronic Poll Register System to issue ballot papers at 693 polling stations and the adoption of a video recording system to monitor the counting process from 11:00 p.m., when 620 polling stations were converted to counting stations. We also rolled out a GESD-developed dashboard at the Emergency Response Centre in our headquarters for round-the-clock monitoring for the election from 18 to 20 December.
The dashboard was particularly effective in monitoring the works of contractors in the run-up to the election day. As each contractor was required to report the progress of their designated tasks via mobile devices, the dashboard was continually updated, giving Mr Yuen and his team access to a real-time overview of the progress of works at all polling stations as displayed on an interactive map of Hong Kong. The system also enabled them to readily retrieve the information of the responsibilities of contractors and their contact details for prompt follow-up. Given the large number of polling stations and contractors, this timely and efficient oversight was not possible in the past when progress updates solely relied on telephone calls.
Speaking of the challenges which the team faced, Mr Yuen cited the short period of time allowed to set up the video recording system for monitoring the counting process. “As the polling stations closed at 10:30 p.m., we only had 30 minutes to set up the device, so that video recording could begin at 11:00 p.m. sharp when the counting process commenced,” he said.
Mr Yuen attributed the team’s success to its rich work experience accumulated from previous elections and strong support from the senior management, as well as over 1600 colleagues from various divisions of the EMSD who rendered assistance on the election day. “The REO was most impressed with the dashboard, which we plan to deploy with other innovation and technology tools in the District Council election in 2023 and the next LegCo election in 2025 after further refinement,” he said.
Preparations for the 2021 LegCo General Election began soon after the District Council election in 2019. The efforts were translated into several “firsts” in this LegCo election, including the first-ever use of an Electronic Poll Register System to issue ballot papers at 693 polling stations and the adoption of a video recording system to monitor the counting process from 11:00 p.m., when 620 polling stations were converted to counting stations. We also rolled out a GESD-developed dashboard at the Emergency Response Centre in our headquarters for round-the-clock monitoring for the election from 18 to 20 December.
The dashboard was particularly effective in monitoring the works of contractors in the run-up to the election day. As each contractor was required to report the progress of their designated tasks via mobile devices, the dashboard was continually updated, giving Mr Yuen and his team access to a real-time overview of the progress of works at all polling stations as displayed on an interactive map of Hong Kong. The system also enabled them to readily retrieve the information of the responsibilities of contractors and their contact details for prompt follow-up. Given the large number of polling stations and contractors, this timely and efficient oversight was not possible in the past when progress updates solely relied on telephone calls.
Speaking of the challenges which the team faced, Mr Yuen cited the short period of time allowed to set up the video recording system for monitoring the counting process. “As the polling stations closed at 10:30 p.m., we only had 30 minutes to set up the device, so that video recording could begin at 11:00 p.m. sharp when the counting process commenced,” he said.
Mr Yuen attributed the team’s success to its rich work experience accumulated from previous elections and strong support from the senior management, as well as over 1600 colleagues from various divisions of the EMSD who rendered assistance on the election day. “The REO was most impressed with the dashboard, which we plan to deploy with other innovation and technology tools in the District Council election in 2023 and the next LegCo election in 2025 after further refinement,” he said.
Pulling Together to Support the Fight against the Fifth Wave of the Epidemic
With the outbreak of the serious fifth wave of the epidemic in early 2022, the fight against the virus was a race against time. Civil servants were mobilised to take up important tasks such as supporting the community and participating in “restriction-testing declaration” (RTD) operations. Mr Chan Chi-wai, a senior engineer of the General Legislation Division, took up the role of coordinating members from different divisions and sections under the Regulatory Services of the EMSD to participate in the anti-epidemic efforts on the frontline.
At the onset of the fifth wave of the epidemic, residents of Kwai Chung Estate were mandated to stay at home. The first major task of the EMSD’s anti-epidemic team was to deliver three meals a day to the residents in one of the 40-storey blocks of the estate. Despite the very limited time for us to prepare for this urgent operation, our colleagues completed the task successfully by promptly arranging a team of about 50 members to deliver three meals to the residents every day during the mandated period.
“Everyone was surely concerned about their own safety in the face of the rapid development of the fifth wave of the epidemic that time. However, as civil servants, we were determined to stay on the frontline to deliver hot meals to the residents. Though we do not have any direct contact with the residents, some of them posted thank-you notes outside their doors to express their gratitude, which means so much to us,” Mr Chan said.
As the epidemic continued to rage on, the EMSD team actively participated in various anti-epidemic tasks, of which the RTD operations were the most challenging. At the peak of the epidemic, a number of teams of civil servants were required to conduct these operations every day. On average, the EMSD had to arrange a team of more than 150 colleagues to join the RTD operations every week. Participating colleagues were of different ranks and posts under the Regulatory Services and the Electrical and Mechanical Services Trading Fund. Whether they were administrative staff, inspectors or engineers, they became close comrades in these anti-epidemic operations.
“In those days, we often heard colleagues recounting stories about their anti-epidemic work on the hallways in the EMSD Headquarters. Some talked about the difficulties they faced and their hope for the epidemic to die down as soon as possible. We all understood that as part of the anti-epidemic force, we had to remain resilient and committed despite all the challenges and immense pressure ahead.”
“Every operation was very urgent in time and large in scale, involving a number of government departments,” Mr Chan said when he talked about the difficulties in the anti-epidemic work. “We had to arrange for supplies and mobilise manpower within a short period of time. And we could only rely on social media apps to stay connected and complete every operation, in which we would invariably end up with sweat-soaked clothing under the protective gear. As every operation was different and there was no past experience for reference, we had to play by ear and stay vigilant. After each operation, we all enthusiastically shared experience to help improve the efficiency and efficacy of our anti-epidemic work in the future, and to minimise the risk of infection for our colleagues and the impact of such work on the general public.”
“Everyone was surely concerned about their own safety in the face of the rapid development of the fifth wave of the epidemic that time. However, as civil servants, we were determined to stay on the frontline to deliver hot meals to the residents. Though we do not have any direct contact with the residents, some of them posted thank-you notes outside their doors to express their gratitude, which means so much to us,” Mr Chan said.
As the epidemic continued to rage on, the EMSD team actively participated in various anti-epidemic tasks, of which the RTD operations were the most challenging. At the peak of the epidemic, a number of teams of civil servants were required to conduct these operations every day. On average, the EMSD had to arrange a team of more than 150 colleagues to join the RTD operations every week. Participating colleagues were of different ranks and posts under the Regulatory Services and the Electrical and Mechanical Services Trading Fund. Whether they were administrative staff, inspectors or engineers, they became close comrades in these anti-epidemic operations.
“In those days, we often heard colleagues recounting stories about their anti-epidemic work on the hallways in the EMSD Headquarters. Some talked about the difficulties they faced and their hope for the epidemic to die down as soon as possible. We all understood that as part of the anti-epidemic force, we had to remain resilient and committed despite all the challenges and immense pressure ahead.”
“Every operation was very urgent in time and large in scale, involving a number of government departments,” Mr Chan said when he talked about the difficulties in the anti-epidemic work. “We had to arrange for supplies and mobilise manpower within a short period of time. And we could only rely on social media apps to stay connected and complete every operation, in which we would invariably end up with sweat-soaked clothing under the protective gear. As every operation was different and there was no past experience for reference, we had to play by ear and stay vigilant. After each operation, we all enthusiastically shared experience to help improve the efficiency and efficacy of our anti-epidemic work in the future, and to minimise the risk of infection for our colleagues and the impact of such work on the general public.”
Telling Compelling Stories about Gas Safety in Creative Ways
In recent years, we have continued to take forward public education on gas safety by diversified new approaches. In addition to creative and vivid animations and four-panel comic strips for publicity, we have made extensive use of social media platforms to engage the public, and translated the gas safety messages for various ethnic groups in Hong Kong. Ms Chan Wai-sheung, Michelle, an engineer of the Gas Standards Office, is our behind-the-scene “Creative Director” for all these publicity initiatives. She told us that more novel promotions would be coming soon.
As the opportunity for face-to-face contact with the public through visits and outreach programmes was greatly reduced during the epidemic, Ms Chan and her team stepped up their efforts in exploring publicity approaches other than the traditional means and channels, such as more extensive use of creative productions, social media platforms and STEM education to engage people from all walks of life.
Taking forward the new initiatives was not plain sailing, she said, “As ethnic groups in society have always been one of our targets for promotion and education, we have translated the messages on gas safety into various ethnic languages for dissemination to them clearly through online platforms and dedicated radio channels. However, as none of our team members knew the languages of ethnic minorities, the biggest challenge we have faced was how to ensure that the translated messages to be delivered to different ethnic groups were accurate.”
To ensure the translated message was concise and closer to the dialects of these target audiences, the team contacted and visited the consulates of ethnic groups for assistance. The consulate staff were very helpful and worked with our team members to revise the translated texts to ensure that the gas safety messages were clear and engaging.
Keeping up their good efforts, the team is embarking on a new series of innovative outreach programmes, such as interactive storytelling theatres and activities, to extend the promotion of gas safety messages to students and foreign domestic helpers. The team also collaborates with support service centres for ethnic minorities to work out promotion programmes in different forms for engaging more ethnic groups.
Ms Chan said, “We have made use of the subsidies granted under the Job Creation Scheme to recruit young people for the preparation work of the outreach programmes, such as compiling the drama scripts and preparing the materials required for theatrical production. Our team and other colleagues will perform on stage to tell a compelling story about gas safety. We hope that students, foreign domestic helpers and ethnic groups will become the ‘seeds’ for disseminating gas safety messages to their family members, friends and employers.”
Taking forward the new initiatives was not plain sailing, she said, “As ethnic groups in society have always been one of our targets for promotion and education, we have translated the messages on gas safety into various ethnic languages for dissemination to them clearly through online platforms and dedicated radio channels. However, as none of our team members knew the languages of ethnic minorities, the biggest challenge we have faced was how to ensure that the translated messages to be delivered to different ethnic groups were accurate.”
To ensure the translated message was concise and closer to the dialects of these target audiences, the team contacted and visited the consulates of ethnic groups for assistance. The consulate staff were very helpful and worked with our team members to revise the translated texts to ensure that the gas safety messages were clear and engaging.
Keeping up their good efforts, the team is embarking on a new series of innovative outreach programmes, such as interactive storytelling theatres and activities, to extend the promotion of gas safety messages to students and foreign domestic helpers. The team also collaborates with support service centres for ethnic minorities to work out promotion programmes in different forms for engaging more ethnic groups.
Ms Chan said, “We have made use of the subsidies granted under the Job Creation Scheme to recruit young people for the preparation work of the outreach programmes, such as compiling the drama scripts and preparing the materials required for theatrical production. Our team and other colleagues will perform on stage to tell a compelling story about gas safety. We hope that students, foreign domestic helpers and ethnic groups will become the ‘seeds’ for disseminating gas safety messages to their family members, friends and employers.”
When AI Meets Cremation: A Drive for Taking the Industry Forward
Mr Cheung Lap-hung (2nd left), an engineer, Mr Fung Chun-kwok (2nd right), an assistant engineer and the team have developed an award-winning artificial intelligence (AI) Based Image Analytic and Control System for Cremation Process which uses image analytics and AI technology to optimise each cremation session, thus reducing the time required and fuel consumption.
While digitalisation and AI have brought transformational changes in many industries, it remains challenging for the cremation trade to adopt the two since cremation is a traditional business and perceived by some as a taboo subject. Even so, Mr Cheung Lap-hung, an engineer of the Municipal Sector Division, believes that digitalisation is the right path for cremation services because it not only enhances the work efficiency but also releases staff to take on emergency repairs and maintenance, putting their expertise to better use.
He, therefore, has put forward a solution called the AI Based Image Analytic and Control System for Cremation Process or i-Cremation, which won a silver medal at the International Exhibition of Inventions of Geneva 2022.
“We must thank our client the Food and Environmental Hygiene Department and our frontline staff for their support throughout the development process,” Mr Cheung said. The system is being piloted at six cremators at the Wo Hop Shek Crematorium and scheduled to be launched officially by the end of 2023.
Training the AI model is the key. It is also the most time-consuming and costly part of the deployment process. Apart from installing a video camera in each cremator to capture sufficient operational data and cremation status for image analytics, experienced frontline staff must also observe the entire cremation process, which takes about two hours, and provide feedbacks to continuously improve the performance and stability of the AI model. This “training” process has been repeated many times to enhance the AI in the development.
“To enhance staff confidence, we set up a dashboard showing the various real-time operational parameters of i-Cremation in action. Our staff can see for themselves how the AI system simulates and controls all four stages of the cremation process,” he explained. The dashboard has boosted staff confidence as it shows vividly that AI can do the job competently. Furthermore, if anything goes wrong, staff can intervene anytime, demonstrating that human operators still can add value to the cremation work. The team is working on a 2.0 version of the patented i-Cremation, which may be deployed at other crematoria in future.
“We are very delighted to see the changes of this traditional industry by adopting new technologies and innovative ideas,” Mr Cheung concluded. During the development of our project, one of the existing German manufacturers has seen the potential benefit of AI application and has already made an important change in their original cremator design to add video cameras as a standard feature in new projects.
He, therefore, has put forward a solution called the AI Based Image Analytic and Control System for Cremation Process or i-Cremation, which won a silver medal at the International Exhibition of Inventions of Geneva 2022.
“We must thank our client the Food and Environmental Hygiene Department and our frontline staff for their support throughout the development process,” Mr Cheung said. The system is being piloted at six cremators at the Wo Hop Shek Crematorium and scheduled to be launched officially by the end of 2023.
Training the AI model is the key. It is also the most time-consuming and costly part of the deployment process. Apart from installing a video camera in each cremator to capture sufficient operational data and cremation status for image analytics, experienced frontline staff must also observe the entire cremation process, which takes about two hours, and provide feedbacks to continuously improve the performance and stability of the AI model. This “training” process has been repeated many times to enhance the AI in the development.
“To enhance staff confidence, we set up a dashboard showing the various real-time operational parameters of i-Cremation in action. Our staff can see for themselves how the AI system simulates and controls all four stages of the cremation process,” he explained. The dashboard has boosted staff confidence as it shows vividly that AI can do the job competently. Furthermore, if anything goes wrong, staff can intervene anytime, demonstrating that human operators still can add value to the cremation work. The team is working on a 2.0 version of the patented i-Cremation, which may be deployed at other crematoria in future.
“We are very delighted to see the changes of this traditional industry by adopting new technologies and innovative ideas,” Mr Cheung concluded. During the development of our project, one of the existing German manufacturers has seen the potential benefit of AI application and has already made an important change in their original cremator design to add video cameras as a standard feature in new projects.
Developing an I&T Solution for Maximising Performance of Solar PV Systems
Ms Cheung Man-chit, Jovian, a senior engineer of the Energy Efficiency Office, previously discovered that no device on the market could objectively and scientifically measure the power generation performance of a solar photovoltaic (PV) system. Therefore, she took the lead in developing the Integrated Solar Energy Performance Management Toolkit.
Ms Cheung collaborated with the Hong Kong Polytechnic University to develop the novel Integrated Solar Energy Performance Management Toolkit (iSMS). Leveraging artificial intelligence and digital twin technology while making reference to the performance of nearby solar PV systems, the iSMS estimates the power generation performance of solar PV systems and predicts the timing of necessary system maintenance.
The iSMS measures factors affecting the power generation performance, such as the coverage of shading, dust and bird excrement on a solar panel. Based on the data, the iSMS reminds owners of solar energy generating facilities to clean the solar PV panels in order to harness more solar energy and maximise power generation performance, so that the maximum Feed-in Tariff (FiT) income of the facilities’ owners will be secured.
When the iSMS detects that a facility is due for repair or maintenance, it will issue an alert and recommend the timing for preventive maintenance. This function is particularly useful for monitoring facilities at hard-to-reach places, such as floating photovoltaic panels.
“To address climate change, the Government encourages the public to install solar PV systems. If solar PV systems can maintain optimal performance and deliver a better FiT return to facilities’ owners, the public will respond more positively to such renewable energy projects. Ultimately, it will help Hong Kong achieve the target of carbon neutrality,” Ms Cheung said.
The iSMS is now patented in Hong Kong and have won a bronze medal in the International Exhibition of Inventions of Geneva 2022, exemplifying the recognition for our I&T achievements.
The iSMS measures factors affecting the power generation performance, such as the coverage of shading, dust and bird excrement on a solar panel. Based on the data, the iSMS reminds owners of solar energy generating facilities to clean the solar PV panels in order to harness more solar energy and maximise power generation performance, so that the maximum Feed-in Tariff (FiT) income of the facilities’ owners will be secured.
When the iSMS detects that a facility is due for repair or maintenance, it will issue an alert and recommend the timing for preventive maintenance. This function is particularly useful for monitoring facilities at hard-to-reach places, such as floating photovoltaic panels.
“To address climate change, the Government encourages the public to install solar PV systems. If solar PV systems can maintain optimal performance and deliver a better FiT return to facilities’ owners, the public will respond more positively to such renewable energy projects. Ultimately, it will help Hong Kong achieve the target of carbon neutrality,” Ms Cheung said.
The iSMS is now patented in Hong Kong and have won a bronze medal in the International Exhibition of Inventions of Geneva 2022, exemplifying the recognition for our I&T achievements.
Supporting RTD Operations with Heart and Technologies
In March 2022, the EMSD co-ordinated and led "restriction-testing declaration" (RTD) operations, which entailed overall planning and co-ordination, information technology system support and logistics management. Thanks to the staunch support and high esprit de corps displayed by our Digitalisation and Technology Division, Corporate Services Division and other divisions, as well as various government departments, these joint operations were carried out smoothly.
Early 2022 was memorable for many EMSTF colleagues who participated in the “restriction-testing declaration” (RTD) operations, an important element of Hong Kong’s fight against the epidemic. Among the participants were Mr Lai Chun-fai, Alex and Mr Chan Sze-nok, Donald, both senior engineers of the Digitalisation and Technology Division (DTD), and Ms Ng Ka-pik, Cindy, the chief supplies officer of the Supplies Sub-division.
As only a few days’ notice was given to the team for its first-ever RTD operation conducted at Tak Ying House in Tak Long Estate on 3 and 4 March, Ms Ng had to race against time to procure adequate supplies within a very short period of time. These included personal protective equipment and rapid antigen test kits for colleagues, as well as Chinese medicine packs and canned food for households in the target building. “We always keep two sets of supplies, one for the immediate RTD operation and the other as stand-by for the next one,” Ms Ng explained.
Mr Lai and Mr Chan recalled their key tasks in the operation. “On Day One, we knocked on the door of each household to inform the residents to go downstairs for nucleic acid tests; on Day Two, we called those who tested positive by phone for follow-up, checked whether the residents had already obtained a negative test result before allowing them to leave the restricted area, and re-opened the restricted area by noon finally.” Many challenges arose in the operation, one of them was data mapping. The testing contractor only had the identity card, mobile phone and reference numbers of those being tested, but did not have the crucial information such as to which households they belonged, thus making it difficult for the responsible colleagues to follow up on the positive cases. Fortunately, the team was able to draw on the rich information technology (IT) expertise of the EMSD to promptly complete the data mapping, so that follow-up action could be carried out smoothly.
“Given the complex and mammoth operation, and the need to work with unfamiliar staff from different departments, we are glad that working with high team spirit, we got all the difficult tasks done,” Mr Chan said.
“We are grateful that our colleagues were so accommodating and that the residents were supportive of our work,” Mr Lai added.
Mr Lee Che-kit, the chief engineer of the DTD, led the RTD operation at Yau Oi Estate on 9 and 10 March as the deputy field-commander. “In this operation, we alerted the testing contractor that the information they obtained from the residents was insufficient for following up on the positive cases,” he said. The insight prompted the contractor to obtain more information required from the residents, making subsequent RTD operations more efficient.
As only a few days’ notice was given to the team for its first-ever RTD operation conducted at Tak Ying House in Tak Long Estate on 3 and 4 March, Ms Ng had to race against time to procure adequate supplies within a very short period of time. These included personal protective equipment and rapid antigen test kits for colleagues, as well as Chinese medicine packs and canned food for households in the target building. “We always keep two sets of supplies, one for the immediate RTD operation and the other as stand-by for the next one,” Ms Ng explained.
Mr Lai and Mr Chan recalled their key tasks in the operation. “On Day One, we knocked on the door of each household to inform the residents to go downstairs for nucleic acid tests; on Day Two, we called those who tested positive by phone for follow-up, checked whether the residents had already obtained a negative test result before allowing them to leave the restricted area, and re-opened the restricted area by noon finally.” Many challenges arose in the operation, one of them was data mapping. The testing contractor only had the identity card, mobile phone and reference numbers of those being tested, but did not have the crucial information such as to which households they belonged, thus making it difficult for the responsible colleagues to follow up on the positive cases. Fortunately, the team was able to draw on the rich information technology (IT) expertise of the EMSD to promptly complete the data mapping, so that follow-up action could be carried out smoothly.
“Given the complex and mammoth operation, and the need to work with unfamiliar staff from different departments, we are glad that working with high team spirit, we got all the difficult tasks done,” Mr Chan said.
“We are grateful that our colleagues were so accommodating and that the residents were supportive of our work,” Mr Lai added.
Mr Lee Che-kit, the chief engineer of the DTD, led the RTD operation at Yau Oi Estate on 9 and 10 March as the deputy field-commander. “In this operation, we alerted the testing contractor that the information they obtained from the residents was insufficient for following up on the positive cases,” he said. The insight prompted the contractor to obtain more information required from the residents, making subsequent RTD operations more efficient.
Refurbishing World-class Escalator with a Big Heart
During the refurbishment works, Mr Ho Chun-to, James, an engineer, was committed to maintaining good communication with members of the public. He handled public enquiries with patience and closely monitored and followed up on the works progress, with a view to minimising the impact on the daily lives of the public.
The 800-metre Central to Mid-Levels Escalator and Walkway System (the System) is the longest covered outdoor escalator in the world. In 2018, the System underwent refurbishment works. As the service life of all the 19 escalators and walkways of the System had been expired then, all of them had to be replaced. The four-year refurbishment works were carried out in 11 phases. It is expected that all the works will be completed and the System fully re-opened by April 2022 for public use.
Two years into the project, Mr Ho Chun-to, James, an engineer of the Boundary Crossing Facilities and Transport Services Division, joined the team responsible for the refurbishment of the System in January 2020. Mr Ho and the team actively co-ordinated with the Transport Department, the project client, as well as other government departments, including the Home Affairs Department and Hong Kong Police Force, to tackle myriad challenges. For example, the team had to ensure that the works will not affect the existing canopies of the System. Moreover, the narrow streets along the System added difficulties to the works, as truck-mounted cranes needed to be deployed for lifting operations while disruption to vehicle and pedestrian traffic had to be minimised. In addition, the team had to solicit support from the local community, composing of different residents and commercial tenants with diverse cultural background.
To facilitate smooth implementation of the project, the team adopted the approach of closing relevant road sections for an hour every day for replacement works, with an aim to minimising the traffic impacts. On one occasion, a seriously ill elderly person on a car going to seek medical treatment could not continue the way due to the road closure; on another occasion, a car carrying a pet in critical condition was obstructed. On both occasions, the team immediately re-opened the closed road section to cater for the urgent need. In another instance in early 2021, when the Drainage Services Department put in a last-minute request for urgent access to a manhole in a closed road section to take underground sewage samples for COVID-19 testing, our staff also made arrangements at once to allow the officers concerned to enter the area. “These examples show our flexibility and adaptability in various situations with caring attitude with regard to the needs of the community,” Mr Ho said.
With careful planning and hard work, the time lost for temporary road re-opening did not cause any major delay in the project. Mr Ho also said that working on the project, he gained much experience in handling public enquiries and complaints, and has become more patient, enabling him to overcome similar challenges with ease in the future. Looking back at the implementation of the project, he would like to thank his team for their support and the community for its forbearance.
Two years into the project, Mr Ho Chun-to, James, an engineer of the Boundary Crossing Facilities and Transport Services Division, joined the team responsible for the refurbishment of the System in January 2020. Mr Ho and the team actively co-ordinated with the Transport Department, the project client, as well as other government departments, including the Home Affairs Department and Hong Kong Police Force, to tackle myriad challenges. For example, the team had to ensure that the works will not affect the existing canopies of the System. Moreover, the narrow streets along the System added difficulties to the works, as truck-mounted cranes needed to be deployed for lifting operations while disruption to vehicle and pedestrian traffic had to be minimised. In addition, the team had to solicit support from the local community, composing of different residents and commercial tenants with diverse cultural background.
To facilitate smooth implementation of the project, the team adopted the approach of closing relevant road sections for an hour every day for replacement works, with an aim to minimising the traffic impacts. On one occasion, a seriously ill elderly person on a car going to seek medical treatment could not continue the way due to the road closure; on another occasion, a car carrying a pet in critical condition was obstructed. On both occasions, the team immediately re-opened the closed road section to cater for the urgent need. In another instance in early 2021, when the Drainage Services Department put in a last-minute request for urgent access to a manhole in a closed road section to take underground sewage samples for COVID-19 testing, our staff also made arrangements at once to allow the officers concerned to enter the area. “These examples show our flexibility and adaptability in various situations with caring attitude with regard to the needs of the community,” Mr Ho said.
With careful planning and hard work, the time lost for temporary road re-opening did not cause any major delay in the project. Mr Ho also said that working on the project, he gained much experience in handling public enquiries and complaints, and has become more patient, enabling him to overcome similar challenges with ease in the future. Looking back at the implementation of the project, he would like to thank his team for their support and the community for its forbearance.
Guardians of Good Ventilation amid the Epidemic
In response to the clusters of infection cases in many restaurants during the outbreak of the fifth wave of the epidemic, Ms Kwan Ho-yu, Lillian (middle), an engineer and her team actively examined the ventilation systems of related restaurants and provided professional advice and support to client departments.
Maintaining good ventilation in dine-in restaurants is crucial for infection prevention and control amid the epidemic. Since the onset of COVID-19, clusters of infection cases have been detected in a number of restaurants in Hong Kong. Ms Kwan Ho-yu, Lillian, an engineer of the Municipal Sector Division and Mr Chan Man-tak, an inspector of the same division, have actively supported the Government’s ventilation investigations at restaurants with COVID-19 outbreaks, thus accumulating abundant experience in this area of work. In late December 2021, a cluster of infection cases at a Chinese restaurant in the Festival Walk triggered the fifth wave of the epidemic. Ms Kwan and her team went to the scene to examine the ventilation system of the restaurant and provided technical support to the Centre for Health Protection (CHP) and the Food and Environmental Hygiene Department. She and her team have subsequently been called upon to investigate the ventilation systems at a number of restaurants.
“As each restaurant was different in its ventilation design and the investigation had to be conducted urgently, we encountered numerous difficulties initially, such as being unable to identify the exact location of the fresh air intake,” Ms Kwan said. That means teamwork would be more important than ever. She was really grateful for the staunch support rendered by her team members. For example, her inspectorate colleagues usually had to climb up high near the ceiling to remove dust-covered air vent covers for the team to measure air changes per hour (ACH).
Mr Chan, one of Ms Kwan’s team members, has participated in numerous investigations of ventilation systems since the epidemic began in 2020. His work included measuring ACH to ascertain if the amount of fresh air was sufficient, and contacting the persons-in-charge of the restaurant for details such as the exact size and configuration of each section of the restaurants.
“Together with the persons-in-charge, we tried to reconstruct the virus transmission scenarios by conducting smoke tests at the seats of the confirmed patients to simulate the most likely airflow patterns during the virus transmission for the CHP’s reference,” he said.
Ms Kwan and Mr Chan have also helped draw up ventilation guidelines for restaurants and residential care homes for the elderly for operators’ reference. When these venues have completed the requisite improvement works based on the ventilation investigation results, input and re-assessment of the team are required prior to their re-opening.
“Ventilation can be a matter of life and death, especially for the elderly, amid the epidemic. It is our duty to join in the fight against the epidemic. We are delighted to be of help,” both said in unison.
“As each restaurant was different in its ventilation design and the investigation had to be conducted urgently, we encountered numerous difficulties initially, such as being unable to identify the exact location of the fresh air intake,” Ms Kwan said. That means teamwork would be more important than ever. She was really grateful for the staunch support rendered by her team members. For example, her inspectorate colleagues usually had to climb up high near the ceiling to remove dust-covered air vent covers for the team to measure air changes per hour (ACH).
Mr Chan, one of Ms Kwan’s team members, has participated in numerous investigations of ventilation systems since the epidemic began in 2020. His work included measuring ACH to ascertain if the amount of fresh air was sufficient, and contacting the persons-in-charge of the restaurant for details such as the exact size and configuration of each section of the restaurants.
“Together with the persons-in-charge, we tried to reconstruct the virus transmission scenarios by conducting smoke tests at the seats of the confirmed patients to simulate the most likely airflow patterns during the virus transmission for the CHP’s reference,” he said.
Ms Kwan and Mr Chan have also helped draw up ventilation guidelines for restaurants and residential care homes for the elderly for operators’ reference. When these venues have completed the requisite improvement works based on the ventilation investigation results, input and re-assessment of the team are required prior to their re-opening.
“Ventilation can be a matter of life and death, especially for the elderly, amid the epidemic. It is our duty to join in the fight against the epidemic. We are delighted to be of help,” both said in unison.
Going Above and Beyond to Avert Auto-LPG Supply Shortage Crisis
The supply of liquefied petroleum gas (LPG) had been generally stable in Hong Kong, but it was almost disrupted in the fourth quarter of 2021 when LPG vessels transporting LPG to Hong Kong from Zhuhai and Dongguan were severely delayed due to the collective impact of COVID-19, international shipping bottlenecks and typhoons, putting Hong Kong on the verge of a LPG shortage. In view of the imminent plight then, Mr Lam Heung-chung, Marco, an engineer of the Gas Standards Office in charge of regulating LPG filling stations, LPG vehicles and gas safety, reacted immediately by coordinating the collaboration among companies in the trade and seeking help from the Mainland, and hence resolved the crisis promptly.
At that time, Mr Lam and his team learned that certain auto-LPG supply companies only had a few days of inventory left, and some LPG filling stations might have to suspend operation if replenishment could not be made in time. This could upset the normal operation of more than 20 000 taxis and light buses across the territory.
To deal with the emergency, the team went above and beyond its gas safety regulatory duties and held an urgent meeting with all gas supply companies to gauge the territory-wide LPG inventory and daily consumption rate, so as to work out informed solutions and ensure stable LPG supply for taxis and light buses.
As immediate action was vital, the team promptly coordinated with local gas supply companies within a tight time frame and successfully facilitated an inventory-on-loan arrangement among suppliers in the nick of time, on the night before the inventory of the LPG filling stations concerned was totally depleted. The arrangement ensured that all LPG filling stations could maintain normal LPG filling services the following day and in the immediate period afterwards.
At the same time, the team sought assistance directly from the co-operating counterparts in the Greater Bay Area. Through the Guangdong Provincial Association for Science and Technology, they contacted the Department of Transport of Guangdong Province and explained in writing the next day the LPG supply crisis in Hong Kong. Upon coordination of the Mainland departments, Hong Kong LPG vessels were given priority for entering and departing from the Mainland ports, and finally LPG was shipped to Hong Kong for replenishment in time.
“The crisis was resolved thanks to the gas supply companies’ mutual support, the swift assistance of the Mainland departments and the team’s collective efforts. By December, local auto-LPG supply has been returned to normal. After the incident, the acute situation that night often springs to mind when I take a taxi. That’s why I often chat with taxi drivers to find out which stations they go for refuelling, the auto-LPG prices and queuing time, so as to learn more about their daily operation. The experience of the emergency has endowed me with a stronger sense of mission and greater dedication to my work.”
To deal with the emergency, the team went above and beyond its gas safety regulatory duties and held an urgent meeting with all gas supply companies to gauge the territory-wide LPG inventory and daily consumption rate, so as to work out informed solutions and ensure stable LPG supply for taxis and light buses.
As immediate action was vital, the team promptly coordinated with local gas supply companies within a tight time frame and successfully facilitated an inventory-on-loan arrangement among suppliers in the nick of time, on the night before the inventory of the LPG filling stations concerned was totally depleted. The arrangement ensured that all LPG filling stations could maintain normal LPG filling services the following day and in the immediate period afterwards.
At the same time, the team sought assistance directly from the co-operating counterparts in the Greater Bay Area. Through the Guangdong Provincial Association for Science and Technology, they contacted the Department of Transport of Guangdong Province and explained in writing the next day the LPG supply crisis in Hong Kong. Upon coordination of the Mainland departments, Hong Kong LPG vessels were given priority for entering and departing from the Mainland ports, and finally LPG was shipped to Hong Kong for replenishment in time.
“The crisis was resolved thanks to the gas supply companies’ mutual support, the swift assistance of the Mainland departments and the team’s collective efforts. By December, local auto-LPG supply has been returned to normal. After the incident, the acute situation that night often springs to mind when I take a taxi. That’s why I often chat with taxi drivers to find out which stations they go for refuelling, the auto-LPG prices and queuing time, so as to learn more about their daily operation. The experience of the emergency has endowed me with a stronger sense of mission and greater dedication to my work.”
A New Chapter on Conservation Education: Compiling STEAM Educational Kit on Solar Harvest for Primary Schools
In a bid to promote the use of renewable energy (RE), the EMSD not only helps eligible schools install solar energy generation systems through Solar Harvest, but also compiles a STEAM educational kit to stimulate students’ interest in scientific learning and deepen their understanding of RE and strategies regarding climate change. Taking on the new challenge boldly, Mr Lam Tung-him, Alex, an assistant engineer of the Energy Efficiency Office, stepped out of his comfort zone of E&M engineering and committed to the compilation of educational kit, an area that was totally new to him.
Mr Lam co-ordinated and led a curriculum development team from the University of Hong Kong to compile for primary schools the first STEAM educational kit, with a total of eight themes, on Solar Harvest. In the process, Mr Lam maintained close communication with the working group, comprising representatives from the then Environment Bureau, Education Bureau (EDB) and EMSD, as well as school teachers and consultants, formed for the compilation of the teaching materials. Completed in a meticulous compilation process, the STEAM educational kit has been approved by the EDB as teaching materials under the primary school curriculum.
The kit comes in two sets separately for junior and senior primary school levels. Each set comprises materials designed for teachers and students respectively, worksheets, a list of materials to be procured by schools for STEAM activities, frequently asked questions and educational videos. The content is written in simple language and full of interactive elements. At every stage of the curriculum, there are hands-on activities for students to make solar-powered handicrafts after learning the relevant theories. Guided by the EMSD mascots, students will also be taken on virtual reality tours of solar energy generation facilities.
“The EMSD is the gatekeeper of technical information of the teaching materials. Coupled with the approval of the EDB as being suitable for the primary school curriculum, the educational kit is highly authoritative. Upon its launch, teachers can flexibly use the high-quality and approved educational kit for teaching based on students’ level and teaching progress, without having to search for other teaching materials. Students can also pick up the knowledge about RE from the basics at a young age. I find this job really meaningful,” Mr Lam said.
The educational kit will be introduced in the 2022/23 academic year. Primary school teachers may browse the EMSD webpage on Solar Harvest anytime to access the educational kit. Schools participating in Solar Harvest with solar energy generation systems connected on-grid can access the Real-time Monitoring System through the Virtual Reality learning platform such that the students can browse the electricity generated by schools’ solar energy generation systems in real time. The introduction of the education kit will mark a new chapter of RE education in Hong Kong.
Mr Lam and his team has begun the compilation of an education kit on Solar Harvest for secondary schools, with separate content for junior and senior secondary levels to align with the Science curriculum for junior secondary levels, and Physics curriculum for senior secondary levels. More technical information will be included in the kit too to suit the level of secondary students.
The kit comes in two sets separately for junior and senior primary school levels. Each set comprises materials designed for teachers and students respectively, worksheets, a list of materials to be procured by schools for STEAM activities, frequently asked questions and educational videos. The content is written in simple language and full of interactive elements. At every stage of the curriculum, there are hands-on activities for students to make solar-powered handicrafts after learning the relevant theories. Guided by the EMSD mascots, students will also be taken on virtual reality tours of solar energy generation facilities.
“The EMSD is the gatekeeper of technical information of the teaching materials. Coupled with the approval of the EDB as being suitable for the primary school curriculum, the educational kit is highly authoritative. Upon its launch, teachers can flexibly use the high-quality and approved educational kit for teaching based on students’ level and teaching progress, without having to search for other teaching materials. Students can also pick up the knowledge about RE from the basics at a young age. I find this job really meaningful,” Mr Lam said.
The educational kit will be introduced in the 2022/23 academic year. Primary school teachers may browse the EMSD webpage on Solar Harvest anytime to access the educational kit. Schools participating in Solar Harvest with solar energy generation systems connected on-grid can access the Real-time Monitoring System through the Virtual Reality learning platform such that the students can browse the electricity generated by schools’ solar energy generation systems in real time. The introduction of the education kit will mark a new chapter of RE education in Hong Kong.
Mr Lam and his team has begun the compilation of an education kit on Solar Harvest for secondary schools, with separate content for junior and senior secondary levels to align with the Science curriculum for junior secondary levels, and Physics curriculum for senior secondary levels. More technical information will be included in the kit too to suit the level of secondary students.
“E&M Detective” Overcoming Challenges Rarely Known in Conducting In-depth Investigation of Electrical Incidents
Every year, the EMSD investigates over 400 suspected electrical incidents on average, and over 100 of them are confirmed to be related to electricity after investigation. Overcoming manifold difficulties rarely known to people with his rich experience, Mr Lam Wai-kei, a chief technical officer of the Electricity Legislation Division (ELD) thoroughly examines the electricity supply systems and appliances at the incident site in each investigation, in order to identify incident causes for the deceased or victims, as well as spotting various risks of electrical incidents with a view to strengthening relevant promotion and education efforts on electrical safety.
Mr Lam recalled that there was, in 2016, a home electrocution incident, in which a scoring engineer died of electrocution while bathing in a village house. At that time, the investigation team Mr Lam led checked every electrical appliance and all wiring in the house. Nevertheless, after more than 18 hours of work at site, the team still could not find any installation with electricity leakage problem. It was only after repeated thorough site inspection that he found out that a nearby house, which was used as a studio and about 100 metres away from the house concerned, had a non-compliant extension cord connected to the material house to obtain power supply. A wrongly wired lamp that was plugged into the extension cord caused electricity leakage and the electric current was transmitted through the earthing wire to the accidentally connected water pipes of the bathroom of the material house. Coupled with the lack of a residual current circuit breaker and effective earth connection in the material house, the fatal incident eventually occurred.
During the investigation of electrical incidents, the experience and knowledge in electrical systems of the EMSD’s investigators are certainly vital, but their ability to withstand psychological and physical stress should not be overlooked. “For instance, we are sometimes required to examine and collect evidence from the electrical appliances and power supply systems at perilous fire scenes, where the bodies of the deceased have not yet been removed, to determine if the fires are caused by electrical incidents,” Mr Lam said.
It is only human to be apprehensive working in the material places of incidents or accidents. “To ease my mind, I often remind myself that I’m there to find the causes of incidents for the deceased and victims. During duty months, it is difficult to have a deep sleep as I may be called for operation in the middle of the night. We also have to prioritise when there are five to six electricity-related cases in a single day. Furthermore, as evidence collection takes time and sometimes we have to work in remote areas, we have to be flexible with colleagues’ personal needs, such as meal-taking and bathroom visits. Such are the untold trials and tribulations of the work in the ELD,” Mr Lam said.
Mr Lam told us that the occurrence of electrical incidents was often attributed to the coincidence of three elements, which were a faulty protection device, electrical appliance breakdown or damage and improper use of electrical appliances. He cited an example in which a resident casually placed a hairdryer still hot after use on the mattress made of flammable materials, causing the mattress to catch fire due to overheating.
“Many incidents are actually avoidable. All it takes is cutting the power supply to all electrical appliances or charging devices before leaving home; cleaning refrigerators and washing machines regularly to avoid fire accidents caused by sparks from an operating machine igniting the gathered dust; and unplugging idle appliances. These daily habits are simple yet helpful for ensuring electrical safety,” Mr Lam said.
During the investigation of electrical incidents, the experience and knowledge in electrical systems of the EMSD’s investigators are certainly vital, but their ability to withstand psychological and physical stress should not be overlooked. “For instance, we are sometimes required to examine and collect evidence from the electrical appliances and power supply systems at perilous fire scenes, where the bodies of the deceased have not yet been removed, to determine if the fires are caused by electrical incidents,” Mr Lam said.
It is only human to be apprehensive working in the material places of incidents or accidents. “To ease my mind, I often remind myself that I’m there to find the causes of incidents for the deceased and victims. During duty months, it is difficult to have a deep sleep as I may be called for operation in the middle of the night. We also have to prioritise when there are five to six electricity-related cases in a single day. Furthermore, as evidence collection takes time and sometimes we have to work in remote areas, we have to be flexible with colleagues’ personal needs, such as meal-taking and bathroom visits. Such are the untold trials and tribulations of the work in the ELD,” Mr Lam said.
Mr Lam told us that the occurrence of electrical incidents was often attributed to the coincidence of three elements, which were a faulty protection device, electrical appliance breakdown or damage and improper use of electrical appliances. He cited an example in which a resident casually placed a hairdryer still hot after use on the mattress made of flammable materials, causing the mattress to catch fire due to overheating.
“Many incidents are actually avoidable. All it takes is cutting the power supply to all electrical appliances or charging devices before leaving home; cleaning refrigerators and washing machines regularly to avoid fire accidents caused by sparks from an operating machine igniting the gathered dust; and unplugging idle appliances. These daily habits are simple yet helpful for ensuring electrical safety,” Mr Lam said.
Inspecting the First Public Inclined Lift System in Hong Kong as the Gatekeeper for Safety
Two inclined lifts connecting Kwai Chung Estate and Wo Tong Tsui Street were completed in February 2022. Mr Leung Wai-yin, an inspector of the General Legislation Division, conducted the final inspection on the lifts as required by the legislation to confirm their safety, completing a crucial step before use permits were issued. Since the lifts commenced operation in April 2022, residents of Kwai Chung Estate can travel easily without having to climb more than a hundred steps.
The first public covered inclined lift system in Hong Kong, which is about 36-metre long, has two inclined lifts plying at a speed of 1.5 metres per second on the 30-degree slope between Wo Tong Tsui Street and Tai Wo Hau Road, with a journey time of less than one minute. Each lift can carry 24 passengers and has a loading capacity of 1 800 kg. The lifts are expected to have a daily patronage of 8 600 passenger trips every day, bringing great convenience to residents of the area.
Mr Leung remarked that inclined lifts are convenient for the use of the elderly and wheelchair users and can better meet the needs of the population in that area, hence they are more suitable than escalators for installation at the above location.
There are huge technical differences in inspecting inclined lifts and vertical lifts. “For inclined lifts, safety components such as traction machines, overspeed governors and brakes, are installed upside down or at an angle, and the tension and traction of each suspension rope that propels the lift car must be the same. Besides, due to the traction direction of inclined lifts and the inclination of their car guide rails, the car guide rails of inclined lifts must bear part of the car weight, whereas that of vertical lifts only control the up or down direction of the lift, which is relatively simpler,” Mr Leung explained.
In addition to testing the components, Mr Leung took the lift during the inspection to experience the lift operation as a user, with a view to figuring out how to improve passenger experience during lift acceleration and deceleration. “From past experience, most escalator incidents were caused by passengers who lost balance and fell over due to their failure to hold the handrail tightly, while most lift incidents involved passenger tripping due to levelling difference of the lift car at landing. In view of this, safety announcements will be broadcast before the cars of the inclined lift system arrive at or depart from the landing, to remind passengers to mind the lift door and hold the handrail tightly,” he said.
After the inclined lifts were put into service, Mr Leung made a point of taking the lifts whenever he worked in the neighbourhood to see if they were working properly. “Taking the lifts makes me aware of any wear and tear in the guide rails causing unstable car movement,” he said. Mr Leung’s commitment to serving the community naturally shone through in his words.
Mr Leung remarked that inclined lifts are convenient for the use of the elderly and wheelchair users and can better meet the needs of the population in that area, hence they are more suitable than escalators for installation at the above location.
There are huge technical differences in inspecting inclined lifts and vertical lifts. “For inclined lifts, safety components such as traction machines, overspeed governors and brakes, are installed upside down or at an angle, and the tension and traction of each suspension rope that propels the lift car must be the same. Besides, due to the traction direction of inclined lifts and the inclination of their car guide rails, the car guide rails of inclined lifts must bear part of the car weight, whereas that of vertical lifts only control the up or down direction of the lift, which is relatively simpler,” Mr Leung explained.
In addition to testing the components, Mr Leung took the lift during the inspection to experience the lift operation as a user, with a view to figuring out how to improve passenger experience during lift acceleration and deceleration. “From past experience, most escalator incidents were caused by passengers who lost balance and fell over due to their failure to hold the handrail tightly, while most lift incidents involved passenger tripping due to levelling difference of the lift car at landing. In view of this, safety announcements will be broadcast before the cars of the inclined lift system arrive at or depart from the landing, to remind passengers to mind the lift door and hold the handrail tightly,” he said.
After the inclined lifts were put into service, Mr Leung made a point of taking the lifts whenever he worked in the neighbourhood to see if they were working properly. “Taking the lifts makes me aware of any wear and tear in the guide rails causing unstable car movement,” he said. Mr Leung’s commitment to serving the community naturally shone through in his words.
An Innovative Tool Developed for Estimating FiT Payback
The Government introduced the Feed-in Tariff (FiT) Scheme to incentivise the private sector to install solar photovoltaic (PV) systems. However, how can members of the public estimate the solar power generation potential of their building rooftops and the FiT income concerned before installation? To this end, Ms Wong San-san, an engineer of the Energy Efficiency Office, coordinated the development of the Hong Kong Solar Irradiation Map (the Map) to provide reliable data for the public to make preliminary estimation.
The Map uses the Airborne Light Detection and Ranging data released by the Civil Engineering and Development Department and the GeoInfo Map provided by the Lands Department to build a digital surface model, and simulates the impact of factors such as buildings nearby and topography on solar irradiation with the aid of the 10-year solar irradiation data provided by the Hong Kong Observatory, so as to calculate the annual solar irradiation received at every building rooftop across the city. Such calculation has an accuracy rate of over 90%.
Those interested in setting up solar PV systems can draw the rooftop area intended for installation of a solar PV system on the Map. The Map will automatically calculate the generation capacity of the selected area and the corresponding FiT income. Members of the public can also use the payback calculator in the Map to obtain an estimation of the payback period.
The Map won a silver medal in the International Exhibition of Inventions of Geneva 2022. Ms Wong believed that the Map stood out because it integrated data from multiple dimensions, including geography, astronomy and surveying, and it was the first map which showed the solar irradiation of all building rooftops across the territory.
“Currently there aren’t many similar solar irradiation maps in the world, and most of them do not have calculation functions,” Ms Wong said. “The Hong Kong Solar Irradiation Map is the fruit of our research and development efforts in collaboration with the Hong Kong Polytechnic University, as well as an embodiment of the synergy of inter-departmental co-operation. During its development, I have learned a lot from other departments and greatly benefited.”
Those interested in setting up solar PV systems can draw the rooftop area intended for installation of a solar PV system on the Map. The Map will automatically calculate the generation capacity of the selected area and the corresponding FiT income. Members of the public can also use the payback calculator in the Map to obtain an estimation of the payback period.
The Map won a silver medal in the International Exhibition of Inventions of Geneva 2022. Ms Wong believed that the Map stood out because it integrated data from multiple dimensions, including geography, astronomy and surveying, and it was the first map which showed the solar irradiation of all building rooftops across the territory.
“Currently there aren’t many similar solar irradiation maps in the world, and most of them do not have calculation functions,” Ms Wong said. “The Hong Kong Solar Irradiation Map is the fruit of our research and development efforts in collaboration with the Hong Kong Polytechnic University, as well as an embodiment of the synergy of inter-departmental co-operation. During its development, I have learned a lot from other departments and greatly benefited.”
Rising to the Air-Conditioning Challenge in Activating Large COVID-19 Treatment Centres Promptly
Amid the epidemic, Mr Wong Tat-tong, Victor, an engineer, led his team to support the re-configuration of the ventilation and air-conditioning system at the Treatment Centre for COVID-19 in the AsiaWorld-Expo. Exerting substantive expertise and experience, the team successfully completed the task of converting related halls into negative pressure wards under a very tight schedule.
In this epidemic, Mr Wong Tat-tong, Victor, an engineer of the Health Sector Division, has been dedicated to the establishment of large scale treatment centres. Starting from August 2020, he assisted the Hospital Authority (HA) and Architectural Services Department to swiftly convert four exhibition halls at the AsiaWorld-Expo (AWE) into a community treatment facility with a negative pressure environment, which commenced operation subsequently in October the same year. When the fifth wave of the epidemic broke out in early 2022, Mr Wong was tasked with the urgent work of converting the venue at AWE into a Treatment Centre for COVID-19 for treating a large number of confirmed patients.
Talking about the key challenge in the AWE project, Mr Wong said it was the existing air-conditioning system, which ran on a thermal energy storage system with ice storage features, as it was originally designed to maximise energy efficiency at a venue that did not have to operate 24 hours a day. While the Treatment Centre would operate 24 hours a day, Mr Wong’s team had to modify the system to provide round-the-clock air-conditioning. The solution was to add chillers, and re-configure the system by increasing the number of air-handling units.
At the outbreak of the fifth wave of the epidemic, Mr Wong helped the HA again in converting another hall in the AWE and setting up the Treatment Centre for COVID-19 for receiving confirmed patients with mild symptoms, so that public hospitals could focus on taking care of severe cases. “Time was really tight, and more than 100 new air purifiers had to be ready,” he recalled the situation then. “We all join the hands-on work, including cutting air filters to the right size for the air purifiers late into the night. After several days of overnight work, all conversion works were eventually completed before the deadline.”
The re-configured air-conditioning system worked well and created a negative pressure environment for the entire Treatment Centre, but Mr Wong soon noted another complication. While the elderly, who were sensitive to cold air, often asked to raise the temperature setting, staff working in the halls preferred cooler temperatures as they had full personal protective equipment on. It was important to strike a balance among different needs by fine-tuning the system from time to time.
Striving for excellence, Mr Wong always seeks to improve the air-conditioning system. “We hope to develop a technical solution, which will enable the air-conditioning system to quickly switch between running on a thermal energy storage system and operating on a round-the-clock basis for emergencies, just by tapping a button,” Mr Wong indicated he would continue to work towards this goal.
Talking about the key challenge in the AWE project, Mr Wong said it was the existing air-conditioning system, which ran on a thermal energy storage system with ice storage features, as it was originally designed to maximise energy efficiency at a venue that did not have to operate 24 hours a day. While the Treatment Centre would operate 24 hours a day, Mr Wong’s team had to modify the system to provide round-the-clock air-conditioning. The solution was to add chillers, and re-configure the system by increasing the number of air-handling units.
At the outbreak of the fifth wave of the epidemic, Mr Wong helped the HA again in converting another hall in the AWE and setting up the Treatment Centre for COVID-19 for receiving confirmed patients with mild symptoms, so that public hospitals could focus on taking care of severe cases. “Time was really tight, and more than 100 new air purifiers had to be ready,” he recalled the situation then. “We all join the hands-on work, including cutting air filters to the right size for the air purifiers late into the night. After several days of overnight work, all conversion works were eventually completed before the deadline.”
The re-configured air-conditioning system worked well and created a negative pressure environment for the entire Treatment Centre, but Mr Wong soon noted another complication. While the elderly, who were sensitive to cold air, often asked to raise the temperature setting, staff working in the halls preferred cooler temperatures as they had full personal protective equipment on. It was important to strike a balance among different needs by fine-tuning the system from time to time.
Striving for excellence, Mr Wong always seeks to improve the air-conditioning system. “We hope to develop a technical solution, which will enable the air-conditioning system to quickly switch between running on a thermal energy storage system and operating on a round-the-clock basis for emergencies, just by tapping a button,” Mr Wong indicated he would continue to work towards this goal.
An Unusual Trip: Flying to Austria for Testing Aircraft Rescue and Firefighting Vehicles
Mr Wong Yu-hong, Simon (2nd right) and his team flew to Austria in early 2022 to support the Fire Services Department in testing and commissioning the Aircraft Rescue and Firefighting vehicles. The trip was full of obstacles with severe weather in Austria and disruptions to the team’s itinerary due to the epidemic. Nevertheless, the team managed to overcome all difficulties and ensured that the vehicles were delivered on time.
A new fleet of 14 advanced Aircraft Rescue and Firefighting (ARFF) vehicles will be deployed at the third runway of the Hong Kong International Airport (HKIA). Mr Wong Yu-hong, Simon, an engineer in the Security and Vehicle Services Division, was responsible for the procurement of the relevant vehicles. Experienced in vehicle procurement, he participated in every stage of the procurement exercise, from tendering to testing and commissioning of the new fleet.
Since some of the ARFF vehicles procured were manufactured in Linz, Austria, equipment checks and on-site performance tests had to be conducted there for the identification of any defects and prompt rectification. In view of this, Mr Wong led three colleagues from the EMSD to form a team with the representatives of the Fire Services Department (FSD), to fly to Linz for testing and receiving nine of the new vehicles.
The team arrived at the production plant in Linz in January 2022, in the depths of the Austrian winter. They stayed for a total of 22 days, working in two groups, each with two EMSD and two FSD colleagues.
“The plant rented a small airfield nearby for us to conduct the driving performance tests. We spent two full days working at the airfield under the temperatures of about -5°C, with snow and ground frost from time to time,” Mr Wong said. Testing of vehicles is usually avoided in European winters. Nevertheless, as the ARFF vehicles needed to be delivered to Hong Kong by May 2022, in order to allow sufficient time for final testing at HKIA before the third runway opened in July.
Another challenge during the trip was the strict inbound flight control measures implemented in Hong Kong in response to the epidemic. “As the trip was drawing to the end, we were stopped at the boarding gate at Vienna Airport and were told that flights to Hong Kong had been suspended for 14 days,” Mr Wong recalled. Fortunately, with the help of EMSD colleagues in Hong Kong, the team finally left Austria after being stranded for two days. Upon arrival in Hong Kong, the team immediately underwent 14 days of hotel quarantine.
From this unusual trip, Mr Wong has drawn insights. The planning and execution of the entire overseas trip was undoubtedly difficult and the flight suspension in the end posed further challenges to the trip. Nevertheless, he was grateful that the team had been calm and professional in the face of difficulties and crises. The trip also broadened his horizons in ARFF technologies, and he is now exploring with the FSD the potential of using hybrid or electric vehicles as firefighting and rescue vehicles.
Since some of the ARFF vehicles procured were manufactured in Linz, Austria, equipment checks and on-site performance tests had to be conducted there for the identification of any defects and prompt rectification. In view of this, Mr Wong led three colleagues from the EMSD to form a team with the representatives of the Fire Services Department (FSD), to fly to Linz for testing and receiving nine of the new vehicles.
The team arrived at the production plant in Linz in January 2022, in the depths of the Austrian winter. They stayed for a total of 22 days, working in two groups, each with two EMSD and two FSD colleagues.
“The plant rented a small airfield nearby for us to conduct the driving performance tests. We spent two full days working at the airfield under the temperatures of about -5°C, with snow and ground frost from time to time,” Mr Wong said. Testing of vehicles is usually avoided in European winters. Nevertheless, as the ARFF vehicles needed to be delivered to Hong Kong by May 2022, in order to allow sufficient time for final testing at HKIA before the third runway opened in July.
Another challenge during the trip was the strict inbound flight control measures implemented in Hong Kong in response to the epidemic. “As the trip was drawing to the end, we were stopped at the boarding gate at Vienna Airport and were told that flights to Hong Kong had been suspended for 14 days,” Mr Wong recalled. Fortunately, with the help of EMSD colleagues in Hong Kong, the team finally left Austria after being stranded for two days. Upon arrival in Hong Kong, the team immediately underwent 14 days of hotel quarantine.
From this unusual trip, Mr Wong has drawn insights. The planning and execution of the entire overseas trip was undoubtedly difficult and the flight suspension in the end posed further challenges to the trip. Nevertheless, he was grateful that the team had been calm and professional in the face of difficulties and crises. The trip also broadened his horizons in ARFF technologies, and he is now exploring with the FSD the potential of using hybrid or electric vehicles as firefighting and rescue vehicles.
Seven-day Race to Restart Cross-Boundary Railway Freight Service
During the fifth wave of COVID-19, cross-boundary cargo flow almost ground to a halt. To open up more logistics channels between Hong Kong and the Mainland, the then Transport and Housing Bureau (THB) liaised with the Mainland counterparts and, upon discussion, decided to reactivate the long-suspended cross-boundary railway freight service within seven days. Mr Yeung Chi-yuet, Chris, a senior engineer, and Ms Chan Ching-man, Kitty, an engineer, both under the Railways Branch (RB), led a team of ten to race against time to plan and conduct on-site railway safety testing in conjunction with the MTR Corporation Limited (MTRCL). Living up to expectation, the team managed to accomplish the “mission impossible” within an extremely short period of seven days, paving the way comprehensively for the resumption of the railway freight service. Eventually, the first Mainland freight train brought about 50 tonnes of much-needed anti-epidemic supplies to Hong Kong on 2 March 2022.
“The timeframe was very short. We only had a day or two to prepare after being told of the mission. The team was formed immediately and we readied ourselves to work round the clock to make all necessary arrangement for the prompt resumption of the railway freight service, on top of the routine duties of monitoring the MTRCL’s maintenance work. It was a monumental challenge indeed,” Ms Chan said.
The preparation work for the reactivation of the railway freight service was complicated as the current freight trains have been quite different from the previous ones since the railway freight service was suspended years ago. The first task was to conduct technical assessments on the Mainland freight trains designated for the Hong Kong run based on the train models, specifications and data confirmed by the Mainland, so as to ensure the compatibility between the Mainland freights trains and Hong Kong’s railway infrastructure for the Mainland freight trains to operate safely on the railways in Hong Kong. Meanwhile, the RB required the MTRCL to conduct not only maintenance and repair of the tracks in accordance with established mechanisms, but also a series of reviews on the tracks before the Mainland freight trains started their runs to Hong Kong, which included measuring the track gauges, checking the track condition and the integrity of the point switches, etc. The RB and the MTRCL personnel also carried out on-site thorough inspection of the approximately 1-km track between the boundary and the Lo Wu Marshalling Yard, and reviewed various measurement data repeatedly to ensure that the Mainland freight trains could operate safely on the railway infrastructure in Hong Kong.
Once the cargo containers were transported to the Lo Wu Marshalling Yard by the Mainland freight trains, they had to be lifted onto container trucks by cranes for local transportation and distribution of the supplies. However, the Yard was a MTRCL depot for stationing trains and covered with a network of overhead high voltage cables. Extra caution was called for in the lifting of the containers to avoid touching the cables and endangering the crane operators or potentially affecting the MTRCL’s train services. In view of the above, Mr Yeung demanded that the MTRCL should conduct a risk assessment of the crane operation and formulate risk mitigation measures and contingency plans. In the end, the electricity supply to the cables near the craning area was isolated, and the tracks were barricaded by stationary trains to prevent the cranes from straying onto the tracks accidentally and triggering electrical incidents.
Monitoring the testing of the signalling and communication systems was another major task. During the drills and the actual freight train operations, the RB deployed staff to the MTRCL’s Tsing Yi Control Centre and the Lo Wu Marshalling Yard to closely monitor the operation of the signalling system and the communication between the MTRCL and the Mainland train control centre to ensure that the signalling system functioned normally and the Mainland drivers operated the train according to the MTRCL’s arrangements on the Hong Kong tracks.
The usual practice in the past was to have an MTRCL driver get on the freight train and guide the Mainland driver to operate on the Hong Kong railway after the Mainland train had entered Hong Kong. However, the MTRCL drivers could not get on the train due to anti-epidemic control arrangements. The MTRCL had to arrange flag signalmen at designated locations at the boundary, the Marshalling Yard and along the tracks, to manually guide the Mainland drivers where to go and where to stop by flags, and perform visual checks to ascertain that the trains were running normally on the tracks. Since the scheduling of the Mainland freight trains was irregular depending on a host of factors, the MTRCL had to put flag signalmen and other staff members on stand-by in shifts. Accordingly, the RB also arranged staff to monitor the freight train operation and the functioning of various railway systems at the Tsing Yi Control Centre and the Lo Wu Marshalling Yard.
Despite the overwhelming challenges, Mr Yeung and his team managed to complete all preparations within seven days against all the odds. Upon the satisfactory trial run of an empty Mainland train operating to Hong Kong on 1 March, the cross-boundary railway freight service was officially reactivated the following day.
“Having to quickly restart the long-suspended cross-boundary railway freight service was an enormous undertaking. We made speedy responses and brought our team together for preparations, risk assessments and formulation of contingency plans, putting all preparation plans in place through working closely with the MTRCL. Every day was packed with lots of things to do, be it monitoring the testing, inspecting the track condition and attending regular meetings to communicate closely with the THB, other government departments, the MTRCL and the Mainland counterparts. That said, we rose to challenges with determination and perseverance and pulled out all the stops for the mission, and our Mainland counterparts were equally determined to make it work. With the concerted effort of all, the cross-boundary railway freight service was put back on track as scheduled. It was an honour to be able to contribute to Hong Kong during the epidemic,” Mr Yeung said.
With the seven-day endeavours, the RB and MTRCL are ready to reactivate the cross-boundary railway freight service anytime should Hong Kong faces cross-boundary logistics bottlenecks again. Meanwhile, the RB and the MTRCL have even put in place the option of transporting livestock from the Mainland to the Sheung Shui Slaughterhouse by using the Mainland freight trains, just in case it is needed.
The preparation work for the reactivation of the railway freight service was complicated as the current freight trains have been quite different from the previous ones since the railway freight service was suspended years ago. The first task was to conduct technical assessments on the Mainland freight trains designated for the Hong Kong run based on the train models, specifications and data confirmed by the Mainland, so as to ensure the compatibility between the Mainland freights trains and Hong Kong’s railway infrastructure for the Mainland freight trains to operate safely on the railways in Hong Kong. Meanwhile, the RB required the MTRCL to conduct not only maintenance and repair of the tracks in accordance with established mechanisms, but also a series of reviews on the tracks before the Mainland freight trains started their runs to Hong Kong, which included measuring the track gauges, checking the track condition and the integrity of the point switches, etc. The RB and the MTRCL personnel also carried out on-site thorough inspection of the approximately 1-km track between the boundary and the Lo Wu Marshalling Yard, and reviewed various measurement data repeatedly to ensure that the Mainland freight trains could operate safely on the railway infrastructure in Hong Kong.
Once the cargo containers were transported to the Lo Wu Marshalling Yard by the Mainland freight trains, they had to be lifted onto container trucks by cranes for local transportation and distribution of the supplies. However, the Yard was a MTRCL depot for stationing trains and covered with a network of overhead high voltage cables. Extra caution was called for in the lifting of the containers to avoid touching the cables and endangering the crane operators or potentially affecting the MTRCL’s train services. In view of the above, Mr Yeung demanded that the MTRCL should conduct a risk assessment of the crane operation and formulate risk mitigation measures and contingency plans. In the end, the electricity supply to the cables near the craning area was isolated, and the tracks were barricaded by stationary trains to prevent the cranes from straying onto the tracks accidentally and triggering electrical incidents.
Monitoring the testing of the signalling and communication systems was another major task. During the drills and the actual freight train operations, the RB deployed staff to the MTRCL’s Tsing Yi Control Centre and the Lo Wu Marshalling Yard to closely monitor the operation of the signalling system and the communication between the MTRCL and the Mainland train control centre to ensure that the signalling system functioned normally and the Mainland drivers operated the train according to the MTRCL’s arrangements on the Hong Kong tracks.
The usual practice in the past was to have an MTRCL driver get on the freight train and guide the Mainland driver to operate on the Hong Kong railway after the Mainland train had entered Hong Kong. However, the MTRCL drivers could not get on the train due to anti-epidemic control arrangements. The MTRCL had to arrange flag signalmen at designated locations at the boundary, the Marshalling Yard and along the tracks, to manually guide the Mainland drivers where to go and where to stop by flags, and perform visual checks to ascertain that the trains were running normally on the tracks. Since the scheduling of the Mainland freight trains was irregular depending on a host of factors, the MTRCL had to put flag signalmen and other staff members on stand-by in shifts. Accordingly, the RB also arranged staff to monitor the freight train operation and the functioning of various railway systems at the Tsing Yi Control Centre and the Lo Wu Marshalling Yard.
Despite the overwhelming challenges, Mr Yeung and his team managed to complete all preparations within seven days against all the odds. Upon the satisfactory trial run of an empty Mainland train operating to Hong Kong on 1 March, the cross-boundary railway freight service was officially reactivated the following day.
“Having to quickly restart the long-suspended cross-boundary railway freight service was an enormous undertaking. We made speedy responses and brought our team together for preparations, risk assessments and formulation of contingency plans, putting all preparation plans in place through working closely with the MTRCL. Every day was packed with lots of things to do, be it monitoring the testing, inspecting the track condition and attending regular meetings to communicate closely with the THB, other government departments, the MTRCL and the Mainland counterparts. That said, we rose to challenges with determination and perseverance and pulled out all the stops for the mission, and our Mainland counterparts were equally determined to make it work. With the concerted effort of all, the cross-boundary railway freight service was put back on track as scheduled. It was an honour to be able to contribute to Hong Kong during the epidemic,” Mr Yeung said.
With the seven-day endeavours, the RB and MTRCL are ready to reactivate the cross-boundary railway freight service anytime should Hong Kong faces cross-boundary logistics bottlenecks again. Meanwhile, the RB and the MTRCL have even put in place the option of transporting livestock from the Mainland to the Sheung Shui Slaughterhouse by using the Mainland freight trains, just in case it is needed.
Vaccine Fridge Monitoring System Enabled by Technology and Talent
To remotely monitor the medical fridges and vaccines, Mr Yip Wai-tong, Wallace, an engineer, and his team have actively provided uninterruptible power supply for the integrated Fridge Monitoring System at the Community Vaccination Centres. Their effort to safeguard the proper storage of vaccines was proved effective.
The COVID-19 Vaccination Programme (CVP) is vital to Hong Kong’s anti-epidemic strategy and an integrated Fridge Monitoring System (iFMS) developed by the EMSTF also plays a crucial role in the CVP.
Mr Yip Wai-tong, Wallace, an engineer of the Health Sector Division, led a team to design and install the iFMS at all the Community Vaccination Centres (CVCs) in 18 districts across the territory in early 2021. The system was proved successful in ensuring that COVID-19 vaccines are stored safely at proper low temperature.
The iFMS was developed as urgently requested by the Centre for Health Protection to tie in with the Government’s plan to launch the CVP in the same year. Leveraging his experience in converting general wards into second-tier negative pressure wards and installing numerous Mobile Modular High Efficiency Particulate Air Filter Units at public hospitals, Mr Yip led his team to spring into action for the development of the system. After considering the actual circumstances, the team decided to use narrow-band Internet of Things (IoT) technology to monitor medical fridges for vaccine storage in the CVCs. In other words, the IoT would operate on existing mobile networks which had a high coverage already. Some suggestions or requests from users, such as auto-generation of a simple report every morning, were promptly accepted to improve the system.
The iFMS is designed to monitor the fridge temperature and the ambient temperature and humidity at the CVC. Meanwhile, it can also detect faults in the fridge, the power supply system and other E&M equipment at the CVCs. Through IoT technology and sensors, all data are transmitted to the Regional Digital Control Centre (RDCC) at the EMSD Headquarters and the RDCC dashboard at the Central Government Offices for round-the-clock monitoring. If any abnormalities are detected, SMS alert messages will be sent to the responsible officers and stakeholders immediately.
“We take these alerts seriously and always arrange colleagues to call the responsible officers in person to ensure that the messages have been got through,” Mr Yip said. He and his colleagues have on several occasions rushed to the centres to personally attend to the supply issues on site after midnight.
“One of the insights gained from the iFMS experience is the importance of having both the ‘technology reserve’ and ‘talent reserve’ for the timely deployment of innovative projects,” Mr Yip said. “With technical expertise and a positive mindset, one will have the confidence to take on challenges.”
Mr Yip Wai-tong, Wallace, an engineer of the Health Sector Division, led a team to design and install the iFMS at all the Community Vaccination Centres (CVCs) in 18 districts across the territory in early 2021. The system was proved successful in ensuring that COVID-19 vaccines are stored safely at proper low temperature.
The iFMS was developed as urgently requested by the Centre for Health Protection to tie in with the Government’s plan to launch the CVP in the same year. Leveraging his experience in converting general wards into second-tier negative pressure wards and installing numerous Mobile Modular High Efficiency Particulate Air Filter Units at public hospitals, Mr Yip led his team to spring into action for the development of the system. After considering the actual circumstances, the team decided to use narrow-band Internet of Things (IoT) technology to monitor medical fridges for vaccine storage in the CVCs. In other words, the IoT would operate on existing mobile networks which had a high coverage already. Some suggestions or requests from users, such as auto-generation of a simple report every morning, were promptly accepted to improve the system.
The iFMS is designed to monitor the fridge temperature and the ambient temperature and humidity at the CVC. Meanwhile, it can also detect faults in the fridge, the power supply system and other E&M equipment at the CVCs. Through IoT technology and sensors, all data are transmitted to the Regional Digital Control Centre (RDCC) at the EMSD Headquarters and the RDCC dashboard at the Central Government Offices for round-the-clock monitoring. If any abnormalities are detected, SMS alert messages will be sent to the responsible officers and stakeholders immediately.
“We take these alerts seriously and always arrange colleagues to call the responsible officers in person to ensure that the messages have been got through,” Mr Yip said. He and his colleagues have on several occasions rushed to the centres to personally attend to the supply issues on site after midnight.
“One of the insights gained from the iFMS experience is the importance of having both the ‘technology reserve’ and ‘talent reserve’ for the timely deployment of innovative projects,” Mr Yip said. “With technical expertise and a positive mindset, one will have the confidence to take on challenges.”
Leveraging Digital Tools to Support the LegCo Election
Mr Yuen Wai-yip, Lobee, a senior engineer, led his team members to deploy new innovation and technology tools in the 2021 Legislative Council (LegCo) General Election to enhance work efficiency and effectiveness. Despite the immense pressure, they devoted their best efforts and completed all the tasks on time, contributing to the smooth running of the election.
The EMSTF has always provided E&M support to LegCo elections, for example, through the provision of electricity and lighting at polling stations. The latest LegCo General Election held on 19 December 2021 was no exception. Mr Yuen Wai-yip, Lobee, a senior engineer of the General Engineering Services Division (GESD), led his team to provide relevant support to the Registration and Electoral Office (REO) and opened up a new digital era for holding elections in Hong Kong.
Preparations for the 2021 LegCo General Election began soon after the District Council election in 2019. The efforts were translated into several “firsts” in this LegCo election, including the first-ever use of an Electronic Poll Register System to issue ballot papers at 693 polling stations and the adoption of a video recording system to monitor the counting process from 11:00 p.m., when 620 polling stations were converted to counting stations. We also rolled out a GESD-developed dashboard at the Emergency Response Centre in our headquarters for round-the-clock monitoring for the election from 18 to 20 December.
The dashboard was particularly effective in monitoring the works of contractors in the run-up to the election day. As each contractor was required to report the progress of their designated tasks via mobile devices, the dashboard was continually updated, giving Mr Yuen and his team access to a real-time overview of the progress of works at all polling stations as displayed on an interactive map of Hong Kong. The system also enabled them to readily retrieve the information of the responsibilities of contractors and their contact details for prompt follow-up. Given the large number of polling stations and contractors, this timely and efficient oversight was not possible in the past when progress updates solely relied on telephone calls.
Speaking of the challenges which the team faced, Mr Yuen cited the short period of time allowed to set up the video recording system for monitoring the counting process. “As the polling stations closed at 10:30 p.m., we only had 30 minutes to set up the device, so that video recording could begin at 11:00 p.m. sharp when the counting process commenced,” he said.
Mr Yuen attributed the team’s success to its rich work experience accumulated from previous elections and strong support from the senior management, as well as over 1600 colleagues from various divisions of the EMSD who rendered assistance on the election day. “The REO was most impressed with the dashboard, which we plan to deploy with other innovation and technology tools in the District Council election in 2023 and the next LegCo election in 2025 after further refinement,” he said.
Preparations for the 2021 LegCo General Election began soon after the District Council election in 2019. The efforts were translated into several “firsts” in this LegCo election, including the first-ever use of an Electronic Poll Register System to issue ballot papers at 693 polling stations and the adoption of a video recording system to monitor the counting process from 11:00 p.m., when 620 polling stations were converted to counting stations. We also rolled out a GESD-developed dashboard at the Emergency Response Centre in our headquarters for round-the-clock monitoring for the election from 18 to 20 December.
The dashboard was particularly effective in monitoring the works of contractors in the run-up to the election day. As each contractor was required to report the progress of their designated tasks via mobile devices, the dashboard was continually updated, giving Mr Yuen and his team access to a real-time overview of the progress of works at all polling stations as displayed on an interactive map of Hong Kong. The system also enabled them to readily retrieve the information of the responsibilities of contractors and their contact details for prompt follow-up. Given the large number of polling stations and contractors, this timely and efficient oversight was not possible in the past when progress updates solely relied on telephone calls.
Speaking of the challenges which the team faced, Mr Yuen cited the short period of time allowed to set up the video recording system for monitoring the counting process. “As the polling stations closed at 10:30 p.m., we only had 30 minutes to set up the device, so that video recording could begin at 11:00 p.m. sharp when the counting process commenced,” he said.
Mr Yuen attributed the team’s success to its rich work experience accumulated from previous elections and strong support from the senior management, as well as over 1600 colleagues from various divisions of the EMSD who rendered assistance on the election day. “The REO was most impressed with the dashboard, which we plan to deploy with other innovation and technology tools in the District Council election in 2023 and the next LegCo election in 2025 after further refinement,” he said.
Pulling Together to Support the Fight against the Fifth Wave of the Epidemic
With the outbreak of the serious fifth wave of the epidemic in early 2022, the fight against the virus was a race against time. Civil servants were mobilised to take up important tasks such as supporting the community and participating in “restriction-testing declaration” (RTD) operations. Mr Chan Chi-wai, a senior engineer of the General Legislation Division, took up the role of coordinating members from different divisions and sections under the Regulatory Services of the EMSD to participate in the anti-epidemic efforts on the frontline.
At the onset of the fifth wave of the epidemic, residents of Kwai Chung Estate were mandated to stay at home. The first major task of the EMSD’s anti-epidemic team was to deliver three meals a day to the residents in one of the 40-storey blocks of the estate. Despite the very limited time for us to prepare for this urgent operation, our colleagues completed the task successfully by promptly arranging a team of about 50 members to deliver three meals to the residents every day during the mandated period.
“Everyone was surely concerned about their own safety in the face of the rapid development of the fifth wave of the epidemic that time. However, as civil servants, we were determined to stay on the frontline to deliver hot meals to the residents. Though we do not have any direct contact with the residents, some of them posted thank-you notes outside their doors to express their gratitude, which means so much to us,” Mr Chan said.
As the epidemic continued to rage on, the EMSD team actively participated in various anti-epidemic tasks, of which the RTD operations were the most challenging. At the peak of the epidemic, a number of teams of civil servants were required to conduct these operations every day. On average, the EMSD had to arrange a team of more than 150 colleagues to join the RTD operations every week. Participating colleagues were of different ranks and posts under the Regulatory Services and the Electrical and Mechanical Services Trading Fund. Whether they were administrative staff, inspectors or engineers, they became close comrades in these anti-epidemic operations.
“In those days, we often heard colleagues recounting stories about their anti-epidemic work on the hallways in the EMSD Headquarters. Some talked about the difficulties they faced and their hope for the epidemic to die down as soon as possible. We all understood that as part of the anti-epidemic force, we had to remain resilient and committed despite all the challenges and immense pressure ahead.”
“Every operation was very urgent in time and large in scale, involving a number of government departments,” Mr Chan said when he talked about the difficulties in the anti-epidemic work. “We had to arrange for supplies and mobilise manpower within a short period of time. And we could only rely on social media apps to stay connected and complete every operation, in which we would invariably end up with sweat-soaked clothing under the protective gear. As every operation was different and there was no past experience for reference, we had to play by ear and stay vigilant. After each operation, we all enthusiastically shared experience to help improve the efficiency and efficacy of our anti-epidemic work in the future, and to minimise the risk of infection for our colleagues and the impact of such work on the general public.”
“Everyone was surely concerned about their own safety in the face of the rapid development of the fifth wave of the epidemic that time. However, as civil servants, we were determined to stay on the frontline to deliver hot meals to the residents. Though we do not have any direct contact with the residents, some of them posted thank-you notes outside their doors to express their gratitude, which means so much to us,” Mr Chan said.
As the epidemic continued to rage on, the EMSD team actively participated in various anti-epidemic tasks, of which the RTD operations were the most challenging. At the peak of the epidemic, a number of teams of civil servants were required to conduct these operations every day. On average, the EMSD had to arrange a team of more than 150 colleagues to join the RTD operations every week. Participating colleagues were of different ranks and posts under the Regulatory Services and the Electrical and Mechanical Services Trading Fund. Whether they were administrative staff, inspectors or engineers, they became close comrades in these anti-epidemic operations.
“In those days, we often heard colleagues recounting stories about their anti-epidemic work on the hallways in the EMSD Headquarters. Some talked about the difficulties they faced and their hope for the epidemic to die down as soon as possible. We all understood that as part of the anti-epidemic force, we had to remain resilient and committed despite all the challenges and immense pressure ahead.”
“Every operation was very urgent in time and large in scale, involving a number of government departments,” Mr Chan said when he talked about the difficulties in the anti-epidemic work. “We had to arrange for supplies and mobilise manpower within a short period of time. And we could only rely on social media apps to stay connected and complete every operation, in which we would invariably end up with sweat-soaked clothing under the protective gear. As every operation was different and there was no past experience for reference, we had to play by ear and stay vigilant. After each operation, we all enthusiastically shared experience to help improve the efficiency and efficacy of our anti-epidemic work in the future, and to minimise the risk of infection for our colleagues and the impact of such work on the general public.”
Telling Compelling Stories about Gas Safety in Creative Ways
In recent years, we have continued to take forward public education on gas safety by diversified new approaches. In addition to creative and vivid animations and four-panel comic strips for publicity, we have made extensive use of social media platforms to engage the public, and translated the gas safety messages for various ethnic groups in Hong Kong. Ms Chan Wai-sheung, Michelle, an engineer of the Gas Standards Office, is our behind-the-scene “Creative Director” for all these publicity initiatives. She told us that more novel promotions would be coming soon.
As the opportunity for face-to-face contact with the public through visits and outreach programmes was greatly reduced during the epidemic, Ms Chan and her team stepped up their efforts in exploring publicity approaches other than the traditional means and channels, such as more extensive use of creative productions, social media platforms and STEM education to engage people from all walks of life.
Taking forward the new initiatives was not plain sailing, she said, “As ethnic groups in society have always been one of our targets for promotion and education, we have translated the messages on gas safety into various ethnic languages for dissemination to them clearly through online platforms and dedicated radio channels. However, as none of our team members knew the languages of ethnic minorities, the biggest challenge we have faced was how to ensure that the translated messages to be delivered to different ethnic groups were accurate.”
To ensure the translated message was concise and closer to the dialects of these target audiences, the team contacted and visited the consulates of ethnic groups for assistance. The consulate staff were very helpful and worked with our team members to revise the translated texts to ensure that the gas safety messages were clear and engaging.
Keeping up their good efforts, the team is embarking on a new series of innovative outreach programmes, such as interactive storytelling theatres and activities, to extend the promotion of gas safety messages to students and foreign domestic helpers. The team also collaborates with support service centres for ethnic minorities to work out promotion programmes in different forms for engaging more ethnic groups.
Ms Chan said, “We have made use of the subsidies granted under the Job Creation Scheme to recruit young people for the preparation work of the outreach programmes, such as compiling the drama scripts and preparing the materials required for theatrical production. Our team and other colleagues will perform on stage to tell a compelling story about gas safety. We hope that students, foreign domestic helpers and ethnic groups will become the ‘seeds’ for disseminating gas safety messages to their family members, friends and employers.”
Taking forward the new initiatives was not plain sailing, she said, “As ethnic groups in society have always been one of our targets for promotion and education, we have translated the messages on gas safety into various ethnic languages for dissemination to them clearly through online platforms and dedicated radio channels. However, as none of our team members knew the languages of ethnic minorities, the biggest challenge we have faced was how to ensure that the translated messages to be delivered to different ethnic groups were accurate.”
To ensure the translated message was concise and closer to the dialects of these target audiences, the team contacted and visited the consulates of ethnic groups for assistance. The consulate staff were very helpful and worked with our team members to revise the translated texts to ensure that the gas safety messages were clear and engaging.
Keeping up their good efforts, the team is embarking on a new series of innovative outreach programmes, such as interactive storytelling theatres and activities, to extend the promotion of gas safety messages to students and foreign domestic helpers. The team also collaborates with support service centres for ethnic minorities to work out promotion programmes in different forms for engaging more ethnic groups.
Ms Chan said, “We have made use of the subsidies granted under the Job Creation Scheme to recruit young people for the preparation work of the outreach programmes, such as compiling the drama scripts and preparing the materials required for theatrical production. Our team and other colleagues will perform on stage to tell a compelling story about gas safety. We hope that students, foreign domestic helpers and ethnic groups will become the ‘seeds’ for disseminating gas safety messages to their family members, friends and employers.”
When AI Meets Cremation: A Drive for Taking the Industry Forward
Mr Cheung Lap-hung (2nd left), an engineer, Mr Fung Chun-kwok (2nd right), an assistant engineer and the team have developed an award-winning artificial intelligence (AI) Based Image Analytic and Control System for Cremation Process which uses image analytics and AI technology to optimise each cremation session, thus reducing the time required and fuel consumption.
While digitalisation and AI have brought transformational changes in many industries, it remains challenging for the cremation trade to adopt the two since cremation is a traditional business and perceived by some as a taboo subject. Even so, Mr Cheung Lap-hung, an engineer of the Municipal Sector Division, believes that digitalisation is the right path for cremation services because it not only enhances the work efficiency but also releases staff to take on emergency repairs and maintenance, putting their expertise to better use.
He, therefore, has put forward a solution called the AI Based Image Analytic and Control System for Cremation Process or i-Cremation, which won a silver medal at the International Exhibition of Inventions of Geneva 2022.
“We must thank our client the Food and Environmental Hygiene Department and our frontline staff for their support throughout the development process,” Mr Cheung said. The system is being piloted at six cremators at the Wo Hop Shek Crematorium and scheduled to be launched officially by the end of 2023.
Training the AI model is the key. It is also the most time-consuming and costly part of the deployment process. Apart from installing a video camera in each cremator to capture sufficient operational data and cremation status for image analytics, experienced frontline staff must also observe the entire cremation process, which takes about two hours, and provide feedbacks to continuously improve the performance and stability of the AI model. This “training” process has been repeated many times to enhance the AI in the development.
“To enhance staff confidence, we set up a dashboard showing the various real-time operational parameters of i-Cremation in action. Our staff can see for themselves how the AI system simulates and controls all four stages of the cremation process,” he explained. The dashboard has boosted staff confidence as it shows vividly that AI can do the job competently. Furthermore, if anything goes wrong, staff can intervene anytime, demonstrating that human operators still can add value to the cremation work. The team is working on a 2.0 version of the patented i-Cremation, which may be deployed at other crematoria in future.
“We are very delighted to see the changes of this traditional industry by adopting new technologies and innovative ideas,” Mr Cheung concluded. During the development of our project, one of the existing German manufacturers has seen the potential benefit of AI application and has already made an important change in their original cremator design to add video cameras as a standard feature in new projects.
He, therefore, has put forward a solution called the AI Based Image Analytic and Control System for Cremation Process or i-Cremation, which won a silver medal at the International Exhibition of Inventions of Geneva 2022.
“We must thank our client the Food and Environmental Hygiene Department and our frontline staff for their support throughout the development process,” Mr Cheung said. The system is being piloted at six cremators at the Wo Hop Shek Crematorium and scheduled to be launched officially by the end of 2023.
Training the AI model is the key. It is also the most time-consuming and costly part of the deployment process. Apart from installing a video camera in each cremator to capture sufficient operational data and cremation status for image analytics, experienced frontline staff must also observe the entire cremation process, which takes about two hours, and provide feedbacks to continuously improve the performance and stability of the AI model. This “training” process has been repeated many times to enhance the AI in the development.
“To enhance staff confidence, we set up a dashboard showing the various real-time operational parameters of i-Cremation in action. Our staff can see for themselves how the AI system simulates and controls all four stages of the cremation process,” he explained. The dashboard has boosted staff confidence as it shows vividly that AI can do the job competently. Furthermore, if anything goes wrong, staff can intervene anytime, demonstrating that human operators still can add value to the cremation work. The team is working on a 2.0 version of the patented i-Cremation, which may be deployed at other crematoria in future.
“We are very delighted to see the changes of this traditional industry by adopting new technologies and innovative ideas,” Mr Cheung concluded. During the development of our project, one of the existing German manufacturers has seen the potential benefit of AI application and has already made an important change in their original cremator design to add video cameras as a standard feature in new projects.
Developing an I&T Solution for Maximising Performance of Solar PV Systems
Ms Cheung Man-chit, Jovian, a senior engineer of the Energy Efficiency Office, previously discovered that no device on the market could objectively and scientifically measure the power generation performance of a solar photovoltaic (PV) system. Therefore, she took the lead in developing the Integrated Solar Energy Performance Management Toolkit.
Ms Cheung collaborated with the Hong Kong Polytechnic University to develop the novel Integrated Solar Energy Performance Management Toolkit (iSMS). Leveraging artificial intelligence and digital twin technology while making reference to the performance of nearby solar PV systems, the iSMS estimates the power generation performance of solar PV systems and predicts the timing of necessary system maintenance.
The iSMS measures factors affecting the power generation performance, such as the coverage of shading, dust and bird excrement on a solar panel. Based on the data, the iSMS reminds owners of solar energy generating facilities to clean the solar PV panels in order to harness more solar energy and maximise power generation performance, so that the maximum Feed-in Tariff (FiT) income of the facilities’ owners will be secured.
When the iSMS detects that a facility is due for repair or maintenance, it will issue an alert and recommend the timing for preventive maintenance. This function is particularly useful for monitoring facilities at hard-to-reach places, such as floating photovoltaic panels.
“To address climate change, the Government encourages the public to install solar PV systems. If solar PV systems can maintain optimal performance and deliver a better FiT return to facilities’ owners, the public will respond more positively to such renewable energy projects. Ultimately, it will help Hong Kong achieve the target of carbon neutrality,” Ms Cheung said.
The iSMS is now patented in Hong Kong and have won a bronze medal in the International Exhibition of Inventions of Geneva 2022, exemplifying the recognition for our I&T achievements.
The iSMS measures factors affecting the power generation performance, such as the coverage of shading, dust and bird excrement on a solar panel. Based on the data, the iSMS reminds owners of solar energy generating facilities to clean the solar PV panels in order to harness more solar energy and maximise power generation performance, so that the maximum Feed-in Tariff (FiT) income of the facilities’ owners will be secured.
When the iSMS detects that a facility is due for repair or maintenance, it will issue an alert and recommend the timing for preventive maintenance. This function is particularly useful for monitoring facilities at hard-to-reach places, such as floating photovoltaic panels.
“To address climate change, the Government encourages the public to install solar PV systems. If solar PV systems can maintain optimal performance and deliver a better FiT return to facilities’ owners, the public will respond more positively to such renewable energy projects. Ultimately, it will help Hong Kong achieve the target of carbon neutrality,” Ms Cheung said.
The iSMS is now patented in Hong Kong and have won a bronze medal in the International Exhibition of Inventions of Geneva 2022, exemplifying the recognition for our I&T achievements.
Supporting RTD Operations with Heart and Technologies
In March 2022, the EMSD co-ordinated and led "restriction-testing declaration" (RTD) operations, which entailed overall planning and co-ordination, information technology system support and logistics management. Thanks to the staunch support and high esprit de corps displayed by our Digitalisation and Technology Division, Corporate Services Division and other divisions, as well as various government departments, these joint operations were carried out smoothly.
Early 2022 was memorable for many EMSTF colleagues who participated in the “restriction-testing declaration” (RTD) operations, an important element of Hong Kong’s fight against the epidemic. Among the participants were Mr Lai Chun-fai, Alex and Mr Chan Sze-nok, Donald, both senior engineers of the Digitalisation and Technology Division (DTD), and Ms Ng Ka-pik, Cindy, the chief supplies officer of the Supplies Sub-division.
As only a few days’ notice was given to the team for its first-ever RTD operation conducted at Tak Ying House in Tak Long Estate on 3 and 4 March, Ms Ng had to race against time to procure adequate supplies within a very short period of time. These included personal protective equipment and rapid antigen test kits for colleagues, as well as Chinese medicine packs and canned food for households in the target building. “We always keep two sets of supplies, one for the immediate RTD operation and the other as stand-by for the next one,” Ms Ng explained.
Mr Lai and Mr Chan recalled their key tasks in the operation. “On Day One, we knocked on the door of each household to inform the residents to go downstairs for nucleic acid tests; on Day Two, we called those who tested positive by phone for follow-up, checked whether the residents had already obtained a negative test result before allowing them to leave the restricted area, and re-opened the restricted area by noon finally.” Many challenges arose in the operation, one of them was data mapping. The testing contractor only had the identity card, mobile phone and reference numbers of those being tested, but did not have the crucial information such as to which households they belonged, thus making it difficult for the responsible colleagues to follow up on the positive cases. Fortunately, the team was able to draw on the rich information technology (IT) expertise of the EMSD to promptly complete the data mapping, so that follow-up action could be carried out smoothly.
“Given the complex and mammoth operation, and the need to work with unfamiliar staff from different departments, we are glad that working with high team spirit, we got all the difficult tasks done,” Mr Chan said.
“We are grateful that our colleagues were so accommodating and that the residents were supportive of our work,” Mr Lai added.
Mr Lee Che-kit, the chief engineer of the DTD, led the RTD operation at Yau Oi Estate on 9 and 10 March as the deputy field-commander. “In this operation, we alerted the testing contractor that the information they obtained from the residents was insufficient for following up on the positive cases,” he said. The insight prompted the contractor to obtain more information required from the residents, making subsequent RTD operations more efficient.
As only a few days’ notice was given to the team for its first-ever RTD operation conducted at Tak Ying House in Tak Long Estate on 3 and 4 March, Ms Ng had to race against time to procure adequate supplies within a very short period of time. These included personal protective equipment and rapid antigen test kits for colleagues, as well as Chinese medicine packs and canned food for households in the target building. “We always keep two sets of supplies, one for the immediate RTD operation and the other as stand-by for the next one,” Ms Ng explained.
Mr Lai and Mr Chan recalled their key tasks in the operation. “On Day One, we knocked on the door of each household to inform the residents to go downstairs for nucleic acid tests; on Day Two, we called those who tested positive by phone for follow-up, checked whether the residents had already obtained a negative test result before allowing them to leave the restricted area, and re-opened the restricted area by noon finally.” Many challenges arose in the operation, one of them was data mapping. The testing contractor only had the identity card, mobile phone and reference numbers of those being tested, but did not have the crucial information such as to which households they belonged, thus making it difficult for the responsible colleagues to follow up on the positive cases. Fortunately, the team was able to draw on the rich information technology (IT) expertise of the EMSD to promptly complete the data mapping, so that follow-up action could be carried out smoothly.
“Given the complex and mammoth operation, and the need to work with unfamiliar staff from different departments, we are glad that working with high team spirit, we got all the difficult tasks done,” Mr Chan said.
“We are grateful that our colleagues were so accommodating and that the residents were supportive of our work,” Mr Lai added.
Mr Lee Che-kit, the chief engineer of the DTD, led the RTD operation at Yau Oi Estate on 9 and 10 March as the deputy field-commander. “In this operation, we alerted the testing contractor that the information they obtained from the residents was insufficient for following up on the positive cases,” he said. The insight prompted the contractor to obtain more information required from the residents, making subsequent RTD operations more efficient.
Refurbishing World-class Escalator with a Big Heart
During the refurbishment works, Mr Ho Chun-to, James, an engineer, was committed to maintaining good communication with members of the public. He handled public enquiries with patience and closely monitored and followed up on the works progress, with a view to minimising the impact on the daily lives of the public.
The 800-metre Central to Mid-Levels Escalator and Walkway System (the System) is the longest covered outdoor escalator in the world. In 2018, the System underwent refurbishment works. As the service life of all the 19 escalators and walkways of the System had been expired then, all of them had to be replaced. The four-year refurbishment works were carried out in 11 phases. It is expected that all the works will be completed and the System fully re-opened by April 2022 for public use.
Two years into the project, Mr Ho Chun-to, James, an engineer of the Boundary Crossing Facilities and Transport Services Division, joined the team responsible for the refurbishment of the System in January 2020. Mr Ho and the team actively co-ordinated with the Transport Department, the project client, as well as other government departments, including the Home Affairs Department and Hong Kong Police Force, to tackle myriad challenges. For example, the team had to ensure that the works will not affect the existing canopies of the System. Moreover, the narrow streets along the System added difficulties to the works, as truck-mounted cranes needed to be deployed for lifting operations while disruption to vehicle and pedestrian traffic had to be minimised. In addition, the team had to solicit support from the local community, composing of different residents and commercial tenants with diverse cultural background.
To facilitate smooth implementation of the project, the team adopted the approach of closing relevant road sections for an hour every day for replacement works, with an aim to minimising the traffic impacts. On one occasion, a seriously ill elderly person on a car going to seek medical treatment could not continue the way due to the road closure; on another occasion, a car carrying a pet in critical condition was obstructed. On both occasions, the team immediately re-opened the closed road section to cater for the urgent need. In another instance in early 2021, when the Drainage Services Department put in a last-minute request for urgent access to a manhole in a closed road section to take underground sewage samples for COVID-19 testing, our staff also made arrangements at once to allow the officers concerned to enter the area. “These examples show our flexibility and adaptability in various situations with caring attitude with regard to the needs of the community,” Mr Ho said.
With careful planning and hard work, the time lost for temporary road re-opening did not cause any major delay in the project. Mr Ho also said that working on the project, he gained much experience in handling public enquiries and complaints, and has become more patient, enabling him to overcome similar challenges with ease in the future. Looking back at the implementation of the project, he would like to thank his team for their support and the community for its forbearance.
Two years into the project, Mr Ho Chun-to, James, an engineer of the Boundary Crossing Facilities and Transport Services Division, joined the team responsible for the refurbishment of the System in January 2020. Mr Ho and the team actively co-ordinated with the Transport Department, the project client, as well as other government departments, including the Home Affairs Department and Hong Kong Police Force, to tackle myriad challenges. For example, the team had to ensure that the works will not affect the existing canopies of the System. Moreover, the narrow streets along the System added difficulties to the works, as truck-mounted cranes needed to be deployed for lifting operations while disruption to vehicle and pedestrian traffic had to be minimised. In addition, the team had to solicit support from the local community, composing of different residents and commercial tenants with diverse cultural background.
To facilitate smooth implementation of the project, the team adopted the approach of closing relevant road sections for an hour every day for replacement works, with an aim to minimising the traffic impacts. On one occasion, a seriously ill elderly person on a car going to seek medical treatment could not continue the way due to the road closure; on another occasion, a car carrying a pet in critical condition was obstructed. On both occasions, the team immediately re-opened the closed road section to cater for the urgent need. In another instance in early 2021, when the Drainage Services Department put in a last-minute request for urgent access to a manhole in a closed road section to take underground sewage samples for COVID-19 testing, our staff also made arrangements at once to allow the officers concerned to enter the area. “These examples show our flexibility and adaptability in various situations with caring attitude with regard to the needs of the community,” Mr Ho said.
With careful planning and hard work, the time lost for temporary road re-opening did not cause any major delay in the project. Mr Ho also said that working on the project, he gained much experience in handling public enquiries and complaints, and has become more patient, enabling him to overcome similar challenges with ease in the future. Looking back at the implementation of the project, he would like to thank his team for their support and the community for its forbearance.
Guardians of Good Ventilation amid the Epidemic
In response to the clusters of infection cases in many restaurants during the outbreak of the fifth wave of the epidemic, Ms Kwan Ho-yu, Lillian (middle), an engineer and her team actively examined the ventilation systems of related restaurants and provided professional advice and support to client departments.
Maintaining good ventilation in dine-in restaurants is crucial for infection prevention and control amid the epidemic. Since the onset of COVID-19, clusters of infection cases have been detected in a number of restaurants in Hong Kong. Ms Kwan Ho-yu, Lillian, an engineer of the Municipal Sector Division and Mr Chan Man-tak, an inspector of the same division, have actively supported the Government’s ventilation investigations at restaurants with COVID-19 outbreaks, thus accumulating abundant experience in this area of work. In late December 2021, a cluster of infection cases at a Chinese restaurant in the Festival Walk triggered the fifth wave of the epidemic. Ms Kwan and her team went to the scene to examine the ventilation system of the restaurant and provided technical support to the Centre for Health Protection (CHP) and the Food and Environmental Hygiene Department. She and her team have subsequently been called upon to investigate the ventilation systems at a number of restaurants.
“As each restaurant was different in its ventilation design and the investigation had to be conducted urgently, we encountered numerous difficulties initially, such as being unable to identify the exact location of the fresh air intake,” Ms Kwan said. That means teamwork would be more important than ever. She was really grateful for the staunch support rendered by her team members. For example, her inspectorate colleagues usually had to climb up high near the ceiling to remove dust-covered air vent covers for the team to measure air changes per hour (ACH).
Mr Chan, one of Ms Kwan’s team members, has participated in numerous investigations of ventilation systems since the epidemic began in 2020. His work included measuring ACH to ascertain if the amount of fresh air was sufficient, and contacting the persons-in-charge of the restaurant for details such as the exact size and configuration of each section of the restaurants.
“Together with the persons-in-charge, we tried to reconstruct the virus transmission scenarios by conducting smoke tests at the seats of the confirmed patients to simulate the most likely airflow patterns during the virus transmission for the CHP’s reference,” he said.
Ms Kwan and Mr Chan have also helped draw up ventilation guidelines for restaurants and residential care homes for the elderly for operators’ reference. When these venues have completed the requisite improvement works based on the ventilation investigation results, input and re-assessment of the team are required prior to their re-opening.
“Ventilation can be a matter of life and death, especially for the elderly, amid the epidemic. It is our duty to join in the fight against the epidemic. We are delighted to be of help,” both said in unison.
“As each restaurant was different in its ventilation design and the investigation had to be conducted urgently, we encountered numerous difficulties initially, such as being unable to identify the exact location of the fresh air intake,” Ms Kwan said. That means teamwork would be more important than ever. She was really grateful for the staunch support rendered by her team members. For example, her inspectorate colleagues usually had to climb up high near the ceiling to remove dust-covered air vent covers for the team to measure air changes per hour (ACH).
Mr Chan, one of Ms Kwan’s team members, has participated in numerous investigations of ventilation systems since the epidemic began in 2020. His work included measuring ACH to ascertain if the amount of fresh air was sufficient, and contacting the persons-in-charge of the restaurant for details such as the exact size and configuration of each section of the restaurants.
“Together with the persons-in-charge, we tried to reconstruct the virus transmission scenarios by conducting smoke tests at the seats of the confirmed patients to simulate the most likely airflow patterns during the virus transmission for the CHP’s reference,” he said.
Ms Kwan and Mr Chan have also helped draw up ventilation guidelines for restaurants and residential care homes for the elderly for operators’ reference. When these venues have completed the requisite improvement works based on the ventilation investigation results, input and re-assessment of the team are required prior to their re-opening.
“Ventilation can be a matter of life and death, especially for the elderly, amid the epidemic. It is our duty to join in the fight against the epidemic. We are delighted to be of help,” both said in unison.
Going Above and Beyond to Avert Auto-LPG Supply Shortage Crisis
The supply of liquefied petroleum gas (LPG) had been generally stable in Hong Kong, but it was almost disrupted in the fourth quarter of 2021 when LPG vessels transporting LPG to Hong Kong from Zhuhai and Dongguan were severely delayed due to the collective impact of COVID-19, international shipping bottlenecks and typhoons, putting Hong Kong on the verge of a LPG shortage. In view of the imminent plight then, Mr Lam Heung-chung, Marco, an engineer of the Gas Standards Office in charge of regulating LPG filling stations, LPG vehicles and gas safety, reacted immediately by coordinating the collaboration among companies in the trade and seeking help from the Mainland, and hence resolved the crisis promptly.
At that time, Mr Lam and his team learned that certain auto-LPG supply companies only had a few days of inventory left, and some LPG filling stations might have to suspend operation if replenishment could not be made in time. This could upset the normal operation of more than 20 000 taxis and light buses across the territory.
To deal with the emergency, the team went above and beyond its gas safety regulatory duties and held an urgent meeting with all gas supply companies to gauge the territory-wide LPG inventory and daily consumption rate, so as to work out informed solutions and ensure stable LPG supply for taxis and light buses.
As immediate action was vital, the team promptly coordinated with local gas supply companies within a tight time frame and successfully facilitated an inventory-on-loan arrangement among suppliers in the nick of time, on the night before the inventory of the LPG filling stations concerned was totally depleted. The arrangement ensured that all LPG filling stations could maintain normal LPG filling services the following day and in the immediate period afterwards.
At the same time, the team sought assistance directly from the co-operating counterparts in the Greater Bay Area. Through the Guangdong Provincial Association for Science and Technology, they contacted the Department of Transport of Guangdong Province and explained in writing the next day the LPG supply crisis in Hong Kong. Upon coordination of the Mainland departments, Hong Kong LPG vessels were given priority for entering and departing from the Mainland ports, and finally LPG was shipped to Hong Kong for replenishment in time.
“The crisis was resolved thanks to the gas supply companies’ mutual support, the swift assistance of the Mainland departments and the team’s collective efforts. By December, local auto-LPG supply has been returned to normal. After the incident, the acute situation that night often springs to mind when I take a taxi. That’s why I often chat with taxi drivers to find out which stations they go for refuelling, the auto-LPG prices and queuing time, so as to learn more about their daily operation. The experience of the emergency has endowed me with a stronger sense of mission and greater dedication to my work.”
To deal with the emergency, the team went above and beyond its gas safety regulatory duties and held an urgent meeting with all gas supply companies to gauge the territory-wide LPG inventory and daily consumption rate, so as to work out informed solutions and ensure stable LPG supply for taxis and light buses.
As immediate action was vital, the team promptly coordinated with local gas supply companies within a tight time frame and successfully facilitated an inventory-on-loan arrangement among suppliers in the nick of time, on the night before the inventory of the LPG filling stations concerned was totally depleted. The arrangement ensured that all LPG filling stations could maintain normal LPG filling services the following day and in the immediate period afterwards.
At the same time, the team sought assistance directly from the co-operating counterparts in the Greater Bay Area. Through the Guangdong Provincial Association for Science and Technology, they contacted the Department of Transport of Guangdong Province and explained in writing the next day the LPG supply crisis in Hong Kong. Upon coordination of the Mainland departments, Hong Kong LPG vessels were given priority for entering and departing from the Mainland ports, and finally LPG was shipped to Hong Kong for replenishment in time.
“The crisis was resolved thanks to the gas supply companies’ mutual support, the swift assistance of the Mainland departments and the team’s collective efforts. By December, local auto-LPG supply has been returned to normal. After the incident, the acute situation that night often springs to mind when I take a taxi. That’s why I often chat with taxi drivers to find out which stations they go for refuelling, the auto-LPG prices and queuing time, so as to learn more about their daily operation. The experience of the emergency has endowed me with a stronger sense of mission and greater dedication to my work.”
A New Chapter on Conservation Education: Compiling STEAM Educational Kit on Solar Harvest for Primary Schools
In a bid to promote the use of renewable energy (RE), the EMSD not only helps eligible schools install solar energy generation systems through Solar Harvest, but also compiles a STEAM educational kit to stimulate students’ interest in scientific learning and deepen their understanding of RE and strategies regarding climate change. Taking on the new challenge boldly, Mr Lam Tung-him, Alex, an assistant engineer of the Energy Efficiency Office, stepped out of his comfort zone of E&M engineering and committed to the compilation of educational kit, an area that was totally new to him.
Mr Lam co-ordinated and led a curriculum development team from the University of Hong Kong to compile for primary schools the first STEAM educational kit, with a total of eight themes, on Solar Harvest. In the process, Mr Lam maintained close communication with the working group, comprising representatives from the then Environment Bureau, Education Bureau (EDB) and EMSD, as well as school teachers and consultants, formed for the compilation of the teaching materials. Completed in a meticulous compilation process, the STEAM educational kit has been approved by the EDB as teaching materials under the primary school curriculum.
The kit comes in two sets separately for junior and senior primary school levels. Each set comprises materials designed for teachers and students respectively, worksheets, a list of materials to be procured by schools for STEAM activities, frequently asked questions and educational videos. The content is written in simple language and full of interactive elements. At every stage of the curriculum, there are hands-on activities for students to make solar-powered handicrafts after learning the relevant theories. Guided by the EMSD mascots, students will also be taken on virtual reality tours of solar energy generation facilities.
“The EMSD is the gatekeeper of technical information of the teaching materials. Coupled with the approval of the EDB as being suitable for the primary school curriculum, the educational kit is highly authoritative. Upon its launch, teachers can flexibly use the high-quality and approved educational kit for teaching based on students’ level and teaching progress, without having to search for other teaching materials. Students can also pick up the knowledge about RE from the basics at a young age. I find this job really meaningful,” Mr Lam said.
The educational kit will be introduced in the 2022/23 academic year. Primary school teachers may browse the EMSD webpage on Solar Harvest anytime to access the educational kit. Schools participating in Solar Harvest with solar energy generation systems connected on-grid can access the Real-time Monitoring System through the Virtual Reality learning platform such that the students can browse the electricity generated by schools’ solar energy generation systems in real time. The introduction of the education kit will mark a new chapter of RE education in Hong Kong.
Mr Lam and his team has begun the compilation of an education kit on Solar Harvest for secondary schools, with separate content for junior and senior secondary levels to align with the Science curriculum for junior secondary levels, and Physics curriculum for senior secondary levels. More technical information will be included in the kit too to suit the level of secondary students.
The kit comes in two sets separately for junior and senior primary school levels. Each set comprises materials designed for teachers and students respectively, worksheets, a list of materials to be procured by schools for STEAM activities, frequently asked questions and educational videos. The content is written in simple language and full of interactive elements. At every stage of the curriculum, there are hands-on activities for students to make solar-powered handicrafts after learning the relevant theories. Guided by the EMSD mascots, students will also be taken on virtual reality tours of solar energy generation facilities.
“The EMSD is the gatekeeper of technical information of the teaching materials. Coupled with the approval of the EDB as being suitable for the primary school curriculum, the educational kit is highly authoritative. Upon its launch, teachers can flexibly use the high-quality and approved educational kit for teaching based on students’ level and teaching progress, without having to search for other teaching materials. Students can also pick up the knowledge about RE from the basics at a young age. I find this job really meaningful,” Mr Lam said.
The educational kit will be introduced in the 2022/23 academic year. Primary school teachers may browse the EMSD webpage on Solar Harvest anytime to access the educational kit. Schools participating in Solar Harvest with solar energy generation systems connected on-grid can access the Real-time Monitoring System through the Virtual Reality learning platform such that the students can browse the electricity generated by schools’ solar energy generation systems in real time. The introduction of the education kit will mark a new chapter of RE education in Hong Kong.
Mr Lam and his team has begun the compilation of an education kit on Solar Harvest for secondary schools, with separate content for junior and senior secondary levels to align with the Science curriculum for junior secondary levels, and Physics curriculum for senior secondary levels. More technical information will be included in the kit too to suit the level of secondary students.
“E&M Detective” Overcoming Challenges Rarely Known in Conducting In-depth Investigation of Electrical Incidents
Every year, the EMSD investigates over 400 suspected electrical incidents on average, and over 100 of them are confirmed to be related to electricity after investigation. Overcoming manifold difficulties rarely known to people with his rich experience, Mr Lam Wai-kei, a chief technical officer of the Electricity Legislation Division (ELD) thoroughly examines the electricity supply systems and appliances at the incident site in each investigation, in order to identify incident causes for the deceased or victims, as well as spotting various risks of electrical incidents with a view to strengthening relevant promotion and education efforts on electrical safety.
Mr Lam recalled that there was, in 2016, a home electrocution incident, in which a scoring engineer died of electrocution while bathing in a village house. At that time, the investigation team Mr Lam led checked every electrical appliance and all wiring in the house. Nevertheless, after more than 18 hours of work at site, the team still could not find any installation with electricity leakage problem. It was only after repeated thorough site inspection that he found out that a nearby house, which was used as a studio and about 100 metres away from the house concerned, had a non-compliant extension cord connected to the material house to obtain power supply. A wrongly wired lamp that was plugged into the extension cord caused electricity leakage and the electric current was transmitted through the earthing wire to the accidentally connected water pipes of the bathroom of the material house. Coupled with the lack of a residual current circuit breaker and effective earth connection in the material house, the fatal incident eventually occurred.
During the investigation of electrical incidents, the experience and knowledge in electrical systems of the EMSD’s investigators are certainly vital, but their ability to withstand psychological and physical stress should not be overlooked. “For instance, we are sometimes required to examine and collect evidence from the electrical appliances and power supply systems at perilous fire scenes, where the bodies of the deceased have not yet been removed, to determine if the fires are caused by electrical incidents,” Mr Lam said.
It is only human to be apprehensive working in the material places of incidents or accidents. “To ease my mind, I often remind myself that I’m there to find the causes of incidents for the deceased and victims. During duty months, it is difficult to have a deep sleep as I may be called for operation in the middle of the night. We also have to prioritise when there are five to six electricity-related cases in a single day. Furthermore, as evidence collection takes time and sometimes we have to work in remote areas, we have to be flexible with colleagues’ personal needs, such as meal-taking and bathroom visits. Such are the untold trials and tribulations of the work in the ELD,” Mr Lam said.
Mr Lam told us that the occurrence of electrical incidents was often attributed to the coincidence of three elements, which were a faulty protection device, electrical appliance breakdown or damage and improper use of electrical appliances. He cited an example in which a resident casually placed a hairdryer still hot after use on the mattress made of flammable materials, causing the mattress to catch fire due to overheating.
“Many incidents are actually avoidable. All it takes is cutting the power supply to all electrical appliances or charging devices before leaving home; cleaning refrigerators and washing machines regularly to avoid fire accidents caused by sparks from an operating machine igniting the gathered dust; and unplugging idle appliances. These daily habits are simple yet helpful for ensuring electrical safety,” Mr Lam said.
During the investigation of electrical incidents, the experience and knowledge in electrical systems of the EMSD’s investigators are certainly vital, but their ability to withstand psychological and physical stress should not be overlooked. “For instance, we are sometimes required to examine and collect evidence from the electrical appliances and power supply systems at perilous fire scenes, where the bodies of the deceased have not yet been removed, to determine if the fires are caused by electrical incidents,” Mr Lam said.
It is only human to be apprehensive working in the material places of incidents or accidents. “To ease my mind, I often remind myself that I’m there to find the causes of incidents for the deceased and victims. During duty months, it is difficult to have a deep sleep as I may be called for operation in the middle of the night. We also have to prioritise when there are five to six electricity-related cases in a single day. Furthermore, as evidence collection takes time and sometimes we have to work in remote areas, we have to be flexible with colleagues’ personal needs, such as meal-taking and bathroom visits. Such are the untold trials and tribulations of the work in the ELD,” Mr Lam said.
Mr Lam told us that the occurrence of electrical incidents was often attributed to the coincidence of three elements, which were a faulty protection device, electrical appliance breakdown or damage and improper use of electrical appliances. He cited an example in which a resident casually placed a hairdryer still hot after use on the mattress made of flammable materials, causing the mattress to catch fire due to overheating.
“Many incidents are actually avoidable. All it takes is cutting the power supply to all electrical appliances or charging devices before leaving home; cleaning refrigerators and washing machines regularly to avoid fire accidents caused by sparks from an operating machine igniting the gathered dust; and unplugging idle appliances. These daily habits are simple yet helpful for ensuring electrical safety,” Mr Lam said.
Inspecting the First Public Inclined Lift System in Hong Kong as the Gatekeeper for Safety
Two inclined lifts connecting Kwai Chung Estate and Wo Tong Tsui Street were completed in February 2022. Mr Leung Wai-yin, an inspector of the General Legislation Division, conducted the final inspection on the lifts as required by the legislation to confirm their safety, completing a crucial step before use permits were issued. Since the lifts commenced operation in April 2022, residents of Kwai Chung Estate can travel easily without having to climb more than a hundred steps.
The first public covered inclined lift system in Hong Kong, which is about 36-metre long, has two inclined lifts plying at a speed of 1.5 metres per second on the 30-degree slope between Wo Tong Tsui Street and Tai Wo Hau Road, with a journey time of less than one minute. Each lift can carry 24 passengers and has a loading capacity of 1 800 kg. The lifts are expected to have a daily patronage of 8 600 passenger trips every day, bringing great convenience to residents of the area.
Mr Leung remarked that inclined lifts are convenient for the use of the elderly and wheelchair users and can better meet the needs of the population in that area, hence they are more suitable than escalators for installation at the above location.
There are huge technical differences in inspecting inclined lifts and vertical lifts. “For inclined lifts, safety components such as traction machines, overspeed governors and brakes, are installed upside down or at an angle, and the tension and traction of each suspension rope that propels the lift car must be the same. Besides, due to the traction direction of inclined lifts and the inclination of their car guide rails, the car guide rails of inclined lifts must bear part of the car weight, whereas that of vertical lifts only control the up or down direction of the lift, which is relatively simpler,” Mr Leung explained.
In addition to testing the components, Mr Leung took the lift during the inspection to experience the lift operation as a user, with a view to figuring out how to improve passenger experience during lift acceleration and deceleration. “From past experience, most escalator incidents were caused by passengers who lost balance and fell over due to their failure to hold the handrail tightly, while most lift incidents involved passenger tripping due to levelling difference of the lift car at landing. In view of this, safety announcements will be broadcast before the cars of the inclined lift system arrive at or depart from the landing, to remind passengers to mind the lift door and hold the handrail tightly,” he said.
After the inclined lifts were put into service, Mr Leung made a point of taking the lifts whenever he worked in the neighbourhood to see if they were working properly. “Taking the lifts makes me aware of any wear and tear in the guide rails causing unstable car movement,” he said. Mr Leung’s commitment to serving the community naturally shone through in his words.
Mr Leung remarked that inclined lifts are convenient for the use of the elderly and wheelchair users and can better meet the needs of the population in that area, hence they are more suitable than escalators for installation at the above location.
There are huge technical differences in inspecting inclined lifts and vertical lifts. “For inclined lifts, safety components such as traction machines, overspeed governors and brakes, are installed upside down or at an angle, and the tension and traction of each suspension rope that propels the lift car must be the same. Besides, due to the traction direction of inclined lifts and the inclination of their car guide rails, the car guide rails of inclined lifts must bear part of the car weight, whereas that of vertical lifts only control the up or down direction of the lift, which is relatively simpler,” Mr Leung explained.
In addition to testing the components, Mr Leung took the lift during the inspection to experience the lift operation as a user, with a view to figuring out how to improve passenger experience during lift acceleration and deceleration. “From past experience, most escalator incidents were caused by passengers who lost balance and fell over due to their failure to hold the handrail tightly, while most lift incidents involved passenger tripping due to levelling difference of the lift car at landing. In view of this, safety announcements will be broadcast before the cars of the inclined lift system arrive at or depart from the landing, to remind passengers to mind the lift door and hold the handrail tightly,” he said.
After the inclined lifts were put into service, Mr Leung made a point of taking the lifts whenever he worked in the neighbourhood to see if they were working properly. “Taking the lifts makes me aware of any wear and tear in the guide rails causing unstable car movement,” he said. Mr Leung’s commitment to serving the community naturally shone through in his words.
An Innovative Tool Developed for Estimating FiT Payback
The Government introduced the Feed-in Tariff (FiT) Scheme to incentivise the private sector to install solar photovoltaic (PV) systems. However, how can members of the public estimate the solar power generation potential of their building rooftops and the FiT income concerned before installation? To this end, Ms Wong San-san, an engineer of the Energy Efficiency Office, coordinated the development of the Hong Kong Solar Irradiation Map (the Map) to provide reliable data for the public to make preliminary estimation.
The Map uses the Airborne Light Detection and Ranging data released by the Civil Engineering and Development Department and the GeoInfo Map provided by the Lands Department to build a digital surface model, and simulates the impact of factors such as buildings nearby and topography on solar irradiation with the aid of the 10-year solar irradiation data provided by the Hong Kong Observatory, so as to calculate the annual solar irradiation received at every building rooftop across the city. Such calculation has an accuracy rate of over 90%.
Those interested in setting up solar PV systems can draw the rooftop area intended for installation of a solar PV system on the Map. The Map will automatically calculate the generation capacity of the selected area and the corresponding FiT income. Members of the public can also use the payback calculator in the Map to obtain an estimation of the payback period.
The Map won a silver medal in the International Exhibition of Inventions of Geneva 2022. Ms Wong believed that the Map stood out because it integrated data from multiple dimensions, including geography, astronomy and surveying, and it was the first map which showed the solar irradiation of all building rooftops across the territory.
“Currently there aren’t many similar solar irradiation maps in the world, and most of them do not have calculation functions,” Ms Wong said. “The Hong Kong Solar Irradiation Map is the fruit of our research and development efforts in collaboration with the Hong Kong Polytechnic University, as well as an embodiment of the synergy of inter-departmental co-operation. During its development, I have learned a lot from other departments and greatly benefited.”
Those interested in setting up solar PV systems can draw the rooftop area intended for installation of a solar PV system on the Map. The Map will automatically calculate the generation capacity of the selected area and the corresponding FiT income. Members of the public can also use the payback calculator in the Map to obtain an estimation of the payback period.
The Map won a silver medal in the International Exhibition of Inventions of Geneva 2022. Ms Wong believed that the Map stood out because it integrated data from multiple dimensions, including geography, astronomy and surveying, and it was the first map which showed the solar irradiation of all building rooftops across the territory.
“Currently there aren’t many similar solar irradiation maps in the world, and most of them do not have calculation functions,” Ms Wong said. “The Hong Kong Solar Irradiation Map is the fruit of our research and development efforts in collaboration with the Hong Kong Polytechnic University, as well as an embodiment of the synergy of inter-departmental co-operation. During its development, I have learned a lot from other departments and greatly benefited.”
Rising to the Air-Conditioning Challenge in Activating Large COVID-19 Treatment Centres Promptly
Amid the epidemic, Mr Wong Tat-tong, Victor, an engineer, led his team to support the re-configuration of the ventilation and air-conditioning system at the Treatment Centre for COVID-19 in the AsiaWorld-Expo. Exerting substantive expertise and experience, the team successfully completed the task of converting related halls into negative pressure wards under a very tight schedule.
In this epidemic, Mr Wong Tat-tong, Victor, an engineer of the Health Sector Division, has been dedicated to the establishment of large scale treatment centres. Starting from August 2020, he assisted the Hospital Authority (HA) and Architectural Services Department to swiftly convert four exhibition halls at the AsiaWorld-Expo (AWE) into a community treatment facility with a negative pressure environment, which commenced operation subsequently in October the same year. When the fifth wave of the epidemic broke out in early 2022, Mr Wong was tasked with the urgent work of converting the venue at AWE into a Treatment Centre for COVID-19 for treating a large number of confirmed patients.
Talking about the key challenge in the AWE project, Mr Wong said it was the existing air-conditioning system, which ran on a thermal energy storage system with ice storage features, as it was originally designed to maximise energy efficiency at a venue that did not have to operate 24 hours a day. While the Treatment Centre would operate 24 hours a day, Mr Wong’s team had to modify the system to provide round-the-clock air-conditioning. The solution was to add chillers, and re-configure the system by increasing the number of air-handling units.
At the outbreak of the fifth wave of the epidemic, Mr Wong helped the HA again in converting another hall in the AWE and setting up the Treatment Centre for COVID-19 for receiving confirmed patients with mild symptoms, so that public hospitals could focus on taking care of severe cases. “Time was really tight, and more than 100 new air purifiers had to be ready,” he recalled the situation then. “We all join the hands-on work, including cutting air filters to the right size for the air purifiers late into the night. After several days of overnight work, all conversion works were eventually completed before the deadline.”
The re-configured air-conditioning system worked well and created a negative pressure environment for the entire Treatment Centre, but Mr Wong soon noted another complication. While the elderly, who were sensitive to cold air, often asked to raise the temperature setting, staff working in the halls preferred cooler temperatures as they had full personal protective equipment on. It was important to strike a balance among different needs by fine-tuning the system from time to time.
Striving for excellence, Mr Wong always seeks to improve the air-conditioning system. “We hope to develop a technical solution, which will enable the air-conditioning system to quickly switch between running on a thermal energy storage system and operating on a round-the-clock basis for emergencies, just by tapping a button,” Mr Wong indicated he would continue to work towards this goal.
Talking about the key challenge in the AWE project, Mr Wong said it was the existing air-conditioning system, which ran on a thermal energy storage system with ice storage features, as it was originally designed to maximise energy efficiency at a venue that did not have to operate 24 hours a day. While the Treatment Centre would operate 24 hours a day, Mr Wong’s team had to modify the system to provide round-the-clock air-conditioning. The solution was to add chillers, and re-configure the system by increasing the number of air-handling units.
At the outbreak of the fifth wave of the epidemic, Mr Wong helped the HA again in converting another hall in the AWE and setting up the Treatment Centre for COVID-19 for receiving confirmed patients with mild symptoms, so that public hospitals could focus on taking care of severe cases. “Time was really tight, and more than 100 new air purifiers had to be ready,” he recalled the situation then. “We all join the hands-on work, including cutting air filters to the right size for the air purifiers late into the night. After several days of overnight work, all conversion works were eventually completed before the deadline.”
The re-configured air-conditioning system worked well and created a negative pressure environment for the entire Treatment Centre, but Mr Wong soon noted another complication. While the elderly, who were sensitive to cold air, often asked to raise the temperature setting, staff working in the halls preferred cooler temperatures as they had full personal protective equipment on. It was important to strike a balance among different needs by fine-tuning the system from time to time.
Striving for excellence, Mr Wong always seeks to improve the air-conditioning system. “We hope to develop a technical solution, which will enable the air-conditioning system to quickly switch between running on a thermal energy storage system and operating on a round-the-clock basis for emergencies, just by tapping a button,” Mr Wong indicated he would continue to work towards this goal.
An Unusual Trip: Flying to Austria for Testing Aircraft Rescue and Firefighting Vehicles
Mr Wong Yu-hong, Simon (2nd right) and his team flew to Austria in early 2022 to support the Fire Services Department in testing and commissioning the Aircraft Rescue and Firefighting vehicles. The trip was full of obstacles with severe weather in Austria and disruptions to the team’s itinerary due to the epidemic. Nevertheless, the team managed to overcome all difficulties and ensured that the vehicles were delivered on time.
A new fleet of 14 advanced Aircraft Rescue and Firefighting (ARFF) vehicles will be deployed at the third runway of the Hong Kong International Airport (HKIA). Mr Wong Yu-hong, Simon, an engineer in the Security and Vehicle Services Division, was responsible for the procurement of the relevant vehicles. Experienced in vehicle procurement, he participated in every stage of the procurement exercise, from tendering to testing and commissioning of the new fleet.
Since some of the ARFF vehicles procured were manufactured in Linz, Austria, equipment checks and on-site performance tests had to be conducted there for the identification of any defects and prompt rectification. In view of this, Mr Wong led three colleagues from the EMSD to form a team with the representatives of the Fire Services Department (FSD), to fly to Linz for testing and receiving nine of the new vehicles.
The team arrived at the production plant in Linz in January 2022, in the depths of the Austrian winter. They stayed for a total of 22 days, working in two groups, each with two EMSD and two FSD colleagues.
“The plant rented a small airfield nearby for us to conduct the driving performance tests. We spent two full days working at the airfield under the temperatures of about -5°C, with snow and ground frost from time to time,” Mr Wong said. Testing of vehicles is usually avoided in European winters. Nevertheless, as the ARFF vehicles needed to be delivered to Hong Kong by May 2022, in order to allow sufficient time for final testing at HKIA before the third runway opened in July.
Another challenge during the trip was the strict inbound flight control measures implemented in Hong Kong in response to the epidemic. “As the trip was drawing to the end, we were stopped at the boarding gate at Vienna Airport and were told that flights to Hong Kong had been suspended for 14 days,” Mr Wong recalled. Fortunately, with the help of EMSD colleagues in Hong Kong, the team finally left Austria after being stranded for two days. Upon arrival in Hong Kong, the team immediately underwent 14 days of hotel quarantine.
From this unusual trip, Mr Wong has drawn insights. The planning and execution of the entire overseas trip was undoubtedly difficult and the flight suspension in the end posed further challenges to the trip. Nevertheless, he was grateful that the team had been calm and professional in the face of difficulties and crises. The trip also broadened his horizons in ARFF technologies, and he is now exploring with the FSD the potential of using hybrid or electric vehicles as firefighting and rescue vehicles.
Since some of the ARFF vehicles procured were manufactured in Linz, Austria, equipment checks and on-site performance tests had to be conducted there for the identification of any defects and prompt rectification. In view of this, Mr Wong led three colleagues from the EMSD to form a team with the representatives of the Fire Services Department (FSD), to fly to Linz for testing and receiving nine of the new vehicles.
The team arrived at the production plant in Linz in January 2022, in the depths of the Austrian winter. They stayed for a total of 22 days, working in two groups, each with two EMSD and two FSD colleagues.
“The plant rented a small airfield nearby for us to conduct the driving performance tests. We spent two full days working at the airfield under the temperatures of about -5°C, with snow and ground frost from time to time,” Mr Wong said. Testing of vehicles is usually avoided in European winters. Nevertheless, as the ARFF vehicles needed to be delivered to Hong Kong by May 2022, in order to allow sufficient time for final testing at HKIA before the third runway opened in July.
Another challenge during the trip was the strict inbound flight control measures implemented in Hong Kong in response to the epidemic. “As the trip was drawing to the end, we were stopped at the boarding gate at Vienna Airport and were told that flights to Hong Kong had been suspended for 14 days,” Mr Wong recalled. Fortunately, with the help of EMSD colleagues in Hong Kong, the team finally left Austria after being stranded for two days. Upon arrival in Hong Kong, the team immediately underwent 14 days of hotel quarantine.
From this unusual trip, Mr Wong has drawn insights. The planning and execution of the entire overseas trip was undoubtedly difficult and the flight suspension in the end posed further challenges to the trip. Nevertheless, he was grateful that the team had been calm and professional in the face of difficulties and crises. The trip also broadened his horizons in ARFF technologies, and he is now exploring with the FSD the potential of using hybrid or electric vehicles as firefighting and rescue vehicles.
Seven-day Race to Restart Cross-Boundary Railway Freight Service
During the fifth wave of COVID-19, cross-boundary cargo flow almost ground to a halt. To open up more logistics channels between Hong Kong and the Mainland, the then Transport and Housing Bureau (THB) liaised with the Mainland counterparts and, upon discussion, decided to reactivate the long-suspended cross-boundary railway freight service within seven days. Mr Yeung Chi-yuet, Chris, a senior engineer, and Ms Chan Ching-man, Kitty, an engineer, both under the Railways Branch (RB), led a team of ten to race against time to plan and conduct on-site railway safety testing in conjunction with the MTR Corporation Limited (MTRCL). Living up to expectation, the team managed to accomplish the “mission impossible” within an extremely short period of seven days, paving the way comprehensively for the resumption of the railway freight service. Eventually, the first Mainland freight train brought about 50 tonnes of much-needed anti-epidemic supplies to Hong Kong on 2 March 2022.
“The timeframe was very short. We only had a day or two to prepare after being told of the mission. The team was formed immediately and we readied ourselves to work round the clock to make all necessary arrangement for the prompt resumption of the railway freight service, on top of the routine duties of monitoring the MTRCL’s maintenance work. It was a monumental challenge indeed,” Ms Chan said.
The preparation work for the reactivation of the railway freight service was complicated as the current freight trains have been quite different from the previous ones since the railway freight service was suspended years ago. The first task was to conduct technical assessments on the Mainland freight trains designated for the Hong Kong run based on the train models, specifications and data confirmed by the Mainland, so as to ensure the compatibility between the Mainland freights trains and Hong Kong’s railway infrastructure for the Mainland freight trains to operate safely on the railways in Hong Kong. Meanwhile, the RB required the MTRCL to conduct not only maintenance and repair of the tracks in accordance with established mechanisms, but also a series of reviews on the tracks before the Mainland freight trains started their runs to Hong Kong, which included measuring the track gauges, checking the track condition and the integrity of the point switches, etc. The RB and the MTRCL personnel also carried out on-site thorough inspection of the approximately 1-km track between the boundary and the Lo Wu Marshalling Yard, and reviewed various measurement data repeatedly to ensure that the Mainland freight trains could operate safely on the railway infrastructure in Hong Kong.
Once the cargo containers were transported to the Lo Wu Marshalling Yard by the Mainland freight trains, they had to be lifted onto container trucks by cranes for local transportation and distribution of the supplies. However, the Yard was a MTRCL depot for stationing trains and covered with a network of overhead high voltage cables. Extra caution was called for in the lifting of the containers to avoid touching the cables and endangering the crane operators or potentially affecting the MTRCL’s train services. In view of the above, Mr Yeung demanded that the MTRCL should conduct a risk assessment of the crane operation and formulate risk mitigation measures and contingency plans. In the end, the electricity supply to the cables near the craning area was isolated, and the tracks were barricaded by stationary trains to prevent the cranes from straying onto the tracks accidentally and triggering electrical incidents.
Monitoring the testing of the signalling and communication systems was another major task. During the drills and the actual freight train operations, the RB deployed staff to the MTRCL’s Tsing Yi Control Centre and the Lo Wu Marshalling Yard to closely monitor the operation of the signalling system and the communication between the MTRCL and the Mainland train control centre to ensure that the signalling system functioned normally and the Mainland drivers operated the train according to the MTRCL’s arrangements on the Hong Kong tracks.
The usual practice in the past was to have an MTRCL driver get on the freight train and guide the Mainland driver to operate on the Hong Kong railway after the Mainland train had entered Hong Kong. However, the MTRCL drivers could not get on the train due to anti-epidemic control arrangements. The MTRCL had to arrange flag signalmen at designated locations at the boundary, the Marshalling Yard and along the tracks, to manually guide the Mainland drivers where to go and where to stop by flags, and perform visual checks to ascertain that the trains were running normally on the tracks. Since the scheduling of the Mainland freight trains was irregular depending on a host of factors, the MTRCL had to put flag signalmen and other staff members on stand-by in shifts. Accordingly, the RB also arranged staff to monitor the freight train operation and the functioning of various railway systems at the Tsing Yi Control Centre and the Lo Wu Marshalling Yard.
Despite the overwhelming challenges, Mr Yeung and his team managed to complete all preparations within seven days against all the odds. Upon the satisfactory trial run of an empty Mainland train operating to Hong Kong on 1 March, the cross-boundary railway freight service was officially reactivated the following day.
“Having to quickly restart the long-suspended cross-boundary railway freight service was an enormous undertaking. We made speedy responses and brought our team together for preparations, risk assessments and formulation of contingency plans, putting all preparation plans in place through working closely with the MTRCL. Every day was packed with lots of things to do, be it monitoring the testing, inspecting the track condition and attending regular meetings to communicate closely with the THB, other government departments, the MTRCL and the Mainland counterparts. That said, we rose to challenges with determination and perseverance and pulled out all the stops for the mission, and our Mainland counterparts were equally determined to make it work. With the concerted effort of all, the cross-boundary railway freight service was put back on track as scheduled. It was an honour to be able to contribute to Hong Kong during the epidemic,” Mr Yeung said.
With the seven-day endeavours, the RB and MTRCL are ready to reactivate the cross-boundary railway freight service anytime should Hong Kong faces cross-boundary logistics bottlenecks again. Meanwhile, the RB and the MTRCL have even put in place the option of transporting livestock from the Mainland to the Sheung Shui Slaughterhouse by using the Mainland freight trains, just in case it is needed.
The preparation work for the reactivation of the railway freight service was complicated as the current freight trains have been quite different from the previous ones since the railway freight service was suspended years ago. The first task was to conduct technical assessments on the Mainland freight trains designated for the Hong Kong run based on the train models, specifications and data confirmed by the Mainland, so as to ensure the compatibility between the Mainland freights trains and Hong Kong’s railway infrastructure for the Mainland freight trains to operate safely on the railways in Hong Kong. Meanwhile, the RB required the MTRCL to conduct not only maintenance and repair of the tracks in accordance with established mechanisms, but also a series of reviews on the tracks before the Mainland freight trains started their runs to Hong Kong, which included measuring the track gauges, checking the track condition and the integrity of the point switches, etc. The RB and the MTRCL personnel also carried out on-site thorough inspection of the approximately 1-km track between the boundary and the Lo Wu Marshalling Yard, and reviewed various measurement data repeatedly to ensure that the Mainland freight trains could operate safely on the railway infrastructure in Hong Kong.
Once the cargo containers were transported to the Lo Wu Marshalling Yard by the Mainland freight trains, they had to be lifted onto container trucks by cranes for local transportation and distribution of the supplies. However, the Yard was a MTRCL depot for stationing trains and covered with a network of overhead high voltage cables. Extra caution was called for in the lifting of the containers to avoid touching the cables and endangering the crane operators or potentially affecting the MTRCL’s train services. In view of the above, Mr Yeung demanded that the MTRCL should conduct a risk assessment of the crane operation and formulate risk mitigation measures and contingency plans. In the end, the electricity supply to the cables near the craning area was isolated, and the tracks were barricaded by stationary trains to prevent the cranes from straying onto the tracks accidentally and triggering electrical incidents.
Monitoring the testing of the signalling and communication systems was another major task. During the drills and the actual freight train operations, the RB deployed staff to the MTRCL’s Tsing Yi Control Centre and the Lo Wu Marshalling Yard to closely monitor the operation of the signalling system and the communication between the MTRCL and the Mainland train control centre to ensure that the signalling system functioned normally and the Mainland drivers operated the train according to the MTRCL’s arrangements on the Hong Kong tracks.
The usual practice in the past was to have an MTRCL driver get on the freight train and guide the Mainland driver to operate on the Hong Kong railway after the Mainland train had entered Hong Kong. However, the MTRCL drivers could not get on the train due to anti-epidemic control arrangements. The MTRCL had to arrange flag signalmen at designated locations at the boundary, the Marshalling Yard and along the tracks, to manually guide the Mainland drivers where to go and where to stop by flags, and perform visual checks to ascertain that the trains were running normally on the tracks. Since the scheduling of the Mainland freight trains was irregular depending on a host of factors, the MTRCL had to put flag signalmen and other staff members on stand-by in shifts. Accordingly, the RB also arranged staff to monitor the freight train operation and the functioning of various railway systems at the Tsing Yi Control Centre and the Lo Wu Marshalling Yard.
Despite the overwhelming challenges, Mr Yeung and his team managed to complete all preparations within seven days against all the odds. Upon the satisfactory trial run of an empty Mainland train operating to Hong Kong on 1 March, the cross-boundary railway freight service was officially reactivated the following day.
“Having to quickly restart the long-suspended cross-boundary railway freight service was an enormous undertaking. We made speedy responses and brought our team together for preparations, risk assessments and formulation of contingency plans, putting all preparation plans in place through working closely with the MTRCL. Every day was packed with lots of things to do, be it monitoring the testing, inspecting the track condition and attending regular meetings to communicate closely with the THB, other government departments, the MTRCL and the Mainland counterparts. That said, we rose to challenges with determination and perseverance and pulled out all the stops for the mission, and our Mainland counterparts were equally determined to make it work. With the concerted effort of all, the cross-boundary railway freight service was put back on track as scheduled. It was an honour to be able to contribute to Hong Kong during the epidemic,” Mr Yeung said.
With the seven-day endeavours, the RB and MTRCL are ready to reactivate the cross-boundary railway freight service anytime should Hong Kong faces cross-boundary logistics bottlenecks again. Meanwhile, the RB and the MTRCL have even put in place the option of transporting livestock from the Mainland to the Sheung Shui Slaughterhouse by using the Mainland freight trains, just in case it is needed.
Vaccine Fridge Monitoring System Enabled by Technology and Talent
To remotely monitor the medical fridges and vaccines, Mr Yip Wai-tong, Wallace, an engineer, and his team have actively provided uninterruptible power supply for the integrated Fridge Monitoring System at the Community Vaccination Centres. Their effort to safeguard the proper storage of vaccines was proved effective.
The COVID-19 Vaccination Programme (CVP) is vital to Hong Kong’s anti-epidemic strategy and an integrated Fridge Monitoring System (iFMS) developed by the EMSTF also plays a crucial role in the CVP.
Mr Yip Wai-tong, Wallace, an engineer of the Health Sector Division, led a team to design and install the iFMS at all the Community Vaccination Centres (CVCs) in 18 districts across the territory in early 2021. The system was proved successful in ensuring that COVID-19 vaccines are stored safely at proper low temperature.
The iFMS was developed as urgently requested by the Centre for Health Protection to tie in with the Government’s plan to launch the CVP in the same year. Leveraging his experience in converting general wards into second-tier negative pressure wards and installing numerous Mobile Modular High Efficiency Particulate Air Filter Units at public hospitals, Mr Yip led his team to spring into action for the development of the system. After considering the actual circumstances, the team decided to use narrow-band Internet of Things (IoT) technology to monitor medical fridges for vaccine storage in the CVCs. In other words, the IoT would operate on existing mobile networks which had a high coverage already. Some suggestions or requests from users, such as auto-generation of a simple report every morning, were promptly accepted to improve the system.
The iFMS is designed to monitor the fridge temperature and the ambient temperature and humidity at the CVC. Meanwhile, it can also detect faults in the fridge, the power supply system and other E&M equipment at the CVCs. Through IoT technology and sensors, all data are transmitted to the Regional Digital Control Centre (RDCC) at the EMSD Headquarters and the RDCC dashboard at the Central Government Offices for round-the-clock monitoring. If any abnormalities are detected, SMS alert messages will be sent to the responsible officers and stakeholders immediately.
“We take these alerts seriously and always arrange colleagues to call the responsible officers in person to ensure that the messages have been got through,” Mr Yip said. He and his colleagues have on several occasions rushed to the centres to personally attend to the supply issues on site after midnight.
“One of the insights gained from the iFMS experience is the importance of having both the ‘technology reserve’ and ‘talent reserve’ for the timely deployment of innovative projects,” Mr Yip said. “With technical expertise and a positive mindset, one will have the confidence to take on challenges.”
Mr Yip Wai-tong, Wallace, an engineer of the Health Sector Division, led a team to design and install the iFMS at all the Community Vaccination Centres (CVCs) in 18 districts across the territory in early 2021. The system was proved successful in ensuring that COVID-19 vaccines are stored safely at proper low temperature.
The iFMS was developed as urgently requested by the Centre for Health Protection to tie in with the Government’s plan to launch the CVP in the same year. Leveraging his experience in converting general wards into second-tier negative pressure wards and installing numerous Mobile Modular High Efficiency Particulate Air Filter Units at public hospitals, Mr Yip led his team to spring into action for the development of the system. After considering the actual circumstances, the team decided to use narrow-band Internet of Things (IoT) technology to monitor medical fridges for vaccine storage in the CVCs. In other words, the IoT would operate on existing mobile networks which had a high coverage already. Some suggestions or requests from users, such as auto-generation of a simple report every morning, were promptly accepted to improve the system.
The iFMS is designed to monitor the fridge temperature and the ambient temperature and humidity at the CVC. Meanwhile, it can also detect faults in the fridge, the power supply system and other E&M equipment at the CVCs. Through IoT technology and sensors, all data are transmitted to the Regional Digital Control Centre (RDCC) at the EMSD Headquarters and the RDCC dashboard at the Central Government Offices for round-the-clock monitoring. If any abnormalities are detected, SMS alert messages will be sent to the responsible officers and stakeholders immediately.
“We take these alerts seriously and always arrange colleagues to call the responsible officers in person to ensure that the messages have been got through,” Mr Yip said. He and his colleagues have on several occasions rushed to the centres to personally attend to the supply issues on site after midnight.
“One of the insights gained from the iFMS experience is the importance of having both the ‘technology reserve’ and ‘talent reserve’ for the timely deployment of innovative projects,” Mr Yip said. “With technical expertise and a positive mindset, one will have the confidence to take on challenges.”
Leveraging Digital Tools to Support the LegCo Election
Mr Yuen Wai-yip, Lobee, a senior engineer, led his team members to deploy new innovation and technology tools in the 2021 Legislative Council (LegCo) General Election to enhance work efficiency and effectiveness. Despite the immense pressure, they devoted their best efforts and completed all the tasks on time, contributing to the smooth running of the election.
The EMSTF has always provided E&M support to LegCo elections, for example, through the provision of electricity and lighting at polling stations. The latest LegCo General Election held on 19 December 2021 was no exception. Mr Yuen Wai-yip, Lobee, a senior engineer of the General Engineering Services Division (GESD), led his team to provide relevant support to the Registration and Electoral Office (REO) and opened up a new digital era for holding elections in Hong Kong.
Preparations for the 2021 LegCo General Election began soon after the District Council election in 2019. The efforts were translated into several “firsts” in this LegCo election, including the first-ever use of an Electronic Poll Register System to issue ballot papers at 693 polling stations and the adoption of a video recording system to monitor the counting process from 11:00 p.m., when 620 polling stations were converted to counting stations. We also rolled out a GESD-developed dashboard at the Emergency Response Centre in our headquarters for round-the-clock monitoring for the election from 18 to 20 December.
The dashboard was particularly effective in monitoring the works of contractors in the run-up to the election day. As each contractor was required to report the progress of their designated tasks via mobile devices, the dashboard was continually updated, giving Mr Yuen and his team access to a real-time overview of the progress of works at all polling stations as displayed on an interactive map of Hong Kong. The system also enabled them to readily retrieve the information of the responsibilities of contractors and their contact details for prompt follow-up. Given the large number of polling stations and contractors, this timely and efficient oversight was not possible in the past when progress updates solely relied on telephone calls.
Speaking of the challenges which the team faced, Mr Yuen cited the short period of time allowed to set up the video recording system for monitoring the counting process. “As the polling stations closed at 10:30 p.m., we only had 30 minutes to set up the device, so that video recording could begin at 11:00 p.m. sharp when the counting process commenced,” he said.
Mr Yuen attributed the team’s success to its rich work experience accumulated from previous elections and strong support from the senior management, as well as over 1600 colleagues from various divisions of the EMSD who rendered assistance on the election day. “The REO was most impressed with the dashboard, which we plan to deploy with other innovation and technology tools in the District Council election in 2023 and the next LegCo election in 2025 after further refinement,” he said.
Preparations for the 2021 LegCo General Election began soon after the District Council election in 2019. The efforts were translated into several “firsts” in this LegCo election, including the first-ever use of an Electronic Poll Register System to issue ballot papers at 693 polling stations and the adoption of a video recording system to monitor the counting process from 11:00 p.m., when 620 polling stations were converted to counting stations. We also rolled out a GESD-developed dashboard at the Emergency Response Centre in our headquarters for round-the-clock monitoring for the election from 18 to 20 December.
The dashboard was particularly effective in monitoring the works of contractors in the run-up to the election day. As each contractor was required to report the progress of their designated tasks via mobile devices, the dashboard was continually updated, giving Mr Yuen and his team access to a real-time overview of the progress of works at all polling stations as displayed on an interactive map of Hong Kong. The system also enabled them to readily retrieve the information of the responsibilities of contractors and their contact details for prompt follow-up. Given the large number of polling stations and contractors, this timely and efficient oversight was not possible in the past when progress updates solely relied on telephone calls.
Speaking of the challenges which the team faced, Mr Yuen cited the short period of time allowed to set up the video recording system for monitoring the counting process. “As the polling stations closed at 10:30 p.m., we only had 30 minutes to set up the device, so that video recording could begin at 11:00 p.m. sharp when the counting process commenced,” he said.
Mr Yuen attributed the team’s success to its rich work experience accumulated from previous elections and strong support from the senior management, as well as over 1600 colleagues from various divisions of the EMSD who rendered assistance on the election day. “The REO was most impressed with the dashboard, which we plan to deploy with other innovation and technology tools in the District Council election in 2023 and the next LegCo election in 2025 after further refinement,” he said.
Copyright © 2022 Electrical and Mechanical Services Department. All Rights Reserved.